Give Your Machines the Correct Prerequisites by Easy-Laser
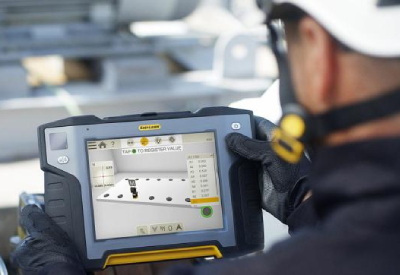
May 16, 2022
Within the industry, maintenance of machinery and plant is routine work. But not everyone is aware of how to minimize future costs and risks for downtime already from the start. Although it is so apparent!
Increased sustainability and reduced energy consumption
Everywhere in our society, machines are used for producing varying items, process materials, pump fluids, etc. These machines must be given the correct prerequisites to do the job for which they were designed. The importance of this increases with the naturally growing demands for sustainability and productivity which we face in our society. We are constantly reminded of the need for more energy-efficient solutions for the sake of our environment, right? This is where precision alignment with laser measurement systems comes in.
Flatness and level are fundamental
For a rotating machine to work as intended, it is fundamental that it is installed on a flat and level surface. This is to ensure proper lubrication of bearings, and that stresses on machine components equals that for which was calculated. With laser alignment systems from Easy-Laser you ensure a flat and level foundation, and that all base plates are plane-parallel in order not to force the machine into position when bolted in place.
Did you, for example, know that the recommended tolerance for machine foundation flatness is 0.2–0.4 mm/m, and that all feet plates should be coplanar within 0.05 mm? The next step is to set up the machines (for example a pump and motor) perfectly in line with each other, i.e., shaft alignment. And no, a straight edge and eyesight are not sufficient for the machines of today, as you understand!
Are you aware of dynamic forces?
Another thing often missed during machine installation are the dynamic forces generated when the machine is operational. They can be caused by pumped fluids, resulting in unwanted forces in pipe connections, or material expansion due to rising temperatures. This misplaces shafts, which in turn generate larger forces in bearings and sealings than the machine was designed for. An example from reality is a company that for many years never got one of their machines to work. Several so-called experts had been there and “proven” what was wrong, but the problems did not go away. With a quick dynamic movement check, we could show that the machine moved 1.3 mm horizontally after being started, which of course was devastating, and totally unexpected. With the right actions, the machine now finally runs as it should.
A laser alignment system quickly pays for itself
The great benefits of laser alignment systems are:
- •Programs guide you step-by-step, which makes for ease-of-use.
- •Versatile and quick to mount on most machine types.
- •Highest reliability and precision (down to 0.001 mm).
Another great advantage with laser alignment systems is that you can document the work in a measurement report for you and the client, which shows that what has been done is within the tolerances required by the machine manufacturer.
In the longer term, this traceability is very important, as if constant problems arise in production, you can go back and see that the conditions were correct from the start. Or not. Then you know where to start problem-solving!
Even better is of course to do things right from the beginning – to give the machines the correct prerequisites for problem-free operation and optimum service life. The investment cost of a laser system is only a fraction of the costs for unplanned downtime and unnecessary high electrical bills. Increased competitiveness comes for free.
If you want to learn more about Easy-Laser’s industrial alignment solutions, please contact them by clicking here