Lockout/Tagout Procedures – What You Need to Know
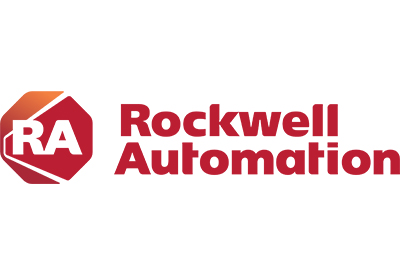
October 28, 2021
No one should get hurt at work.
Unfortunately, in 2019 there were 5,333 worker deaths in the U.S. – an average of 15 deaths every day. While many types of incidents result in worker injuries and fatalities, among the most frequently cited are lockout/tagout violations.
As with most work-related incidents, lockout/tagout related accidents and deaths are avoidable. In fact, according to the Occupational Safety and Health Administration (OSHA), the implementation of lockout/tagout standards helps prevent an estimated 120 fatalities and 50,000 injuries every year in the US.
A compliant lockout/tagout program includes implementing and practicing five OSHA mandated components: corporate policy, machine-specific procedures, training, locks and devices, and annual audits.
Today, we’re going to take a closer look at a core component: machine-specific lockout/tagout procedures.
What Are Lockout/Tagout Procedures?
Lockout/tagout procedures are a way of helping prevent injuries, even fatal ones, related to hazardous energy. Put simply, a lockout/tagout procedure is an instructional document designed to instruct authorized employees on how to lockout a specific machine. Lockout can be defined as isolating energy sources with a lock providing physical protection, and with every lock accompanied by an information tag. Tagout is isolating energy that cannot be physically locked with an information tag to convey who isolated the energy and to warn against reenergization.
Both steps are vital for controlling hazardous energy and can help prevent permanent injuries or death from electrocution or other dangerous sources of energy like compressed air or pressurized steam. It’s also important that lockout/tagout happens before maintenance begins on any equipment, so it doesn’t pose a danger to anyone working around it.
By using a lockout/tagout procedure, employees can help protect themselves from unexpected re-energization or release of stored energy. In addition, companies can find greater efficiency and productivity through these procedures.
Components of a Compliant Lockout/Tagout Procedure
To verify that employees are using a compliant procedure, companies should include several components. For example, all procedures should include step-by-step directions to ensure that all hazardous energy is turned off and isolated, including electrical sources and mechanical power sources. They should also have details on how to prevent accidental re-energization of lockout devices.
The information required on each procedure, according to OSHA standards, is as follows:
- – A statement of the intended use of the procedures
- – Methods for shutting down the machine and controlling hazardous energy
- – Steps for the placement and removal of lockout locks, tags, and devices, and;
- – Ways to verify that the machine has been properly locked out
Companies can develop these directions by reviewing previous examples from safety professionals or trade groups. Trade associations like the National Safety Council offer training sessions, videos, and additional resources for developing these procedures. Companies that plan on training workers or having third parties like Rockwell Automation come in and perform work, can have their lockout procedures independently audited.
Who Must Be Trained on Lockout/Tagout Procedures?
Anyone who performs maintenance, service, or repair work on a machine with hazardous energy must be trained on how to lock out and tag out. In addition, anyone who supervises employees must also be trained on lockout/tagout procedures. When it comes to who needs training in your workplace, employers should take into account OSHA 1910.147 section (c)(7.).
These requirements state that an employer must confirm that each employee who performs machine servicing involving hazardous energy receives initial training before being assigned work duties involving lockout/tagout procedures. They also require your employer to provide a retraining session for all authorized and affected employees whenever there is a change in their job assignments, a change in machines, equipment or process that present a new hazard, or where there is a change in the energy control procedures.
By OSHA standards, an authorized employee is a person who locks or tags out equipment to perform servicing or maintenance. This includes employees who:
- – Perform energy source isolation
- – Implement lockout and/or tagout on machines or equipment
- – Dissipate potential (stored) energy
- – Verify energy isolation
- – Implement actions to release LOTO
- – Test or position machines or equipment
While OSHA requires that all authorized and affected employees receive adequate training, training facilitation can be customized to any employer’s needs. Training facilitation can be customized to a facility’s precise needs and conducted in-person/instructor-led, online, or with videos.
Best Practices for Creating Lockout/Tagout Procedures
Create procedures that are specific to your company. To do so, you must first identify all machines and equipment for which energy control is necessary. Lockout/tagout procedures must be created for machines or equipment with two or more sources of hazardous energy. This includes electricity greater than 50V, compressed air, liquids, gases, fuel, steam, hydraulics, and also sources that need to be dissipated like kinetic (flywheels for example), gravity (like a raised overhead door), springs, thermal (a hot boiler for example) or capacitance (found in every Variable Frequency Drive unit).
For each piece of equipment identified on your list, you will need to create a procedure that addresses energy control during maintenance and repair activities. For example, all identified hazardous energy should be controlled before performing tasks requiring entry into hazardous areas.
Example Types of Lockout/Tagout Procedures
Different types of lockout/tagout procedures depend on their uses and requirements. The examples of lockout/tagout procedures provided below are used in various industries, including the chemical industry, refinery industry, manufacturing industry, petrochemical industry, and others.
Text-Based Procedures
Text-based formats are enough for many companies to meet minimum lockout/tagout compliance standards; however, these programs often prove cumbersome to maintain as the company grows. Text-based procedures are becoming less common as companies begin to realize the many advantages of picture-based formats. Like all procedures, text-based procedures briefly describe the equipment or machines they apply to, followed by a list of steps that must be followed to properly lock out the equipment. Often, a set of numbered steps is presented for the employee to use. Other times, a company may choose to have a checklist of possible sources, noting those present in each piece of equipment.
Authorized users who are locating the disconnects often find text-based procedures difficult and time-consuming. To avoid confusion, it is best to use text-based procedures only if all sources are labeled and numbered so employees locking out the equipment can confirm the proper valves are closed.
Procedures Including Line Drawings
As software advanced in the mid to late 90s, line drawings became very popular as the next best upgrade over text-based procedures. They were faster, and they also gave the authorized employee a much better sense of confidence that they were following the instructions correctly. Unfortunately, many lockout/tagout procedures that use line drawings are still in place because of a corporate policy requirement or rigid proprietary software that only supports this design.
While line drawings provide better clarity to the authorized employee as to where the lockout points are, there are still many areas for ambiguity when trying to translate a line drawing into a real-world setting. Line drawings typically work by providing a bird’s-eye view or possibly a 3D view of the equipment to serve as a map to help locate the isolation points. In addition, by using standard piping and instrument symbols, employees can determine the type of isolation point for each source, aiding in selecting the correct lockout devices.
While the added visual is helpful, those without knowledge of piping diagrams will find the procedure confusing. It also requires employers to have and/or create updated line drawings for each piece of equipment that requires a lockout/tagout procedure, which is often a difficult task.
Graphical Lockout/Tagout Procedures
The current gold standard for lockout/tagout procedure formats is undoubtedly the picture-based graphical approach. By including high-quality pictures of the equipment, isolation points, control points, and specific shutdown components, authorized employees can quickly and clearly understand how to lock out the equipment. Additionally, including graphical tags with this solution helps bring the program together to help authorized users process the lockout/tagout procedure steps more quickly, with less likelihood of them isolating the wrong source.
There is an absolute advantage to having graphical lockout procedures available for daily use and the inherent efficiency advantage to more easily conducting annual auditing tasks.
Fully Electronic Lockout/Tagout Procedures
With the advancement of technology, the ability to maintain only electronic copies of procedures has become a real possibility for many companies. Digital versions may be text-based, line drawings, or graphical procedures, and the advantages are many. To fully implement such a program, companies must have access to tablets readily available for authorized employee use and solutions available for contractors while on site. Physical three-ring binders can always serve as an ultimate backup, and procedures can still be mounted on the equipment to help enhance the program. For any companies who still print the procedures to institute lockouts, the usage of tablets will have an immediate cost saving by cutting down on paper waste and confirming the procedures are always up to date.
By keeping only electronic digital lockout tagout procedures, document control becomes much easier. In addition, record-keeping for procedure usage also improves if good software and documentation are used.
Custom Format and Graphical-Line Drawing Hybrid
When the situation warrants it, another method for creating lockout/tagout procedures is to add pictures of the lockout steps and further enhance the message with an overview map showing the isolation points in the line drawing. This method is sometimes used for large pieces of equipment or system-based lockout/tagout procedures where the complexity of the process warrants the extra investment in customized formats such as this.
Typically, the line diagram will be located at the top of the first page of the procedures. The corresponding pictures will be placed around the diagram, with arrows indicating which sections of the pictures are showing. For example, shutdown steps can be located below.
Although this method leaves the least amount of room for error when using the procedure, it is also the most time-consuming procedure to create and maintain, as the equipment changes will change over time.
Hidden Dangers
Lesser-known Risks to Be Aware Of
It is sometimes difficult to look at a machine and determine all energy sources it possesses. Therefore lockout/tagout procedures must contain more information than just the energy sources that can be locked. The procedures must also inform the employee of the energy sources that are non-lockable. Some common non-lockable energy sources include:
- – Potential energy – magnetic
- – Potential energy – capacitance
- – Potential energy – gravity
- – Potential energy – spring
- – Hydraulic energy
- – Thermal energy
- – Kinetic energy
These energy sources can easily be overlooked, but all of them pose a hazard to employees that must be addressed.
Some of these non-lockable sources, and the methods to control them, are more obvious than others. Simply waiting a few extra minutes before performing a lockout can render many of the non-lockable energies inert. Energies such as capacitance, kinetic and thermal energy need time to dissipate. Others like gravity, spring, and hydraulic energy, take more initiative.
The lockout technicians must take it upon themselves to lower all suspended parts, reduce or eliminate potential energy in the springs, or bleed the pressure from the hydraulic lines to create a safe lockout environment. Keep in mind that some energy, such as magnetic energy, is always going to be present, and you’ll need to choose the safest way to perform the work. If so, it is important to notify the authorized and affected employees, so that any extra personal protective equipment can be acquired. Magnetic energy has the potential to create pinch points, or to launch ferrous tools; and it should be acknowledged before a lockout begins.
The Future of Lockout/ Tagout Procedures
Lockout/ tagout procedures are one of the most critical aspects of an organization’s ability to comply with safety regulations. A good procedure safeguards employee compliance and helps ensure safe and efficient operations for all company employees.
As safety regulations continue to evolve, businesses must adapt and keep up with their standard practices. While many companies still rely on traditional lockout/ tagout procedures that have been used for decades, future organizations will likely start moving towards cloud-based programs or software that allows more efficient reporting and records management. This new trend reflects a growing need for businesses to collect more data on their processes to identify potential problem areas better and come up with solutions in real-time.