Eaton: Variable Frequency Drives Enhance Energy Efficiency at Greenhouse Waste Recycling Plant
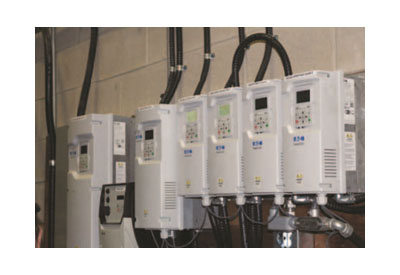
April 30, 2018
Sponsored by Eaton
In today’s market operational efficiency is essential. Whether it be upgrades to aging infrastructure or the application of new products into a modern facility there is a market wide drive to ensure that facilities are energy efficient and have proper control infrastructure. The push for efficiency has gone beyond the narrow consideration of manufacturing to incorporate a wide array of facilities that utilize modern machinery and control systems.
One of the primary concerns in regard to energy consumption and machine wear is the frequency or speed of the motors. If a motor is improperly controlled, it consumes more energy than required and can create operational concerns as the motor and related equipment wear out faster. This issue was resolved through the application of Variable Frequency Drives (VFD’s) that have the ability to adjust a motors speed to meet the requirement of the electric motor’s load and change its frequency depending on the task it is operating.
In many instances motors are used to control operations that perform multiple tasks and require varying frequencies (or motor speeds). Without proper use of VFD’s motors will operate at a consistent level that results in high energy costs, machine wear, and potentially poor results in terms of task efficiency if the motor frequency is not adjusting to perform optimally for different tasks.
The current case study identifies the value of VFD’s in operations that perform multiple tasks that require varying motor speeds, as well as ensuring optimal energy efficiency and operational performance.
Background
In line with the drive for energy efficiency this study identifies optimization efforts at a revolutionary greenhouse waste recycling plant in Ontario. When we think of recycling plants Greenhouse waste is not often the first recyclable material that comes to mind, however as we continue to focus on environmental issues advanced recycling of various materials are exceedingly important. And like other recycling facilities the material recycled is varied and requires a system capable of addressing the various recycling methods utilized for differing materials.
The facility in question is being driven by AR3C International’s WECO2 Parks, which acquired Agricultural Technology Incorporated (ATI), the original founder of the facility. The Acquisition was the result of ATI’s large Greenhouse services throughout North America and their offering of innovative portable equipment and technology. ATI is a leader in greenhouse services and recognized the need to advance the methods and technology utilized in recycling greenhouse waste.
Steve Posthumous, an early pioneer in the industry, helped found ATI in 1995 and in 2000 purchased a small farm that gradually grew into the agricultural by-product processing facility. Early on the facility recognized the importance of operational efficiency and implemented a motor control centre. As it grew Steve recognized the need to continue advancing the facility’s operation and systems. ATI engaged Eaton to advance the facility’s operational efficiency and over the first decade several projects saw the implementation of VFD’s, metering applications and switchgear.
Today, the greenhouse services industry grows seven to 10 percent annually and AR3C currently holds a significant percentage of the market share. WECO2 Parks consistently reinvests its proceeds into new machinery, services,
and systems to ensure it is utilizing the most advanced technology and efficient operations. By 2015, the company had developed an emerging concept for a fully integrated and energy self-sufficient plant that would operate on recyclable materials available from the greenhouse industry. Under the revolutionary design, plant waste, substrate, plastic and soil are removed, separated and recycled into fuel pellets, composite decking and nutrient-rich fertilizer tea. The pellets are burned in an onsite cogeneration plant to provide carbon-neutral heat and electricity.
As the initial power system upgrades had been implemented by Eaton, Matthew Posthumous, CEO of AR3C, and the company opted to continue working with Eaton for the new project. In early 2016, Posthumus contacted AR3C’s Eaton distributor, WESCO, to kick off the new project.
Challenge
The biggest challenge for AR3C was ensuring that operational efficiency was maintained, a fact which had not been feasible with standard drives in place. Since the composition and density of the waste material going into the recycling plant is always changing, most of the material handling and processing equipment needed the ability to adjust speeds on the fly, while remaining synchronized for optimal output. It was also essential that the new system being implemented was run entirely off green energy. For example, in one process, as vines are removed, the heat that radiates off of the engines is able to run a series of dryers.
The recycling system first takes the nutrients out of the vine and then other vine materials are processed into fuel pellets to help power the facility. AR3C engineers had originally built most of the specialized equipment for the self-sufficient recycling plant themselves. They had also already purchased the motors and process controllers before coming to the realization that they needed VFDs to fully utilize the potential of their advanced design. “We needed drives that had a lot of flexibility already built into their processing from the start,” said Posthumus. With the other equipment in place it was essential that the VFD’s were compatible with the existing equipment.
Eaton was able to step in and recommended drives ranging from 3HP to 100HP be implemented to power several applications in the plant design—conveyors, presses for materials, fans, pumps and steam valve controls. Precise process control was essential, and the project required drives capable of handling multiple conveyors with varying load conditions. And, finally, because AR3C wanted to make its solution available worldwide, the drives also had to have universal ratings and certification. AR3C’s WECO Park solution adds value by creating a circular economy, developing regions that have no access to electricity by generating local power and thermal capacity—creating the opportunity for agricultural and manufacturing growth based on the waste products already available locally.
Solution
Eaton’s previous experience within the facility as well the comprehensive support of the local Eaton technical sales representative, the region’s technical application engineer, extensive online training tools and universal ratings and certification, made Eaton the logical choice to supply the needed VFD’s. As a result, Eaton installed its DG1 VFD’s in the plant to offer robust, state-of-the-art design over the power range required. The installation process was simple as the compact size of NEMA 1 and NEMA 12 enclosures currently in place allowed for direct installation of the VFD’s anywhere in the plant. The implementation of comprehensive and flexible control through I/O and onboard communications offered quick and simple integration with the process controller.
As noted several of the facilities operations required flexible settings to allow for different speeds and volume rates. One of the installed VFD banks operated a drying system that after installation allowed for proper settings to be utilized for different products and varying moisture rates, satisfying a prime concern of AR3C. In total 5 VFD banks were installed that allowed for full flexibility and optimal control throughout the plant.
Results
It is beyond question that the implementation of proper drives and control infrastructure allows for optimal energy use and plant efficiency. Beyond the benefits to the plant operations the recycling process itself saves taxpayers from having to open another landfill. Using AR3C’s system, only about two percent of agricultural waste goes back to landfills; everything else gets repurposed. “The project has had positive results on our bottom line, labor management, protocols, pre-set controls and more,” said Posthumus. The application of VFD’s has essentially increased productivity and efficiency across the board.
AR3C is unique in that it creates its own sustainable energy source, however ensuring that the longevity of that sustainability is maintained has been greatly increased through the application of VFD’s. On average electric motors can be responsible for up to 65% of power consumption in facility operations, but the installation of VFD’s can reduce energy use by as much as 70%. In a plant where utilizing a sustainable energy source is essential the reduction in energy use is a key component to ensuring long term sustainable operations.
Productivity increases result form smooth start-ups and transition between frequency, which result in higher revenues. The increased revenue allows for AR3C to continue to reinvest proceeds and be driver force in the utilization of advancing technology and sustainability. And finally, equipment life is extended as a result of less maintenance and required down-time by protecting motors from issues such as electro-thermal overload, phase protection, under voltage or over voltage.
AR3C expects to take its carbon-neutral plant throughout the world for use wherever food or plant materials and plastics can be recycled through its WECO 2 branded eco parks. But first it will operate with local partners to fine-tune its recipes and process management options. “AR3C can now develop and test a range of recipes and management systems because we have the confidence that VFDs can fully regulate the necessary speed,” explained Posthumus.
Online learning components are available to drive adoption through self-taught use/application of the units. AR3C is incorporating Eaton’s online learning resources as part of its own rollout process. The AR3C teams work with the drives online before each install; this helps facilitate discovery and understanding of the full capabilities of the new drives. “It’s like an orchestra,” concluded Posthumus. “And it plays a good tune. No other greenhouse services company has achieved this level of by-product recycling coordination all in one spot.”
http://www.eatoncanada.ca/EatonCA/index.htm