How to Prevent MCC Corrosion with Insulated Bus Technology
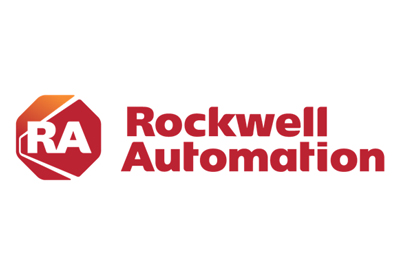
September 14, 2020
By Andrew Schaeffler, Sr. Product Specialist, Intelligent Packaged Power and IntelliCENTER Technology, Rockwell Automation
Many industries around the world face challenges with corrosive environments, whether it is inside their facilities with air pollutants such as sulfur dioxide, or outdoors with corrosive factors such as water and salt fog. Corrosion is the single largest cause of the breakdown of machinery, structures, supports, and motor control equipment in a plant.
Such demanding environments require that extra thought be given to equipment longevity and arc flash avoidance. When it comes to motor control centers, the power bus design can help address both. The horizontal bus on CENTERLINE Motor Control Centers (MCCs) can be insulated with a factory-installed polypropylene flame-retardant wrap that helps prevent arc propagation and prevents MCC corrosion by creating a resistant seal around the busbar.
The oil and gas industry, for example, can subject MCCs to harsh and corrosive environments. From harsh environments in the refineries to salt fog that is often experienced on offshore drilling platforms, the polypropylene wrap used in CENTERLINE 2100 MCCs with insulated bus provides resistance to the severe environments. The increased resistance to corrosion of the insulated busbar can lead to increased longevity and performance.
Arc Flash Reduction
A sound structural design and a well-supported, isolated bus system are critical for an MCC to withstand the effects of an arc flash event. The two side sheets on every MCC section and a robust bus support design significantly contribute to the ability of the equipment to contain and redirect the arc flash energy.
An arc flash event has the potential of expelling large amounts of energy that can have deadly consequences. The energy in the form of the arc flash can reach temperatures of 35,000 °F, which is hot enough to vaporize copper and aluminum cables and busbars. The explosion also creates high pressure and sound waves. These events can be triggered by equipment that could be underrated for the available fault current, by accidental contact with an energized conductor, or corroded equipment such as a busbar in an MCC. Insulating the busbar in an MCC and helping prevent arc propagation or accidental contact is important for personnel and equipment safety.
Equipment Longevity
The polypropylene wrap that surrounds and insulates the busbar also helps protect and extend the life of the MCC. The wrap protects the busbar from air pollutants such as:
- – Sulfur dioxide
- – Trace materials like oils and lubrications
- – Dust found in sawmills and other food processing facilities
- – Moisture and other caustic materials prevalent in a manufacturing facility
While you can’t always control your operating environment, you can select products that are designed to withstand its challenges.