Key reasons why a backward-compatible system is essential for a future-oriented manufacturing facility
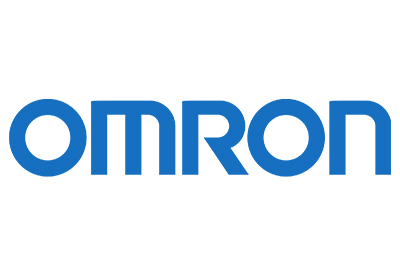
July 31, 2019
Omron are committed to developing advanced technologies that maximize our customers’ potential for innovation. They invest 7% annually in research and development so that they can design and build products in-house that work together at maximum efficiency.
One of their key product development maxims is the commitment to ensuring backward compatibility so that their customers can enjoy long-term operational stability. The interoperability of their technologies protects investments in resources such as hardware, engineering, and design time.
The challenges surrounding firmware and software compatibility
Besides the hardware, there are two key components that must work together in a manufacturing system: the firmware and the software. Firmware is the code responsible for providing low-level control of a particular piece of hardware, while software is responsible for programs that run the overarching applications.
One significant problem that manufacturers face when using equipment from certain automation solution providers is that each firmware revision for a given device (PLC, drive, servo, etc.) is only compatible with one revision of the programming software and vice versa. If updates are required, it’s a challenge to keep everything working together properly.
Sysmac Studio’s backward compatibility keeps downtime to a minimum
Omron designs its controllers and its Sysmac Studio programming environment to make these headaches go away. By ensuring that controllers and other hardware components work seamlessly with older firmware versions bearing the same part number, the Sysmac platform simplifies setup and reduces the length of downtime occurrences.
Programs written with older versions of Sysmac software can be opened and edited with newer revisions, so it’s only necessary to keep the latest version installed. This makes it easy to access machines that need troubleshooting or program changes and eliminates the need to manage lists of revisions for machines, lines or the entire plant.
The ideal solution for scalable applications that require equipment mixing and matching
In the Sysmac software, firmware is a drop-down selection in the software. This makes it easy to add new components to a system. For example, if a user has a machine controlled by a three-year-old Sysmac NX102 Machine Automation Controller and would like to add a machine safety system using Omron’s latest NX-SL5 Safety Controller, the user simply needs to open the existing NX102 project in the latest version of Sysmac Studio and add the NX-SL5.