Economic Foresight: Modernize Systems Sustainably with Retrofits Instead of Buying New Ones
March 4, 2025
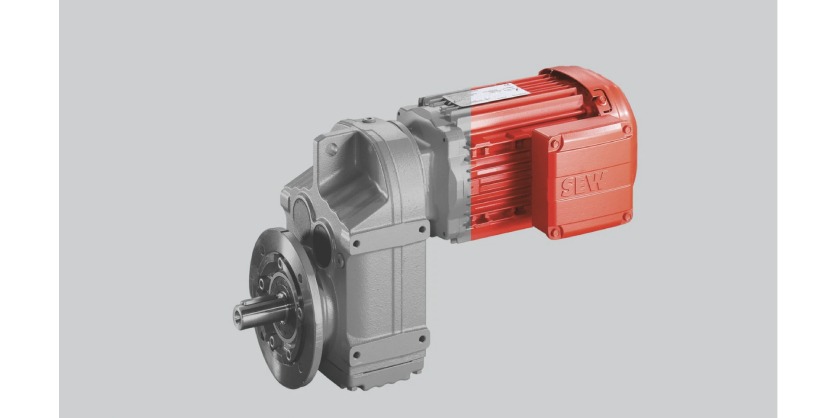
Manufacturing companies are facing major challenges: rising costs, strict regulations and the pressure to work more sustainably. In this uncertain economic situation, purchasing new machines is often risky and too expensive. Retrofitting offers a cost-effective and efficient alternative: modernizing existing machines to the latest state of the art not only saves money, but also time and resources. Improved drives, optimized control systems and modern technologies such as data-based monitoring reduce energy consumption, lower maintenance costs and increase production capacity.
Projects such as the retrofit of a 40-year-old conveyor system at ZF Friedrichshafen AG or a pasteurization system at Lindauer Bodensee-Fruchtsäfte GmbH show what this looks like in practice. Today, both companies benefit from energy-efficient technology, fewer breakdowns and future-proof production.
Why retrofitting is particularly important in economically uncertain times
In times of economic uncertainty and increasing cost-cutting measures, retrofitting is a strategic decision that helps companies to modernize their systems in a cost-effective and future-proof manner. Companies can save themselves the high investment costs for new machines while still significantly improving their production capacities.
Retrofit at SEW-EURODRIVE – Customized solutions
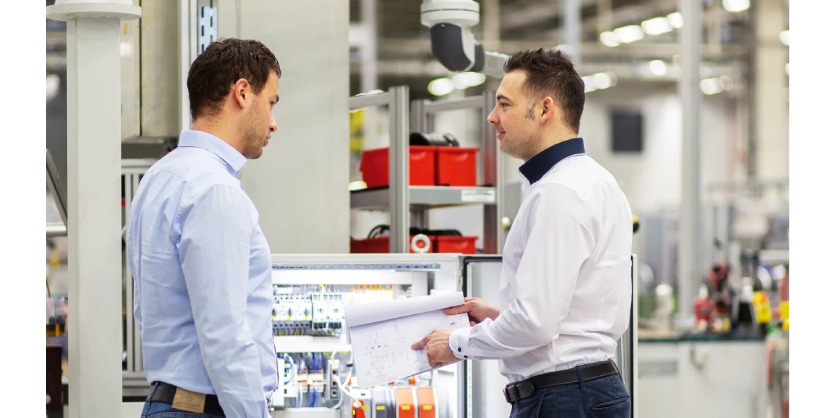
SEW-EURODRIVE offers customized retrofit solutions that are tailored to the specific requirements of the customer. From retrofitting old drive technology to modernizing the entire system – they update systems with up-to-date drive solutions and integrate modern technologies from their product portfolio. In doing so, they always pay attention to legal requirements and the specific needs of production.
- Retrofitting components: Here they replace individual drive components in a targeted manner without having to tackle the entire system straight away. The advantage of selective modernization is not only the cost savings, but above all the minimal downtime. And because they work with modular solutions, they can act flexibly: they tailor each measure to the specific requirements.
- Retrofitting systems: For more extensive projects, they modernize complete systems to bring the entire system up to date – from the control system to the mechanics. The special added value? They control the entire project management. Their customers can rely on them to seamlessly coordinate every phase – from planning to commissioning. This saves time, reduces risks and ensures optimum results.
Why is retrofitting a smart decision?
1) The cost issue: cheaper than buying new, faster amortization
In economically uncertain times, when companies are becoming increasingly cautious about investments, retrofitting offers a convincing solution. The decision to replace old machines with modern technologies may seem tempting at first, but the cost of a new purchase is often considerably higher than that of retrofit measures. Retrofitting makes it possible to realize significant cost savings and at the same time bring production facilities up to the latest state of the art. The reduction in investment costs and the short amortization period make retrofitting a particularly attractive choice.
2) Energy efficiency: A key to reduced operating costs
More and more companies are relying on reducing their operating costs and optimizing their energy consumption at the same time. A decisive advantage of retrofitting is the increase in energy efficiency. By replacing outdated drive systems, control systems and motors with energy-saving technologies, companies can significantly reduce their energy consumption. Especially in times of rising energy prices, this advantage represents a significant competitive edge.
3) Increased production capacity and flexibility
Modernized systems also offer greater flexibility and production capacity. With retrofits, companies can adapt the performance of their machines to the constantly changing requirements of production. Modern control systems and automation technologies also offer the opportunity to optimize and automate production processes. This leads to an increase in productivity and a reduction in production errors.
4) Less downtime through retrofitting
Another advantage of retrofitting is the reduction in downtime. By gradually replacing and adapting machines and systems, companies can maintain their production even during the retrofit process. This minimizes downtime and ensures continuous production, which is particularly important in industries with tight schedules and high production requirements.
5) Sustainability through retrofitting
In times of growing environmental awareness, sustainability is another argument for retrofitting. The modernization of systems helps to reduce the ecological footprint. By reusing old machines, companies are helping to conserve resources and avoid waste. This not only fits in with global sustainability goals, but also helps companies to position themselves as environmentally conscious brands.
6) Compliance with legal requirements
Another important point is compliance with legal requirements. By modernizing systems, companies ensure that their machines and systems comply with current standards and regulations. This not only guarantees legal security, but also long-term competitiveness. Retrofitting ensures that companies are able to adapt to new legal requirements without having to purchase their entire production from scratch.
From the field
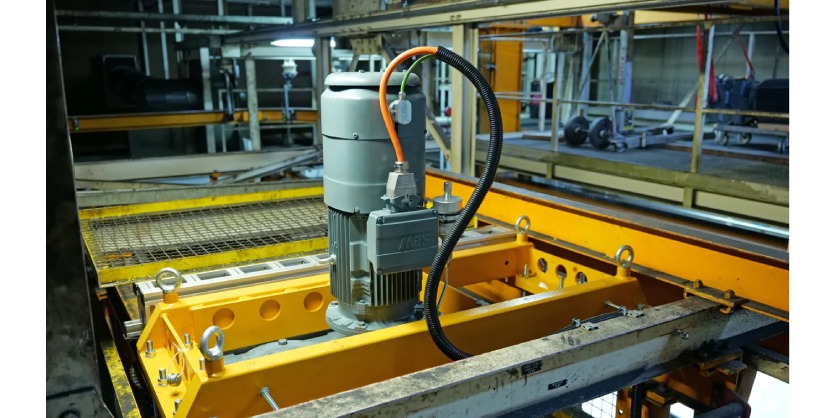
Examples from industry show how retrofitting can be successfully implemented. Two current retrofit projects from SEW-EURODRIVE show how companies benefit from energy-efficient technology, fewer breakdowns and future-proof production.
Modernization in record time at ZF Friedrichshafen AG on Lake Constance
ZF Friedrichshafen AG is a good example of the cost savings that can be achieved through retrofitting. In this project, the 40-year-old drive of a conveyor system in the drying oven for truck gearboxes was modernized. The original drive was replaced by a modern system that included a parallel shaft geared motor and a frequency converter. This solution led to a significant increase in energy efficiency and reduced maintenance costs.
The challenge was that access to the old drive system was difficult and the system was central to ZF’s production processes. SEW-EURODRIVE’s team developed a customized solution that allowed the new drive system to be installed without interrupting the production flow. The modernization was completed in just three days, resulting in a considerable reduction in downtime and a significant increase in efficiency. Find out more about the project here.
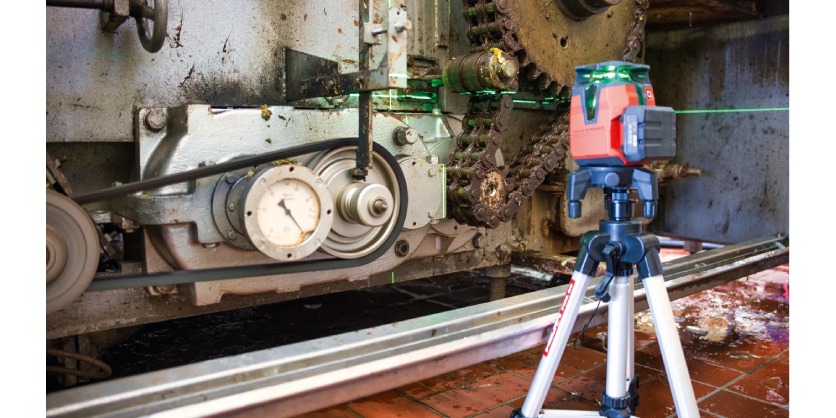
Modernization for sustainable production at Lindauer Bodensee-Fruchtsäfte GmbH
The pasteurization plant at Lindauer Bodensee-Fruchtsäfte GmbH had been in operation since 1977. After all these years, the family-run company decided to modernize it, as the original adjustment gears at the inlet and outlet of the system were worn out and spare parts were no longer available.
SEW-EURODRIVE developed a cost-effective and innovative solution: A new double geared motor including all necessary adaptations – adapted to the high hygiene standards that must be met in the beverage industry. The solution concept was more cost-effective and modern than a general overhaul of the existing drives, minimized downtimes and reduced energy consumption. As the drive units were pre-assembled in their service centre, installation on site was completed in no time at all with minimal downtime. With modern technology, the company can once again concentrate fully on juice production – in a sustainable and resource-saving way. Find out more about the project here.
Conclusion: Retrofit as a strategic solution
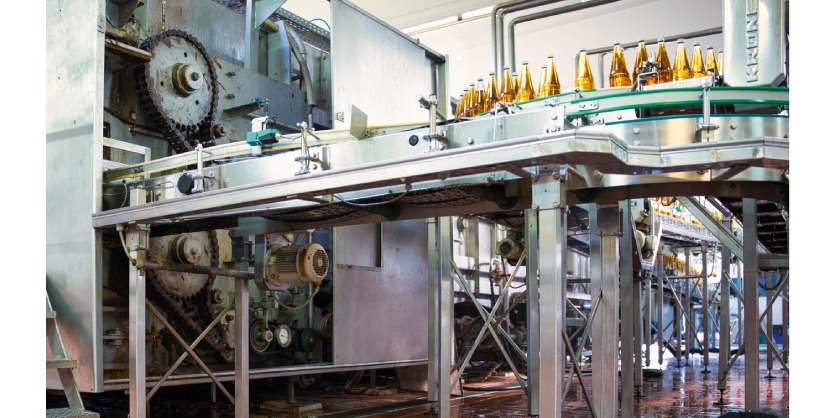
In times when every euro counts, retrofitting offers an attractive opportunity to modernize existing production systems and make them more efficient without the high costs of a completely new purchase. Retrofitting is a sustainable solution that helps companies to remain competitive – in the long term. Due to the cost savings, energy efficiency, increase in productivity and sustainable use of resources, retrofitting is a solution that is both ecologically and economically beneficial. Companies that use retrofitting can bring their machines and systems up to date without having to take the risks of purchasing new equipment.
Now is the time to lay the foundations for a successful future with retrofitting. Contact SEW-EURODRIVE and find out how you can modernize your systems more economically so that your company can remain competitive.
And after the Retrofit?
SEW-EURODRIVE not only offer the retrofit service, but also a wide range of supplementary services that round off the modernization process. These include, for example, our 24-hour service hotline, where they offer you technical support around the clock, including express orders and repairs. With their operating and maintenance concepts, they tailor the maintenance of your system optimally to your needs. And to ensure that everything runs smoothly in your production processes, their experts support you with comprehensive training, especially during the start-up phase.
Related Story
Why Choose SEW-EURODRIVE VFD’S?
SEW-EURODRIVE’s decentralized drive technology has everything you need – compact drive units, decentralized inverters and motion controllers for field use – and everything can be easily combined and recombined as required. This is all possible because the standardized control and communication architecture forms the perfect pairing!