How Omron’s Motion and Control Helped Liquibox Reduce Material Waste and Stay Flexible
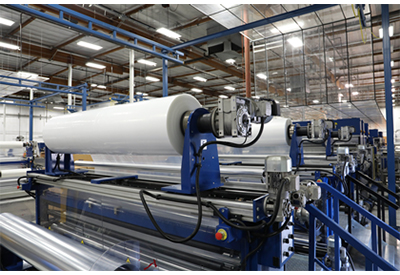
June 2, 2020
For flexible packaging pioneer Liquibox, sustainability has always been a priotiry. The company has more than 50 years of experience supplying pouches and bag-in-box solutions to food and beverage companies, and its liquid packaging withstands hard shipping conditions, dispenses perfectly into any machine. and maintains a small environmental footprint.
In search of a new way to make both their products and their processes more sustainable, Liquibox teamed up with Omron to devise a solution.
Reducing material waste by improving accuracy
Omron’s first task was to enhance the accuracy of the system that pulls film along the length of the company’s bag-making machines, which are flexible enough to handle a range of film types and material sizes as well as fitments. We used our G5 servos to achieve the required specification while keeping tension constant and avoiding over-pull or under-pull.
Controlling the temperature to support sustainability
Liquibox uses a variety of films with new resin technologies that make them stronger and thinner than other options. These films require better temperature control, as each type may have a different gauge and melting point. Omron’s E5C temperature controllers keep the sealing bar temperature stable while accommodating variances from film changeovers.
Overall, the new Omron technologies helped Liquibox produce 100% of its bags within specification and significantly cut down on wasted material. The company’s machines now deliver 133% higher pouch output thanks to the speed of the EtherCAT network and the Omron platform’s fast program scan time.