From Beer to Hand Sanitizer: Adapting Manufacturing for COVID-19
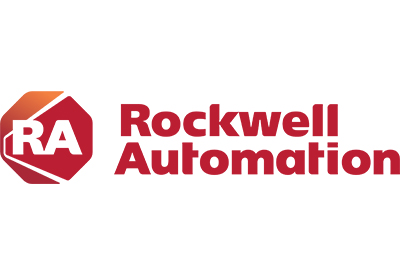
May 4, 2020
By Michaela Kaufmann, Product Manager, iTRAK, Rockwell Automation
The world stands still as COVID-19 continues to turn it upside down. No more social contact. No more ‘business as usual.’ In fact, no more ‘normal’ for many. Now, we stay home to save lives.
But there are some brave souls who cannot stop like doctors, nurses, and pharmacists. And, hidden in the background we find manufacturers, machine builders and their suppliers. These are the people responsible for producing food, life-saving medicines, masks and wipes.
It is unquestionable that in times like these we must move together to ensure production of the products that are so urgently needed. And not only that, but we must do it as quickly as possible to avoid interrupting mass production and serve the greater good.
Societally, we have now experienced a lack of ventilator masks, cleaning and disinfecting products, toilet paper, and sadly, medical devices. But, how do we quickly change from beer or spirits to hand sanitizer? How do we adapt newly developed medical device designs for our current machine lines? How do we answer the difficult question of which medication production to prioritize? Which machine line to change? Obviously, there is high demand to manufacture products to combat the current pandemic, but at the same time other life-saving medication demands do not stop. Therefore, how do we adapt to the increase in demand for certain products, while overcoming challenges, like not having the physical infrastructure to allow production growth?
Independent Cart Technologies serve several production demands, all in one
Independent Cart Technologies (ICT) allow changeovers for different products and formats with the push of a button, providing the ability to manufacture a variety of products on a single line.
Individual medical packages? No problem.
Single and large packs? You’ve got it.
Switch from diapers to masks? Right away.
Mass-customized production is enabled based on several driving demands at the same time.
But, it goes beyond unlimited flexibility. Implementing pitchless technology increases your throughput and uptime while eliminating chains, belts and other traditional mechanics that limit speed. The mix of continuous and intermittent motion, as well as easy synchronization with any other external axis, like robots, improves operational efficiency and contributes to higher productivity. With this, the common bottleneck of in-feed complexity belongs to the past. Floor space can be reduced because machines are now designed to be scalable and modular. It’s now easier to re-deploy existing machines for new products and integrate multiple machine functions.
Analytics and smart track and trace of individual products throughout the entire process help ensure quality, improve production process and reduced energy consumption while always being aware of your customized production—even remotely.
Innovation never stops
ICT combined with analytics, simulation and other leading-edge technologies, such as wireless power transfer and wireless communication, bring manufacturing to the next level. Analytics provide full transparency into how machines are running, maximizing uptime. Simulation can be used to create Digital Twins and access virtual training and support, which helps decrease time to market. This is especially important in our current uncertain times, requiring manufacturers to pivot quickly.
Unimaginable speeds can be achieved for light products because communication and power at the mover make it possible to affix products that would have flown off the conveyors of older machines.
These are just a few examples demonstrating that creativity and innovation never stop.
So, don’t decide which demand is most important. Let’s lay the foundation for the future while meeting the needs of the world in the present. Let us help you combine and serve every need.