Comparing Eight Different Types of Servo Motors to Stepper Motors
January 25, 2024
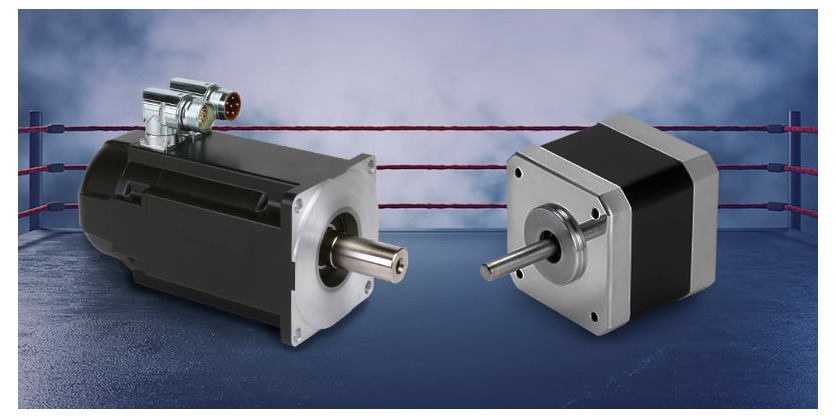
While servo motors are often chosen as a high-performance alternative to stepper motors, their variety and specialized applications are less commonly understood. This article aims to explain the differences between the types of servo motors, enhancing your understanding of when and why to use each type.
AC Servo Motors
AC servo motors excel in industrial applications due to their high power and efficiency. These motors, powered by alternating current (AC), are ideal for precision tasks in automation and robotics. They stand out for their robust construction, handling high cycle rates and dynamic accelerations, which makes them suitable for CNC machinery, conveyor systems, and packaging machinery.
One key advantage of AC servo motors over stepper motors is their continuous rotation capability, ensuring uninterrupted operations. They also maintain high torque at high speeds, unlike stepper motors, which lose torque as speed increases. This feature is crucial for high-speed automation lines where consistent power and speed are necessary.
Brush DC Servo Motors
DC brush servo motors are a popular choice for precision-based applications, particularly where size and control are critical factors. Operating on direct current (DC), these motors are known for their compact size and ease of control, making them ideal for smaller-scale operations where space and precise motion control are paramount.
Applications for DC servo motors are diverse, ranging from small-scale robotics to precision medical equipment. They are especially favored in applications that demand precise positioning and responsiveness, such as in 3D printers, camera focus mechanisms, and smaller automated systems.
Comparing DC servo motors to stepper motors, the former exhibits superior speed control and a more rapid response to commands like starting, stopping, and reversing. This responsiveness is due to their inherent design, which allows for quick adjustments in speed and position. In contrast, stepper motors, while reliable, can be less responsive and offer less nuanced speed control.
A notable example of a DC servo motor that exemplifies these qualities is the Maxon RE40 DC Motor. This motor is particularly well-suited for applications requiring fine-tuned speed control and swift responsiveness.
Brushless DC Servo Motors
Brushless servo motors are celebrated for their high efficiency and minimal maintenance needs. The absence of brushes in their design is a key feature that sets them apart. This brushless construction not only enhances their efficiency but also significantly reduces the wear and tear commonly associated with mechanical brushes in traditional motors.
A primary advantage of brushless servo motors is their longevity and reliability. Without brushes, there’s less friction inside the motor, leading to lower heat generation and reduced risk of mechanical failure. This attribute translates to a longer lifespan and less downtime for maintenance, which is crucial in industrial applications where continuous operation is vital.
Brushless servo motors are ideal for scenarios that demand both durability and minimal maintenance. They are particularly well-suited for high-precision applications where motor dynamics are critical, such as aerospace, medical devices, and high-speed automation.
A great example of a brushless servo motor that embodies these characteristics is the Kollmorgen AKM2G Servo Motor. This motor is designed for applications that require long life and minimal maintenance, making it an excellent choice for demanding industrial environments.
Linear Servo Motors
Linear servo motors, a specialized type among servo motor types, excel in direct drive applications, offering high precision in linear motion. Their direct drive design eliminates the need for mechanical transmission elements like ball screws, resulting in simpler, more reliable operations with reduced wear.
These motors are ideal for applications where precision linear movement is crucial, such as in advanced industrial automation and precision machining. Unlike rotary servo motors, linear servo motors provide smoother and more efficient motion control due to their straightforward drive mechanism.
A notable example is the Nippon Pulse Linear Shaft Motor, designed for high-precision linear applications.
Continuous Rotation Servo Motors
Continuous rotation servo motors are a unique category within the types of servo motors, characterized by their ability to rotate indefinitely. This feature makes them highly suitable for applications that require a full, uninterrupted range of motion, such as in robotics and conveyor systems. Their design allows for constant, smooth rotation, which is essential in automated processes and robotic applications where continuous movement is necessary.
The primary difference between continuous rotation servo motors and limited rotation servos lies in their rotational capabilities. Standard servos are typically constrained to a certain angle, usually less than 360 degrees, limiting their range of motion. In contrast, continuous rotation servos can turn endlessly in either direction, providing greater flexibility and functionality in applications where unlimited rotation is advantageous.
Limited Angle Torque (LAT) Servo Motors
Limited Angle Torque (LAT) servo motors are specifically designed for applications that require only a limited range of motion. This makes them a distinct type within the various servo motor types. The design of LAT servo motors is tailored to deliver high torque within a restricted angular range, typically less than 180 degrees. This limited rotation capability is not a drawback but rather a specialized feature for certain applications.
The specific applications where LAT servo motors excel include control surfaces in aerospace and certain aspects of robotics. In aerospace, these motors are crucial for controlling flaps, rudders, and ailerons, where precise movement within a defined angular range is essential for the safe and efficient operation of aircraft. Similarly, in robotics, LAT servo motors are used in joint control where a full rotation is neither needed nor desired, providing precise control and stability.
Smart Servo Motors
Smart servo motors represent a modern and advanced segment within the diverse types of servo motors. Their defining feature is the integration of control electronics and feedback mechanisms directly into the motor. This integration allows for sophisticated control and monitoring capabilities, making them an intelligent choice for modern applications.
One of the advanced features of smart servo motors is their ability to self-regulate and adapt to varying operational conditions. The integrated control electronics enable precise motion control, while the feedback mechanisms provide real-time data on motor performance. This combination results in improved efficiency, accuracy, and reliability.
Smart servo motors are particularly valuable in applications where compact integration and intelligent control are paramount. They are ideal for space-constrained environments where external control units would be impractical. Their smart features make them suitable for advanced robotics, automated manufacturing systems, and precision medical equipment, where their compact size and integrated intelligence can significantly enhance performance and functionality.
A notable example in this category is the Maxon IDX Compact Integrated Servo. This motor exemplifies the advantages of compact integration and intelligent control, making it an excellent choice for cutting-edge applications.
Miniature Servo Motors
Miniature servo motors are a specialized category in the diverse range of servo motor types, characterized by their remarkably small size. These motors are engineered for use in compact, precision applications where space is at a premium and precise control is necessary. Their diminutive size does not compromise their performance; rather, it allows them to operate efficiently in confined spaces.
The primary application area for miniature servo motors is in medical devices, where precision and reliability are paramount. They are extensively used in surgical tools, diagnostic equipment, and other medical instruments where precise movement and control are crucial. Their small footprint allows them to fit into intricate medical devices without sacrificing power or precision.
When compared with larger servo motors, miniature servo motors have a unique suitability for tasks that require micro-movements. While larger servos are designed for high power and torque in industrial applications, miniature servos excel in scenarios where delicate and precise movements are essential. Their design allows for fine control, making them ideal for applications in micro-robotics, optics, and miniature pumps.
A fitting example of this type of motor is the Maxon’s ECX Series Brushless Servo Motor. This motor is specifically designed for applications that require precise control in a compact package, making it an excellent choice for medical and other precision-driven applications.
Wrap-Up
Each type of servo motor has distinct characteristics that make it suitable for specific applications. Understanding these differences is key to selecting the right motor for your needs, whether it’s for precision in a small device or robust performance in an industrial setting.
Related Story
Electromate Announces Pre-Order Availability of Universal Robots’ New UR30 Cobot
Electromate Inc., a leading Distributor of Precision Robotic & Mechatronic Solutions, is excited to announce the pre-order availability of Universal Robots’ latest innovation – the UR30 collaborative robot (cobot). The UR30, boasting a 30 kg payload capacity, is the newest addition to Universal Robots’ cutting-edge cobot lineup.