How Predictive Maintenance Technology is Improving Machine Monitoring
March 17, 2025
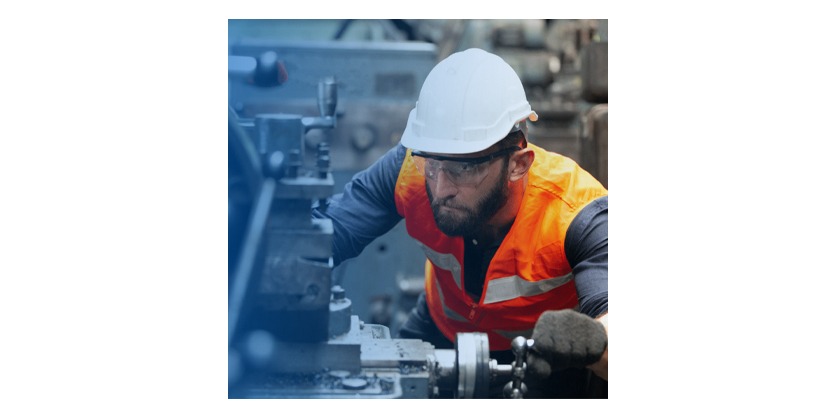
Learn how to leverage solution providers to automate real-time data collection, detect issues early, and optimize maintenance activities.
Introduction to Predictive Maintenance
Predictive maintenance is changing the way industries manage their equipment. Unlike traditional maintenance methods, which rely on fixed schedules, predictive maintenance uses real-time monitoring to detect potential issues early. This proactive approach reduces the likelihood of unexpected downtime and ensures that maintenance activities are performed only when necessary, optimizing resource allocation and reducing costs.
Key Advantages of Predictive Maintenance
One of the key advantages of predictive maintenance is the consistency and reliability of its data-driven approach. Real-time data is available for everyone to read and act upon, minimizing the variability that can arise from individual expertise. This ensures that maintenance decisions are based on accurate and up-to-date information, leading to more consistent and reliable operations. This not only frees up skilled labor for more critical tasks but also reduces overall maintenance costs. By automating the monitoring process, factories can achieve more efficient operations, ultimately improving their bottom line.
Overcoming Challenges in Predictive Maintenance
While the benefits of predictive maintenance are clear, implementing this technology in factories with legacy equipment can present several challenges. One of the primary hurdles is the high initial investment required for predictive maintenance devices and their integration into existing networks. Legacy equipment often lacks modern communication ports, making integration more complex. Additionally, there may be a lack of technical expertise to understand and act on the data collected.
The Role of Solution Providers
These challenges can be effectively addressed by partnering with experienced automation solution providers, like Omron. They can guide factories in selecting the most appropriate monitoring devices and ensuring that the initial investment is justified. They help identify the root causes of equipment issues and recommend solutions that are tailored to the specific needs of the factory.
Simplifying data integration is another critical aspect. Solution providers can suggest devices that are easy to configure and integrate into the existing network, and they can use built-in algorithms to filter and process data, making it more accessible and actionable. Furthermore, they can offer comprehensive training programs to bridge skill gaps and ensure that the data is presented in a way that is easy to understand.
Real-World Success Story
A real-world example of the benefits of predictive maintenance is the case of a global baked goods manufacturer. This company faced significant challenges with manual processes, including unstable data tracking, increased downtime, and safety risks. By upgrading to an automated system with EtherNet/IP for data logging, they improved data tracking, synchronized processes, and eradicated errors. This set the stage for implementing predictive maintenance, which significantly improved production efficiency, safety, and product availability.
More Information
Reduce unplanned downtime with 24/7 predictive maintenance
Related Story
Omron’s K6PM Thermal Condition Monitor: Predictive Maintenance Reduces Downtime
Effective and exhaustive temperature monitoring has traditionally been performed by skilled workers who are adept with using special thermal monitoring equipment to identify potential concerns. These inspections, however, are becoming increasingly complicated because of the ever-increasing number of devices in a panel that are needed to adhere to compliance standards. Simultaneously, the quality and quantity of maintenance workers is receding, making it challenging to provide real-time analysis of thermal conditions in a panel and develop an accurate snapshot of the system.