Mazak: Beat the Manufacturing Clock With Multi-Tasking
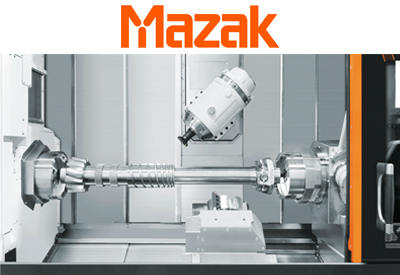
Novemver 20, 2018
The reduction of long lead times won’t be achieved by simply reducing machining cycle times; shaving seconds off a part’s in-cut time is nothing compared to eliminating entire steps in the process, especially time-consuming tasks that require manual intervention. That’s why manufacturers turn to Mazak and our innovative Multi-Tasking machines, which bring multiple machining processes into one machine platform to achieve single-setup manufacturing.
Our increasingly complicated world requires equally complicated building blocks, and to cut these parts, manufacturers have stretched out lead times and added steps to their processes. Yet when the time comes to optimize part-production operations, manufacturers rarely think about the days, weeks or months that elapse as raw material becomes a finished part. Instead, the industry often focuses on the minutes and seconds of in-cut time, the so-called “value-added” time.
Consider the production of aerospace landing gear components such as pistons and cylinders that require high-quality surface finishes, tight tolerances and intricate features. With conventional machine tools and processes, each piston and cylinder can take up to six weeks to finish, with more than 50 hours of machining – with six separate set ups – and 22 hours of manual benchwork. After incorporating an INTEGREX e-670H Multi-Tasking Machining Center from Mazak, however, it now takes a mere 15 hours of in-plant time to complete a part, with only 13 hours of machining time in two set ups and two hours of manual benchwork.
Notice that the reduction of machining time – a 13% decrease – is far less than the reduction in overall in-plant time, an incredible 98.5% decrease. In addition to the reduction of manual benchwork, the bulk of this decrease comes from the elimination of four setup operations and the amount of time it took to move parts from turning machines to other secondary operations. Not only did the INTEGREX e-670H’s milling functionality replace the need for a forging flash, but DONE IN ONE® part production and single-setup operations prevent the risk of damaging parts inside and outside machines.
The trick then becomes selecting the right machine from Mazak’s five levels of Multi-Tasking. It’s useful to consider your parts and how much time they spend in milling and turning machines. Do you need a milling machine with turning functionality or vice versa? Can you achieve the best cost effectiveness with milling and turning alone, or do you require more advanced features available in the HYBRID Multi-Tasking family of machines? Let your parts guide this process to achieve the best results.
In the end, Multi-Tasking technology may be inside the machine, but it’s when the doors are open that all the time gets saved. Fewer set ups mean fewer opportunities for scrapping parts while moving them from machine to machine or building to building. Indeed, shops waste enormous amounts of time simply leaving workpieces on a shelf as they wait for the next step in a lengthy process. All this slack time can be eliminated in one fell swoop: install a Multi-Tasking machine and watch your productivity soar.