How smart manufacturing solutions address current megatrends in the packaging industry
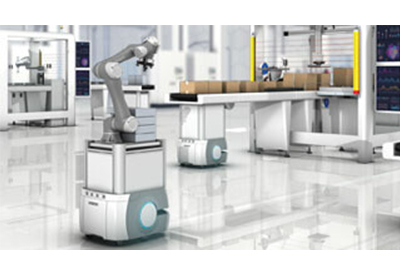
February 18, 2020
Flexibility is the ultimate strategy for success in today’s challenging market for food and beverage packaging. Companies are striving to produce increasingly large varieties of products – including various sizes and combinations – while also being able to turn on a dime in response to any change in consumer demand.
Although this level of flexibility isn’t easy to implement, certain smart solutions can bring it within reach much more quickly. The latest automation technologies range from turnkey applications to comprehensive, end-to-end systems. Let’s take a look at several key solutions that can put packaging companies on the path to success.
Technologies that speed up package sortation and placement
Robotics – whether fixed, mobile or collaborative – increase the speed, functionality and precision of operations. They perform a wide variety of repetitive tasks and can handle product changeovers with ease – key requirements of any packaging line that’s intended for high-mix, low-volume production.
Omron’s package sortation and placement solutions speed up automation processes, ensure precision in operations, and boost the efficiency of repetitive tasks. Designed with flexibility in mind, these systems seamlessly handle a variety of packaging sizes and dramatically reduce the amount of downtime associated with changeovers.
Automated line changeover solutions that dramatically increase production efficiency
In a typical changeover, the system must be brought to a standstill so that machine settings can be adjusted. In addition, bringing a restarted line up to speed too quickly can result in damaged and wasted product as well as lost time to tweak the settings even further. As product proliferation becomes more widespread, the need to reduce changeover time is growing.
Omron’s automated changeover solutions reduce the risk of jams and incorrect adjustments and keep post-changeover startup waste to a minimum. By increasing the availability and operating time of machinery, shortening the time before payback and eliminating supply chain delays, these solutions enhance packagers’ productivity and competitiveness.
Data-driven solutions that further optimize production
One of the main requirements of operating a flexible plant is leveraging real-time data from the production line and turning it into key performance indicators. Intelligent use of this data significantly improves equipment longevity through improved predictive maintenance and makes it easier to spot and improve upon quality issues.
Omron’s technologies for collecting and analyzing data are designed to help packaging companies identify operational strengths and weaknesses by providing visibility into complex production processes. Traceability and other data-driven strategies also help resolve quality, safety and compliance issues.