Four Ways New DCS Technology Makes Life Simpler
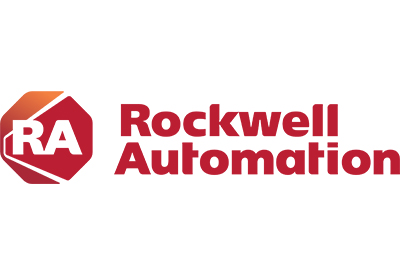
June 16, 2020
By Blair Wilson, PlantPAx Marketing Manager, Rockwell Automation
More frequent process changes. New technology. Larger datasets. Greater traceability and compliance requirements. Tighter budgets.
Sound familiar?
From oil refineries to food and beverage plants, process engineers are being asked to manage increasingly complex systems – and to do more with less. The good news is the latest distributed control system (DCS) platforms have kept pace with technological developments. And more DCS users are now considering upgrading and modernizing their systems for optimal performance.
But just how will a DCS modernization help manage system complexity and improve productivity? If you’re like many process engineers I meet, that’s the question you’re asking.
Our latest release of The Modern DCS addresses key challenges throughout the lifecycle of your system – and makes life simpler in four critical ways.
1. Purpose-built, robust controllers minimize complexity.
By their nature, processing plants are multifaceted and continuously changing. As applications expand and become more sophisticated, many older controllers and I/O platforms simply cannot keep up. For many plants, adding controllers to the existing automation infrastructure to meet new demands has been the only practical response.
But as you know, introducing more and sometimes disparate systems makes an inherently complex DCS even more complex – and more costly to integrate and maintain.
Now new process controller types provide a better option. Significant gains in processing power and capacity mean you can manage more strategies with fewer controllers – and reduce architecture complexity and related lifecycle costs.
The latest release also enables “report-by-exception,” which significantly reduces architecture stress caused by alarm and event polling. And for many systems, less polling means fewer data servers as well.
2. Embedded process objects keep applications – and user experience – consistent.
Everyone has their own ideas about how a system should function. And while we all appreciate the skills of a good developer, one person’s undocumented “tweaks” become another’s significant challenge when maintaining or updating a system.
Additionally, once a vendor-provided object library is modified, you can no longer rely on the vendor to maintain, migrate and document it. That becomes the job of your staff or system integrator, increasing costs and risks over the lifecycle of the system.
As part of a DCS modernization, new controller types feature process objects embedded in the firmware to drive more design consistency. Embedded process objects support a modern approach to system development by “locking down” core controller functionality, which allows developers to focus on configuration for higher-level applications.
Because core functionality aligns with industry standards and cannot be edited, embedded objects help maintain system integrity – and speed replication plant to plant. Embedded objects also automatically migrate when new firmware revisions become available to make future upgrades simpler.
3. Automatic diagnostics save time.
Your existing DCS tag database includes diagnostic information regarding your controller, I/O and field devices. Making that information accessible to operators may require significant development work on the back end.
In fact, identifying diagnostic tags in the control system and then configuring links to those tags in the HMI platform could account for up to 30% of the coding required to design and maintain a system.
DCS modernization streamlines this process. Using the expanded capacity of the new process controller, preconfigured alarms automatically deploy directly to the HMI with a single click. This capability saves significant time during initial development – and throughout the life of your system as process requirements evolve.
4. Alignment with latest standards helps minimize cybersecurity risk.
To take advantage of the latest IIoT technologies, your DCS must integrate with enterprise-level systems. But connecting more information across your enterprise could inadvertently expose your process operations to risk.
A Modern DCS recognizes the need to both take advantage of advanced analytics and other digital technologies – and help protect your critical data. The latest release allows you to migrate forward and implement a system and process controllers aligned with international standard IEC 62443 – and global cybersecurity best practices based on defense-in-depth.
As the term implies, a defense-in-depth strategy recognizes that any one point of protection will likely be defeated. Cybersecurity systems based on this strategy establish multiple layers of protection through a combination of physical, electronic and procedural safeguards.