Jog Mode in the S6 and F6
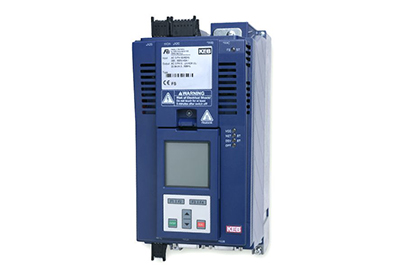
July 9, 2020
With the release of the version 2.6 firmware, the Jog Mode functionality is now available for all S6 and F6 drives. This post will provide an introduction of what is available with the function and how its utilization can provide application benefits.
How it Works
In the Jog Mode, a user can program the drive to run at two, bidirectional, speed set points that are independent of those defined for normal operation. This is achieved by using up to five of the drive’s digital inputs and, if desired, one input can be used to command multiple portions of the Jog Mode setup.
At a minimum, the user must provide an input to activate the Jog Mode and to select a direction. The user can then opt to add additional inputs to select the opposite direction, select a second speed, or to add a movement limit. The function also uses acceleration and deceleration rates that are independent from the typical operation. Finally, the user can opt to use hardware or software limit switches whose uses are again independent of the standard operation.
When entering the Jog Mode, all error statuses are cleared once. Additionally, fieldbus watchdog errors are ignored while the function is active. This allows the drive to run regardless of the status of the fieldbus communication. When leaving the Jog Mode, the KEB drive’s state machine is shut down and any commands must be resent. This ensures the motor cannot run unintentionally when leaving the Jog Mode. With this relatively basic setup, the Jog Mode ensures the motor is always able to spin.
Application Benefits
The main benefit of the Jog Mode is that it allows the drive to run at any time, using only digital inputs. For this reason it is sometimes also referred to as a “Manual Mode”. Under that umbrella, there are two particular examples that highlight the usefulness of the function.
The first is in its ability to override fieldbus errors and ignore the loss of communication to the PLC. While the world of automation is increasingly reliant on fieldbus communication, these systems sometimes do still fail. Network cables can fail or can be cut and crushed. When this occurs, the Jog Mode allows the user to run the motor in emergency situations.
Another useful example of the function is its use for the startup and commissioning of systems. In material handling, lift, or theater applications the Jog Mode can be used to slowly run the motor to find and store stopping positions or end limits. With its relative simplicity and independence from the rest of the system, the Jog Mode ensures the motor can run simply and easily at any time.