How Effective Communication Reduces Plant Hazards
November 6, 2023
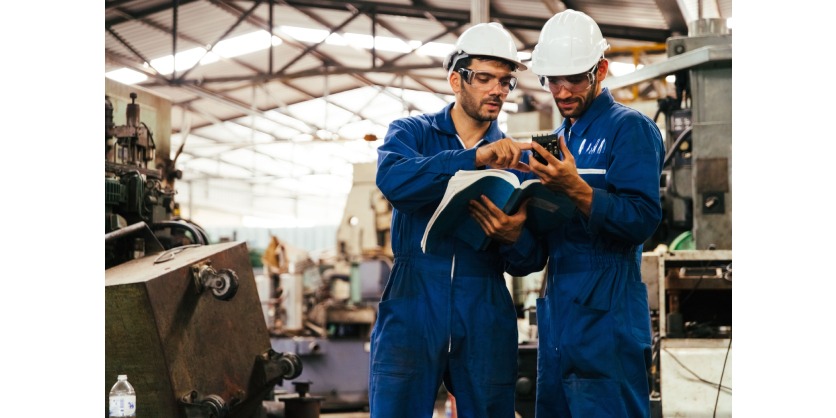
By Rick Farrell, President, PlantTours
In plant operations, the margin for error is notoriously slim. The smallest oversight, a single misinterpreted instruction, or an unnoticed alert can be the difference between smooth operations and catastrophic failures. While advanced technologies and protocols play an undeniable part in ensuring safety, the bedrock upon which all these measures stand is clear and effective communication.
Communication isn’t merely about transmitting information; it’s about ensuring understanding, fostering trust, and driving home the gravity of protocols. Done right, it can be as potent as the most advanced safety systems. Read on as we unravel the pivotal role of communication in reducing plant hazards.
Common Electrical-Related Plant Hazards
Plant operations, particularly electrical work, are riddled with hazards that demand stringent safety protocols and awareness. Some common plant hazards include:
Arc Flashes: A Silent Peril
An arc flash is a sudden, explosive release of electrical energy that occurs when there’s a bridge or path for electricity to flow through an unintended medium, often the air.
When this happens, there’s an explosive release of heat, light, and force, resulting in dire consequences, from severe injuries and equipment damage to the outbreak of fires. The temperatures within an arc flash can be shockingly high, reaching up to 20,000°C, leading to devastating thermal injuries.
The force generated from the explosive release can be powerful enough to knock workers off balance, potentially causing traumatic injuries or even hearing damage. Beyond its immediacy, its aftermath often brings unforeseen disruptions in operations and a steep surge in repair costs.
High Voltage Systems: A Potential Hazard
High-voltage systems are integral components in many plants, facilitating the transmission of large amounts of electrical power. However, they come with inherent risks.
The sheer amount of electrical energy present can cause severe injuries or fatalities if mishandled. Direct contact can result in electrocution, while indirect contact might lead to arc flashes or other electrical discharges. Moreover, high-voltage systems can be a source of electrical fires if any malfunction occurs.
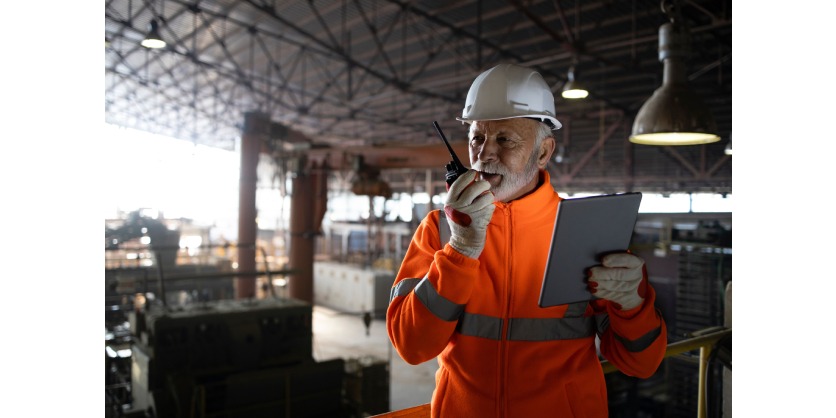
Here are a few strategies for mitigating risks associated with high-voltage systems:
- Regular maintenance and inspection: Periodic checks ensure that the equipment remains in optimal working condition, reducing the chances of malfunctions or breakdowns.
- Training and education: Equipping workers with the knowledge and skills to safely handle high-voltage systems is pivotal.
- Emergency medical equipment: High-voltage areas should be equipped with essential medical supplies, including a workplace first aid kit to address emergencies that may arise during maintenance or operation
- Safety gear and equipment: Providing and mandating appropriate safety gear, such as insulated gloves, safety goggles, and flame-resistant clothing, can reduce the risk of injuries from unexpected electrical discharges.
- Clear labeling and signage: Clearly marked areas inform workers about high voltage zones, ensuring they exercise added caution when operating near or within these zones.
- Restricted access: Only trained personnel should have access to high-voltage areas.
How Effective Communication Can Prevent Electrical Accidents
Effective communication in plant operations means relaying pertinent information clearly, concisely, and timely. A minor oversight can lead to severe consequences.
For instance, clear communication about scheduled maintenance can prevent the accidental energizing of a circuit being worked on. Similarly, real-time updates about system status, potential issues, or changes in operational protocols ensure that all team members are aware of and can adapt to the current situation, reducing the risk of accidents.
The Role of Human Interaction in Electrical Safety
While technology has evolved, providing us with automated systems and advanced tools, the human element remains irreplaceable in electrical and plant operation safety in general. Humans possess intuition and the ability to make judgments in unprecedented situations.
They can also interpret nuanced signals that machines might overlook. Yet, this human advantage is hinged on the quality of worker interactions. When information is shared efficiently, teams can collectively analyze situations, brainstorm solutions, and preemptively tackle problems before they manifest into tangible hazards.
Communication Strategies for Hazard Mitigation
Here are pivotal communication strategies that can significantly mitigate hazards in plant operations:
- Standard operating procedures (SOPs): Drafting and implementing comprehensive SOPs ensures that all employees are on the same page when it comes to handling equipment and dealing with potential hazards.
- Feedback mechanisms: Encouraging a culture where feedback from superiors and peers is valued and acted upon can help in identifying areas of improvement in communication protocols.
- Regular safety meetings: Periodic meetings focused on safety can serve as platforms for discussing potential risks, sharing experiences, and collectively brainstorming solutions.
- Use of technology: Utilizing modern communication tools, like instant messaging apps or dedicated safety software, can expedite the process of information dissemination during emergencies or routine operations.
- Clear signage and visual aids: Visual cues are a universal mode of communication. Ensuring that electrical areas, high-risk zones, and equipment are clearly labelled can provide instant information, reducing the scope of misunderstandings.
The Importance of Training and Education
The world of plant operations, especially in the electrical domain, is constantly evolving. With new technologies emerging and processes becoming more complex, the importance of regular training and education cannot be overstated. It is crucial for improving individual competency and plays a role in enhancing overall safety and operational efficiency.
Proper training equips the staff with a comprehensive understanding of systems, machinery, and safety protocols, which reduces the margin of error. Moreover, educated individuals are better equipped to anticipate potential issues and take preventive actions rather than just reactive measures.
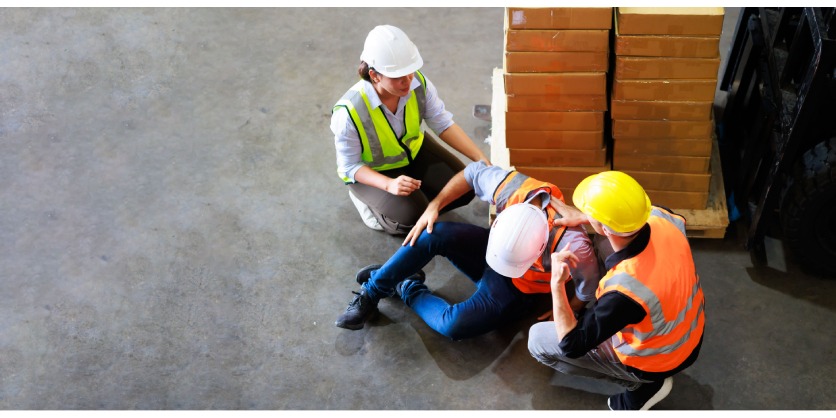
You can start by scheduling regular training sessions where workers get a refresher on safety guidelines for manufacturing settings . Practical sessions, safety protocol drills, and certification programs are also components of effective training. Promoting interactive workshops can foster collaborative learning and address real-world challenges.
Prioritize Regulatory Compliance and Standards
Adherence to regulatory compliance and standards is crucial in plant operations. These standards, set by industry experts and governing bodies, ensure both the safety of the workforce and the efficiency of operations.
Staying compliant mitigates risks and safeguards organizations from potential legal consequences and penalties. Regular updates to these standards reflect the industry’s growth and technological advancements, making it essential for plant operators to stay informed and adapt accordingly.
The Bottom Line
In plant operations, where technology and human expertise converge, effective communication emerges as the cornerstone of safety and efficiency. Each mishap averted and each streamlined process can be traced back to clear, concise interactions.
Ignoring this vital component can lead to grave repercussions, while embracing it can elevate operational standards. Let this be the catalyst for reevaluating your plant’s communication measures, ensuring a safer, more productive environment for all.
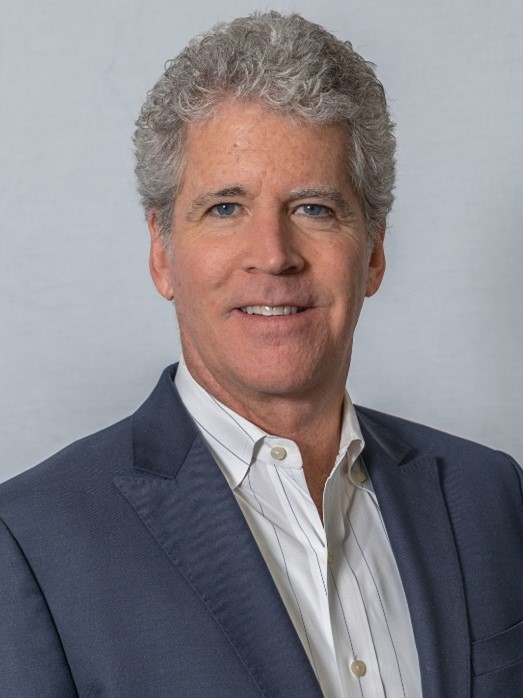
Author: Rick Farrell, President, PlantTours
Farrell is North America’s foremost expert in improving manufacturing group communication, education, training and group hospitality processes. He has over 40 years of group hospitality experience, most recently serving as President of PlantTours for the last 18 years. He has provided consulting services with the majority of Fortune 500 industrial corporations improving group communication dynamics of all types in manufacturing environments.