Key Component Considerations for Improved Machine Safety through Automation and Control
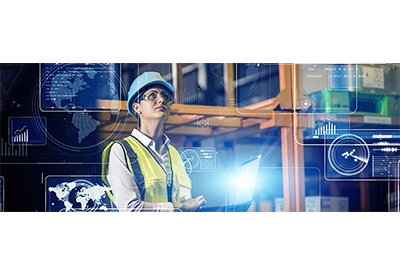
January 18, 2021
As factory automation evolves with Industry 4.0, advanced technology continues to introduce more accurate and innovative features, many of which are used to protect personnel and equipment.
In competitive industrial operations, quality, throughput, uptime, and other production attributes are key. Operations must not only be precise, but also safe. Safety, however, relies on new innovations in sensors, controllers, relays, and other controls, to prevent mishaps that can potentially be life threatening. Manufacturers and distributors of automation and control technologies are responding with accurate controls to ensure unprecedented levels of safety.
To better understand how such components add safety, we take a brief look inside four basic components – sensors, relays, modular safety controllers, and servo motor controllers – to understand how certain components aid automation and create safer conditions.
Sensors
Sensors detect a condition according to a set point and signal action and are quite useful in automation and control to protect personnel and equipment.
“The requirement for safety sensors to protect operators has evolved in tandem with technological progress. Safety light curtains, safety laser scanners and related technologies are being developed around the principle that customers need reliable and durable products,” says Kenny Heidel, P.E., Product Manager, Safety at Omron Automation Americas in Hoffman Estates, IL.
“Critical machine uptime has always been a focus of manufacturers and the cause of unplanned downtime can be something as simple as light curtain misalignment. For this reason, many manufacturers are transitioning to safety-related sensing technologies that provide enhanced diagnostic data and can sound an alarm when they detect a change in the monitored area. ”
Kenny adds that today’s engineers must stay abreast of new products that have feature sets designed to alert them when a potential problem requires troubleshooting before it might result in unexpected downtime. These features include, but aren’t limited to, IO-Link communication of real-time data, improved diagnostics based on what vendors have historically experienced, and visual indicators that show more than a simple on/off signal.
“Engineers are opting for safety sensors that align with their machine needs instead of simply choosing what appears to be the least expensive product available,” says Heidel. “They’re realizing that it’s wise to value machine strategy over cost, and this evolution is enabling them to focus on other product areas to find more ways to ensure uptime.”
Relays
The risk to man and machine is also mitigated with relays that prevent mishap. More specifically, in automation and control, relays protect against potential damage caused by a surge in amperage. Relays help to automatically control the on and off switching, thus controlling power admitted to circuitry.
Relays may be electromechanical, or nowadays, solid state. A solid-state relay uses electronic switching to admit power to the load circuitry. It may be used in either AC or DC circuitry and is used in conjunction with a coupling mechanism to activate switching without mechanical action. Since solid state relays have no moving parts, they are quieter and tend to last longer.
“Today’s safety relays offer an advanced set of features that are focused on helping to reduce installation time and save mounting space,” says Pam Horbacovsky Klancewicz, a product manager at OMRON Industrial Automation. “For example, the G9SE series has ultra-slim design that can help to reduce 45-65% of the mounting space required, and screwless terminals can help to reduce installation time by at least 50%.”
She adds that LED status indicators on safety relays offer much more information today than five years ago. For example, a set of LEDs indicate what type of error has occurred, such as a short circuit or a broken wire, which helps to minimize downtime by making it easier to identify the cause of unplanned stops on machinery.
Modular Safety Controllers
Incorporating multiple safety relays in different channels of industrial automation can be costly. Given that designs with multiple relays is more challenging than having one central module, modular safety controllers may be used in lieu of relays. A safety controller, with the function of several relays incorporated within, makes it easier on the design and its operation. In addition, controllers may work in tandem with other safety controllers and support multiple inputs and outputs.
“Flexibility is one of the most common requirements in manufacturing systems, and from the functional safety perspective, it implies that there is a need to move from a safety-by-wire solution to a safety networks solution, which is only achievable by implementing an ‘integrated safety’ approach,” says Pam. “This strategy has two major components: the implementation of one integrated development environment (IDE) and the use of safety networks.”
According to Horbacovsky Klancewicz, having a unique IDE makes it easier to develop entire industrial automation solutions – including standard PLCs, safety, motion, and vision – thus making it possible to simplify machine design and commissioning. The major advantage of having an IDE, like Sysmac Studio is the seamless sharing of information between systems, while function blocks and built-in tools simplify programming and commissioning, making it easier to monitor the entire system from one single program instead of combining a dedicated platform for each piece of a machine.
“The second element is the reduction of wires as much as possible, which leads to the development of modular safety systems to make it easier to change the process according to the product or model running,” she further explains.
“For example, muting a portion of the process when running product A, and enabling one robotic cell when running product B. In the past, this type of modification meant that an automation engineer, with a deep understanding of functional safety, needed to reprogram the safety logic of the machine and re-wire each safety device. Thanks to the latest innovations in safety controllers, for example the NX-SL5, this can be easily solved when using safety networks, like CIP Safety or Functional Safety over EtherCAT (FSoE), which makes it easier to add or remove stations to a system by simply plugging or unplugging a cable combined with automatic detection to adapt the safety system to the current configuration.”
Servo Motor Controllers
Servo controllers are another category of control component used in conjunction with drive technology – most commonly motors. The servo controller works in tandem with a small motor, a controller of sorts, and typically a small feedback device. The servo system adjusts according to automation parameters such as position, speed, torque, or other set values or inputs in order to accurately control the machine operation.
For example, the Omron Automation R88M-K75030H-S2 uses high positioning accuracy and features a 20-bit high-resolution incremental encoder.
Its function as a servomechanism pairs with an encoder to provide positioning and speed feedback. As a safety device, it utilizes error-correction routine to correct motion where needed to prevent any damage from inordinate motion or action. In some instances, a speed-limiting function can be instrumental in providing motion safety in high impact applications such as crushing, which involves strong and forceful impacts. Any anomaly in operation may cause machine shut down and disrupt the flow of operation. A control that manages shutdown, and subsequently downtime, is beneficial.
“In machines where an intervention such as removing crushed products makes the entire line to stop, downtime can expeditiously increase with just one single event like this per hour, as system restarts can become time-consuming depending on the process and machinery involved,” explains Horbacovsky Klancewicz. “With motion safety function, like the safely limited speed (SLS) function, it is possible to keep the production line running at a limited speed when a guard is open to remove a damaged product.”
She also points out that by avoiding a complete stop, downtime becomes manageable and the system can restart smoothly from speed limit to normal speed when all safety conditions are met again.
“Other ways on how servo drives can add flexibility to the factory floor are linked to the use of one cable to power, encode, and break, for quick installation and troubleshooting,” she adds. “And the option to have integrated programming and testing functions helps to reduce the commissioning efforts and speed up implementations.”
Safety through Automation and Control
Safety is paramount in all industrial applications. With the continuous arrival of newer and more innovative automated equipment, the pursuit of a safe working environment is crucial. Fortunately, there are many different engineered components that may be integrated into an automation landscape to protect man and machine. While there are no substitutes for militant safety training and a persistent safety culture, components and hardware are helpful to achieve safety goals and protect people and assets.