Get a Countdown to Downtime With Drive-Based Predictive Maintenance
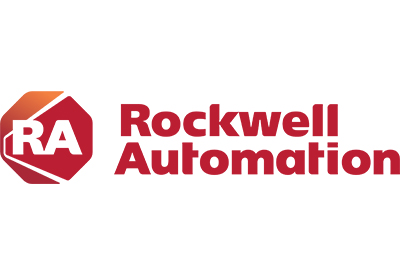
June 27, 2019
Do you have a countdown for when your critical assets are expected to fail? What could you do with one?
What if, rather than scrambling to resolve asset failures when they happen out of the blue, you could see them coming and make plans to address them? You would probably herald in greater peace of mind, with less agonizing over surprise failures and the unplanned downtime that comes with them. You would also most likely realize financial savings by reducing your spending on maintenance and replacement parts.
Now, a “countdown to failure” capability for your production assets isn’t just wishful thinking. It’s something you can deploy using new AC drives that have advanced, built-in predictive maintenance.
Agnostic + Adaptive = Accurate
Predictive maintenance can offer different levels of accuracy.
For example, some products are configured to make certain assumptions, like the operating conditions in which they’ll be used. However, if a product is configured for the hottest possible conditions but used in a cooled facility, then it will likely alert users of servicing or replacement needs sooner than they’re actually required. And while that’s a better maintenance approach than waiting for assets to fail, it doesn’t allow you to get the most performance or value from your capital investments.
New AC drives with predictive maintenance are configured with agnostic algorithms. This means the drive will make no assumptions about the application or operating conditions in which you deploy it.
Instead, the drive spends its first 30 days of operation learning its applications stresses. It uses built-in sensors to monitor stressors like temperature, voltage, current and speed. It then uses models to convert those stressors into rate-of-life consumption data for critical components like fans and capacitors.
After 30 days, the drive will have an established understanding of your application based on actual – not assumed – stressor parameters. Even after that, the product will continue relearning and updating its use-case model at least once per hour.
The AC drives with advanced predictive maintenance are also adaptive. So, if a new shift is added to production or if a drive is swapped from one machine to another, the drive will relearn how it’s being used and adapt its predictions for when its components will reach their end of life.
These agnostic and adaptive learning capabilities can help you understand the true remaining life of the drive’s critical components. This allows you to run them to their full potential and only replace them or their critical components when necessary.
Better Insights to Optimize Maintenance
AC drives with advanced predictive maintenance can help you make smarter, more precise maintenance decisions.
Operators and technicians can track end-of-life data down to the hour for each critical component to better plan maintenance activities. And they can be notified by an alarm when critical components reach a certain percentage of their predicted remaining operating life. Then, they can create a maintenance plan for the exact day or shift when they will replace the component.
The drives can also help you learn from and optimize their performance across your operations.
For example, you may notice that AC drives running in an air-conditioned facility have a longer rate of life than those in an uncooled facility. Specifically, the bearings in the drive’s heat-sink fan may be wearing out faster in the hotter facility. You may then determine that extending the life of the drive and reducing your maintenance makes enough financial and operational sense to add air conditioning in facilities that lack it.
Built-in Predictive Maintenance
One of the most appealing aspects of AC drives with predictive maintenance is they offer the capability as an inherent product feature. They require no add-on or extra charge to access the predictive insights.
Remaining life component data can be read directly on the drive. You do have the option, however, of scaling up the data into your plantwide visualization software or to the cloud. This allows you to build a predictive-maintenance strategy that corresponds with the size and needs of your operations.
For more information, visit HERE.