Enhancing Food and Beverage Manufacturing with Motion Control
September 9, 2024
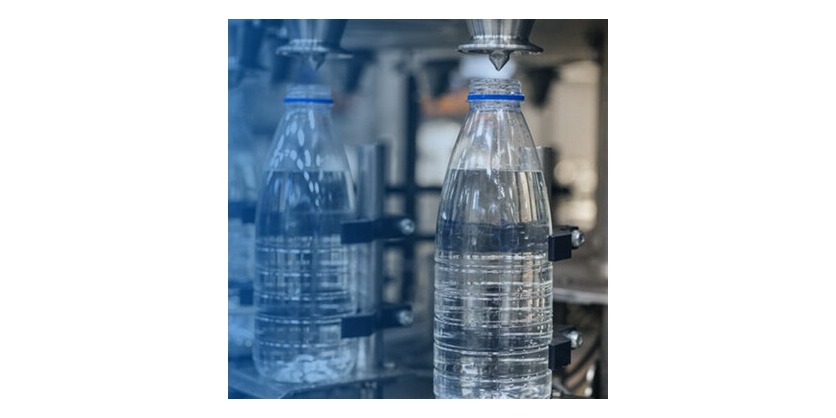
Reliability in automation motion control is crucial for original equipment manufacturers (OEMs), directly influencing machine efficiency and production costs
Key factors of motion control, such as servo position accuracy, trajectory repeatability, and system efficiency are essential for maintaining high performance and competitiveness. OEMs must balance the addition of advanced features with profitability, ensuring their equipment meets customer expectations and optimizes production processes.
This blog will explore the lifecycle of food and beverage manufacturing equipment—from design to production—highlighting best practices in motion control that enhance reliability and system performance, while keeping future technology integrations seamless and non-intrusive.
Strategic Design in Automation Systems
In designing automation control systems for food and beverage facilities, it’s crucial to prioritize accuracy, repeatability, and efficiency from the outset. The selection of network protocol, such as EtherCAT®, significantly influences the system’s complexity, performance, and long-term operational costs. EtherCAT® enhances communication to ensure deterministic communication and reducing jitter that can affect motion control. This is vital in applications like sealing, where precision directly impacts material waste and customer satisfaction.
For trajectory repeatability, EtherCAT® ensures precise, collision-free delivery of commands, crucial for applications requiring consistent precision over numerous cycles, such as bottling and sterilization systems. It offers various modes—Free Run, Synchronous, and Time Stamp—to match specific repeatability needs, synchronizing operations to achieve microsecond precision.
Regarding system efficiency, EtherCAT® supports quick design and scalability. Its global openness allows interoperability among different manufacturers, fostering a consistent adoption rate and providing a competitive edge. Early adopters have benefited from sustained growth and avoided costly redesigns, demonstrating EtherCAT®’s role in sustaining automation systems.
Streamlining Commissioning for Enhanced Machine Performance
Commissioning robust motion control systems is crucial for meeting customer expectations by identifying and eliminating inefficiencies before deployment, ensuring optimal machine performance and reducing risks at the user’s facility. This process can occur during the runoff stage or alongside machine builds without physical hardware, effectively reducing production time while maintaining quality. Selecting the right servo size is also vital for cost-effectiveness and accuracy, with an integrated development environment on a unified automation platform streamlining servo choices and eliminating the need for additional software.
Accurate motion trajectories are essential for efficient operation, influencing throughput, crash risks, and quality. Simulating these trajectories in programming software mitigates risks and ensures the equipment performs as expected. Additionally, using 3D simulation during commissioning allows for the entire assembly process to be visualized and tested, verifying motion and safety protocols. This method not only ensures safety and optimizes procedures but also enhances the likelihood of exceeding performance standards before physical assembly begins, paving the way for successful deployment and operation.
Enhancing Production with Advanced Automation
Investing in original equipment design and thorough commissioning is crucial for manufacturers aiming to secure repeat success, as the performance, scalability, uptime, and data capabilities of equipment significantly impact customer satisfaction and future business potential. High-performance automation platforms enhance this by offering extensive modularity and supporting a wide range of industrial protocols, which facilitates the integration of new technologies and meets evolving industry standards and consumer demands, especially in dynamic sectors like food and commodity manufacturing.
Moreover, automation systems improve operational repeatability and fault diagnosis by autonomously capturing and replaying production events, allowing quick pinpointing and verification of downtime causes without disrupting production. The integration of OPC UA™ servers in controllers standardizes secure communication with field devices, enhancing security and supporting SCADA systems to meet communication needs effectively. This setup not only prevents unauthorized access but also strengthens the connection between manufacturers and users, fostering continuous improvement and opening up new opportunities for equipment enhancement.
Sustaining Automation Equipment
To remain competitive, manufacturers must focus on robust design, reliable commissioning, and efficient troubleshooting, adhering to increasingly stringent industry standards. Utilizing all-in-one automation platforms that support global industrial protocols can simplify design, streamline commissioning, and enhance data management during production. As the food and beverage industry evolves, leveraging advanced motion control technologies today prepares manufacturers for future challenges, ensuring a sustainable competitive edge.
More Information
Explore Omron’s reliable All-in-One automation platform
Related Story
Omron’s Advanced Safety Services 101
In any industrial setting, safety is of the utmost importance. Omron Offers Advanced Safety Services to help you and your staff navigate the challenges of complex industry standards and compliance regulations. They also can provide machine safety technology to protect your people and equipment while maximizing productivity.
Did you know that Omron’s safety training and services encompass safety compliance education, risk assessment, and compliance reviews led by certified safety engineers? Their enabling technologies Include Functional Safety Training, Machine Safety Risk Assessments, Machine Safeguarding Solutions, Lockout/Tagout Procedures, Arc Flash Assessment, And Machine Safety. In this blog, Omron experts provide details about how they can help businesses safeguard workers, maintain stable operations, and prolong equipment life cycles.