Machine Man Reflects on 50 Years In a Challenging But Rewarding Field
December 18, 2024
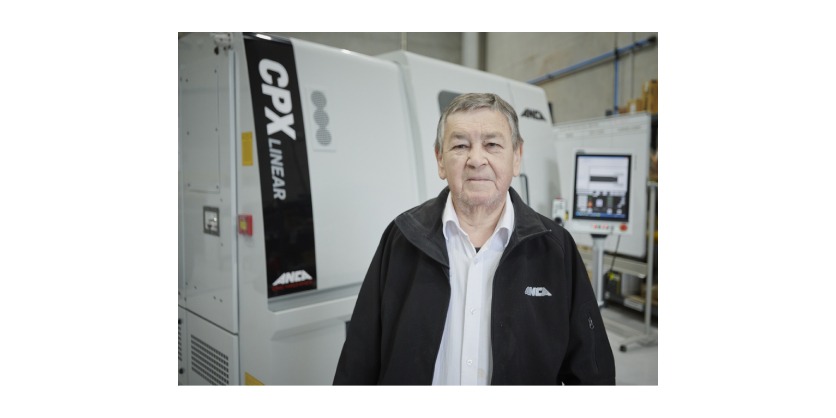
Pat McCluskey’s machine design and build experience at ANCA has fuelled manufacturing exports for Australia for half a century
For a half-century, ANCA has made the machines that make the tools that make the world go around.
One half of its founding pair, Pat McCluskey, has designed many grinding machine tools in that time.
He says that two things have remained focal when designing a machine: the customer and their expectations, and the manufactured cost.
It is never the result of a whim. It always follows information fed back through a two-way communication process on customer challenges, and meticulous market research, which is then presented to Pat’s team. Then the design gets underway.
If it sounds straightforward, it never is.
“To design a completely new machine that nobody has seen before is a complex task,” explains McCluskey.
ANCA tool and cutter grinding machines are underpinned by world-leading engineering and skills so specialized they often have to be fostered in-house. Their approach to innovation includes machines, controls, software and related accessories such as robots, and their vertical alignment has kept them ahead in a challenging field where there are few serious rivals.
A selection of world firsts over 50 years includes a probe for digitizing tools, first modem for support and diagnostics in a machine, and the first full and true 3D simulation of the grinding process.
Progress from top to bottom
“For some reason we seem to be the only grinding machine manufacturer for tool grinding that uses a polymer concrete base on their machine,” says McCluskey of one thing done differently.
First introduced in the TG7 machine, released in 1990, polymer concrete provides a very stable base for machines, damping out any vibrations. The ability to absorb heat minimizes any expansion and contraction which might sacrifice grinding accuracy.
McCluskey looked into what’s now called ANCAcrete in the 1980s as an alternative to cast iron, and a way to avoid dependency on foundry providers.
Self-reliance is crucial to the company’s dominance of its market, according to McCluskey.
Perhaps most important is development of its CNC and servo systems, as well as software, in-house. Competitors are dependent on pre-packaged CNC controls, and ANCA is the only tool grinding machine builder that makes its own control.
“So the Germans and the Swiss tend to buy the Japanese or the German CNC and try their best to adapt it to their machine,” explains McCluskey.
“And it’s a clumsy fit and they don’t do the in-depth development in the software that we do because they can’t get access to the software… it’s all locked off to them.”
Notable recent innovations are credited to Dr. Kotler Tee, Technical Leader – Servo Control at ANCA.
One innovation has enabled servo system resolution of a single nanometre and is being rolled out to new machines in the ULTRA platform
“He rewrote the servo algorithms in the servo drives in the CNC to increase the resolution,” says McCluskey.
“To explain this achievement in layman’s terms, take a 300 millimeter ruler and look at a pair of the smallest lines; the distance is 1 millimeter.
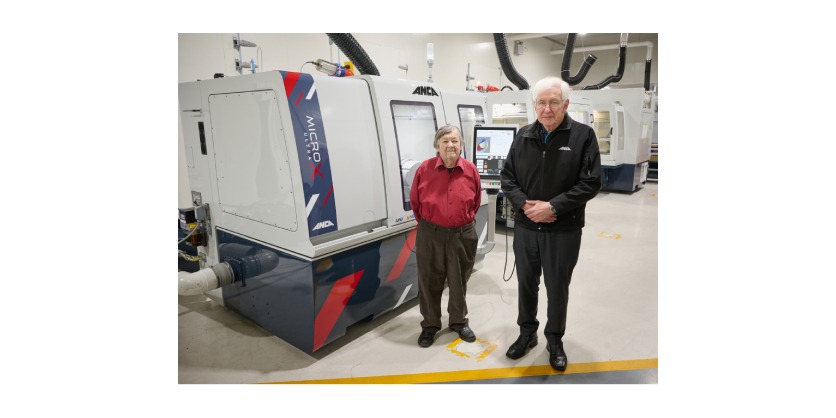
“Now divide that distance by 1,000, now you have a distance of 1 micron. In your mind, now divide that micron by 1,000, the result is now equal to 1 nanometre.”
“Designing the ULTRA platform has been a design process from the ground up bringing sophisticated elements to the art of grinding.”
Others include breakthrough features available on the newly released MicroX ULTRA, a six-axis tool grinder that premiered at EMO in 2023.
Through the years
The first four years of ANCA involved retrofitting CNC controls to other people’s equipment, such as special purpose machinery, lathes and mills.
What McCluskey estimates was the most significant non-technical development came in 1978.
Their major OEM at the time, Laser Lab, set up in Detroit, with ANCA sending young engineer John Roberts to work at the facility.
Roberts took it upon himself to book a booth at a trade show and display an ANCA CNC. According to Roberts, there was a crowd at the booth and significant interest, and the suggestion that ANCA make a CNC tool grinder to improve on the less-than-spectacular machines available at the time.
“The die was cast,” McCluskey says.
A further important non-technical development was the Australian recession in 1982.
“We didn’t want to continue to sell in Australia because of the ups and downs of the markets; we wanted to cover ourselves,” he adds.
“And the American market seemed to be the market for us, and we only needed a small percentage of that market and that was enough – more than what we could handle. And we got it.”
“So if we hadn’t made that decision, we’d have gone bust.”
50 years later, 98% of revenues are from exports, with customers in over 45 countries.
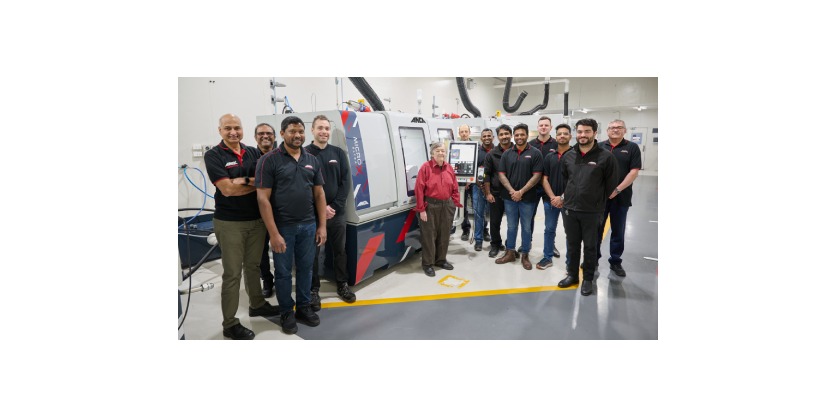
ANCA employs over 1,200 worldwide, with offices in the UK, Germany, China, Thailand, India, Japan, Korea, Brazil, Mexico, Italy, Türkiye, and the USA.
While some production occurs in Thailand and Taiwan, the heart of the company, its headquarters and innovation and manufacturing base – remains in the Melbourne suburb of Bayswater North.
Nearly a tenth of revenues are spent on R&D.
“ANCA is my life and I’m proud to be celebrating its 50th anniversary and that we have been able to build the company to the size that it is and with world recognition,” adds McCluskey.
The opportunity for engineers to work hard on complicated, world-leading, meaningful problems goes back to the company’s roots.
“I think it’s because Pat (Boland – ANCA co-founder) and I had to work so bloody hard in the beginning when we almost went broke and we’ve continued to do nothing but work hard like that ever since,” he says.
“And the people who work with us get a hell of a buzz out of working hard too.”
Staying sharp and skilled up
There is something of an “open university” nature to ANCA, believes McCluskey.
It attracts a lot of bright young people who are motivated by technical challenges more than money, and in seeing their work embodied in a physical product (which they can’t always do at a university.)
“At university they can study theory as long as they want, but at the end of that theory, they move on to something else,” suggests McCluskey.
“Whereas here at the end of their theory, they’ve got a new machine sitting on the floor and they’ve written the software for it, or they’ve written the code for the display unit.”
Attracting clever engineering graduates has not been a problem, he adds,
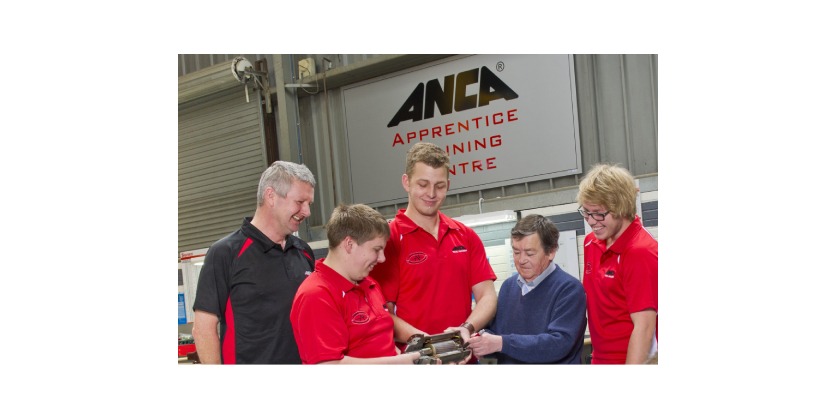
“It doesn’t take long for a group of students at a technical university to learn about ANCA. We don’t have to tell them, they learn by talking amongst themselves and it’s a great place for them to work,” McCluskey says.
“They get great pay, they get well looked after, and above all, they get respected by their peers, they get respected by the company owners. They don’t get that working for a big corporate.”
As the only organization in Australia that manufactures machine tools, and with a demand for very high-level assembly workers, the only real option for finding suitably skilled tradespeople is to train them in-house.
Another feature of ANCA is upward mobility for those who have apprenticed, with many going on to senior roles. When they move up or out, they must be replaced.
“So you train these guys to work in the high-precision assembly shop, but a few years later you find that they’re overseas somewhere, then they’ve got to be replaced. So there’s a continuous need for them,” McCluskey explains.
“We can’t send them to the technical colleges because they don’t have a program to train machine tool fitting. And you can go and look at other companies, but there isn’t any other company like ANCA.”
ANCA has been taking on apprentices and formalized its program in 2011. McCluskey wrote the original course material.
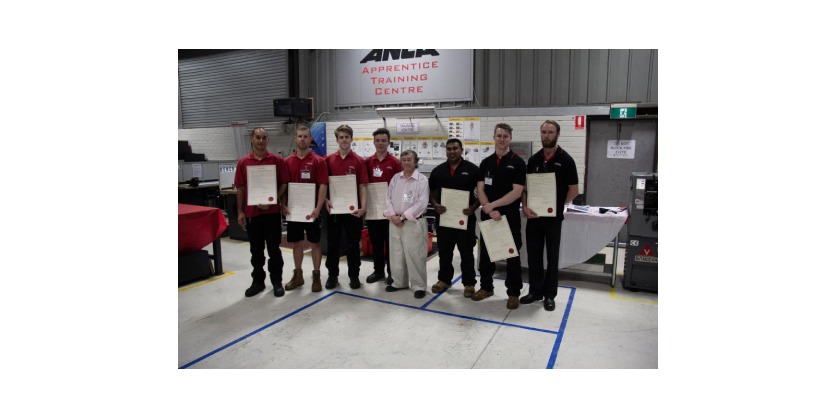
“I was reasonably happy when I found out that we’d have to create our own apprentice training school,” he recalls.
“Because it was something in the back of my mind that I had always wanted to do anyway.”
McCluskey began his career with an apprenticeship at the Commonwealth Department of Supply, where he met ANCA co-founder Pat Boland (then a cadet engineer at University of Melbourne) in 1968.
He is happy with the results of the company’s program and its ability to both create niche skillsets at ANCA as well as interesting futures for young employees.
“People say that the young kids of today are pretty useless. Well, I’d say they’re not. I’d say if you’re given the right kind of training, the right kind of opportunity, you’ll get the best out of them,” McCluskey says.
“One guy this year finished his time, got his indentures released at the last presentation night, and two nights later he was on a plane to America. He’s going to work in the American office in Detroit. What an opportunity for a kid!”
More Information
Related Story
ANCA Celebrates 50th Anniversary and Contributions to the High-Precision Tool-Cutting Industry
ANCA was founded by Pat Boland, an Electrical Engineer, and Pat McCluskey, an Industrial Electronics Engineer in 1974, in Melbourne Australia. For 50 years, the company expanded globally. Today they employ over 1200 people worldwide and serve customers in more than 46 countries. Pat Boland, co-founder of ANCA, discusses this journey and some of the innovations they have contributed to the high-precision tool-cutting industry.