Case Study: Launching a Nationwide Equipment Network
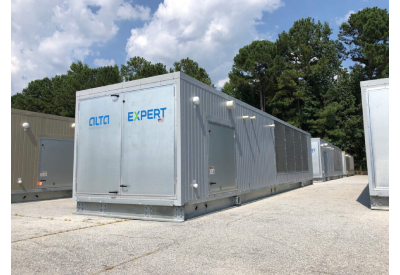
August 2, 2022
ALTA Refrigeration achieves faster, easier product development and servicing with groov EPIC and MQTT
What’s the secret to providing superior service and staying competitive in a changing market? Well, you might learn something from ALTA Refrigeration’s experience.
Over ten years, it transformed itself from a custom engineering services company into a scalable industrial equipment manufacturer, using an edge-oriented control architecture to efficiently manage a growing installed base.
Each EXPERT follows a standard, reliable design that can be mounted on the roof above the area it serves.
Originally started in 1975 as Industrial Refrigeration Services, ALTA has been designing and installing refrigeration systems across the United States for more than 45 years. And for a long time, they were large, custom-designed systems that used a central machine room to deliver refrigerant to various facility areas through long, overhead piping runs.
“Our customers’ biggest concern is their power bill,” notes Peter Santoro, controls engineer at ALTA. So ALTA’s systems stood out for the level of control they offered, including multiple operating modes that allowed the equipment to be tuned for optimal efficiency. However, it required significant time to design and program each unique system, and competitors were able to steal some of their market share with cheaper, simpler offerings.
“Competitors could use 20-30 cheaper units with control limited to a dumb thermostat to compete against one of ALTA’s large systems,” Peter adds. ALTA knew it couldn’t compete by reducing its product quality, so the company looked for a way to standardize its offering without sacrificing features.
We’re the Experts
In 2013, ALTA introduced its EXPERT series of modular refrigeration control units. Each unit used a standard, more reliable design, and could be mounted on the roof above the area it served, simplifying installation.
According to Peter, ALTA poured its previous years of experience with system design into creating the EXPERT product line.
“A single EXPERT has almost as much I/O as an entire centralized system, and because the units are much smaller, the wiring and conduit runs are incredibly short, allowing us to cram in a ton of sensors. The units themselves are also incredibly efficient. We analyze both the external ambient conditions and refrigerated space and do real-time thermodynamic calculations. This lets us do variable capacity refrigeration, and only run exactly the amount of refrigeration as needed.”
“All motors are on variable speed drives. We also design many of the sensors we use on the system, allowing us to get precise valve positioning and to monitor refrigerant levels throughout the system. We make good use of Hall effect sensors in various configurations to monitor refrigerant levels and motor positions. There is also a dedicated energy monitor on each unit so we can monitor voltages and power usage.”
Since all EXPERT systems are essentially the same, Peter and his colleague, Todd Hedenstrom, could put a higher degree of focused engineering into creating a robust and complete solution that works with many different applications.
A Good Problem to Have
The product rollout worked. EXPERT sales quickly grew to become the bulk of ALTA’s business. ALTA has sold nearly 600 units and is typically sold out into the next year.
But growth brings its own challenges. While a handful of EXPERTS can replace one of the older, custom systems, ALTA now averages eight units per site. And service contracts drive ALTA’s revenue. With only a small control engineering team, servicing the growing installed base became time-consuming.
“Since we are installing sites at a much faster rate, scalability was our main concern,” says Peter. “We service most of our sites, so we need visibility into everything… Our systems have a long lifetime and service is super important to our customer relationships… but we sell probably 70 of these a year and it gets hard to manage all that.”
On top of that, there were some aspects of their previous designs related to system maintenance that got in the way. Their control system required many steps to properly update control strategies in the field, including exchanging files between the control engine and the web server they used for remote connectivity. It was a sometimes-fragile process that made it difficult to train technicians.
Previously, ALTA had also left the details of remote connectivity to each customer. This increased the team’s workload, since they usually checked in on each site every day and had to use a different method to connect to each one (VPN, Citrix, LogMeIn, TeamViewer, etc.).
If they were going to keep up with the pace of growth, Peter and Todd needed a way to remove these bottlenecks in service delivery.
Where to Start?
ALTA’s centralized control system design was built around an industrial PC (IPC) running custom C++ code on top of a distributed I/O system from Opto 22. “We’ve been Opto people for something like 37 years,” Todd adds, so when he and Peter designed the original EXPERT, they simplified the system by replacing the IPC with an Opto 22 PAC controller.
This approach was an improvement in some ways since all the components of the system could be managed through the PAC Control engine. But it didn’t go as far as they needed. It still required a multi-step update process and didn’t give them as much data access as they wanted. So they began exploring Opto 22’s newer groov EPIC system.
.EPICs, or edge programmable industrial controllers, provide a new option for industrial control systems that combines the best features of PLCs and IPCs. PLCs offer a rugged, purpose-built design with many, typically expandable, options for I/O and device communication.
IPCs offer general-purpose processing power, storage, and networking options to support more demanding applications and broader functionality like cybersecurity, database management, and high-level programming languages. EPICs support all of these functions on a single backplane but typically without the complexity of maintaining a full Windows OS environment.
ALTA upgraded the EXPERT control system to Opto 22’s groov EPIC to gain access to more flexible control and communication options
Peter and Todd wanted to use the power and flexibility of an EPIC to develop a custom solution that reduced the effort required to deploy bug fixes and product updates. They also wanted a single solution for remote monitoring and thought that groov EPIC’s array of communication options would make that easier.
Building a Better Fridge
Peter and Todd dove seriously into using groov EPIC’s operating system shell to port their PAC Control application to C++, passing over other control engine options to leverage the language they were most familiar with. “We tried CODESYS on the EPIC,” says Peter, “but the freedom and flexibility of going with C++ was too good to pass on.”
groov EPIC uses a custom Debian Linux distribution that has been stripped down to the essential components, reducing its memory footprint and potential cyber-attack vectors. Additionally, it has been cryptographically signed with Opto 22’s private key to prevent installation of any unapproved software. However, Opto 22 also exposes access to the EPIC’s Linux command-line using the secure shell protocol (SSH) and a free Shell Access license (GROOV-LIC-SHELL).
“All development is done remotely through the SSH connection in [Microsoft] Visual Studio,” Peter explains. You can find the guide Todd posted in the Opto 22 user forums explaining how he set up this connection, which allowed him to develop programs in VS and compile them directly on his EPIC. Once Todd figured out this basic process, he and Peter were able to consolidate most of the control program into their C++ application along with many new features.
The program controls the installed I/O modules—voltage and current sensing inputs and discrete AC outputs—using Opto 22’s C++ OptoMMP SDK, or software development kit. The application also includes its own Modbus server that creates and manages connections to variable frequency drives, the local energy monitoring unit, and other remote devices.
“We [also] have our own REST API and webserver running on the C++ application,” Peter adds, “allowing us to create our own web page interfaces in HTML and Javascript… It’s a lot easier to build HTML stuff in familiar tools than with an HMI package… You can do anything.” That includes things like using Google’s Chart API to display energy metrics in the HMI.
Each EXPERT provides a local unit interface through an embedded web server that runs on the unit’s EPIC.
Each EXPERT’s web interface is served up from its EPIC controller. It includes prebuilt templates for different unit configurations and verifies system settings to help technicians identify configuration values that are out of range or not recommended. It also generates alarms as needed. Alternatively, customers can access unit data through the EXPERT’s Modbus server or REST API.
For managing groups of EXPERTs, ALTA uses a separate HMI server to read data from each unit and present a unified view of the entire system. “All of our sites are required to have a local interface for operators to see a global view of their refrigeration units, instead of having to manage network connections to hundreds of individual units,” Peter explains.
To create this site-level HMI, each EXPERT stores transient data in the shared memory “scratchpad” area of its groov EPIC. ALTA’s HMI server runs on Windows and uses Opto 22’s .NET OptoMMP SDK to retrieve this data from all units in 1-second increments. Data is stored in cyclical files that maintain a 1-week buffer, and the HMI server uses this data to generate trends, charts, and email notifications.
ALTA can also access this data remotely for troubleshooting recent events. By default, groov EPIC does not route traffic between its Ethernet ports, so ALTA can use the controller to create a security zone for each EXPERT. One port on each EPIC connects to a private network exclusively for the controller and its remote devices. The other port is connected to a common network between all the units at a given site, as well as the local HMI server.
This server is connected to the internet and uses MQTT to send and receive data, acting as a middleman for each individual EXPERT to the MQTT broker that resides in ALTA’s headquarters. When ALTA’s remote HMI requires new data, it sends a request to the local server over MQTT. The data is queried and sent back. External connections to local HMI servers are restricted so that the only traffic allowed through is from outbound MQTT TLS connections.
ALTA’s nationwide network connects each EXPERT to its central server through a local HMI and MQTT gateway.
Recently, ALTA also made it possible for their customers to access this remote server. The server has its own database that records temperatures and energy usage for each EXPERT in 10-minute intervals. Customers can log into a private web portal to generate reports directly from this data. Since groov EPIC provides an embedded MQTT client and network firewall, ALTA
“also tried doing unit-level MQTT [communications] to the broker,” Peter clarifies. “But with some of our units running on customer networks, it was impossible to guarantee they would allow a direct internet connection to the [EPICs]. That is why we shifted focus to only have our local site server be the device connected to the broker.”
The Coolest Service Around
ALTA’s central HMI aggregates data from across its installed base of EXPERT systems.
How are Peter, Todd, and the ALTA team doing now? In Peter’s opinion, “Our service and warranty programs are unprecedented.”
ALTA has built a nationwide HMI that aggregates data from its network of EXPERT units and highlights any issues the team needs to act on. Instead of spending hours every day to check on each site, they can monitor their entire installed base in minutes. They know when there is a problem, can input and track necessary work orders, track technicians’ locations, and monitor energy usage per unit. When an alarm occurs, the system creates an interactive timeline of events before and after.
“Often, we know what the problem is before the customer calls. We just need to drive there and fix it,” says Peter. “With the amount of data we get from our units we are capable of diagnosing the vast majority of problems remotely. This allows many of our end users to not even staff on-site maintenance… And no interfacing with third-party systems anymore. It’s all integral.”
“When we used to do centralized systems, a lot of IoT stuff was near impossible with how the old systems were structured. Because all the central systems could be drastically different, it was difficult to even consider a ‘dashboard’ to display them. Having a central web server or database was not even considered until we made the full transition to our EXPERT product line.”
“This solution was mostly developed to make our lives easier to support the systems. Having customers on here is just a big bonus now that everything is externally visible.”
ALTA’s central HMI continuously monitors its entire installed base, providing intuitive representation of system health across the country.
Servicing the systems themselves has also become much simpler now that Peter and Todd can manage the entire platform—I/O configuration, control strategy, communications, and networking—through a single device. “One of the best features we introduced was the ability to update the programs through our web interface… Now a batch program packages up all the program files into a .gz (compressed) file. Technicians can upload the file and restart the system… We send the tarball, they click update, and the system takes care of the rest. Much easier,” Peter says.
“We have a lot of experience with C++ here, so applying that to the EPIC controllers using Shell Access has allowed us to rapidly develop these custom solutions with a very small team… The lead engineer loves to make changes, so we’ve gone through hundreds of revisions.”
ALTA also uses the groov EPIC’s touchscreen as a maintenance interface inside the control cabinet. The native groov Manage application allows them to view and modify I/O and network settings directly on the controller without using a separate computer interface. Using the EPIC’s native HMI server, groov View, ALTA also provides technicians with local control options and basic information about the Linux program’s status.
ALTA’s nationwide network serves up performance data on every unit and allows the team to track and manage necessary work orders.
But Can It Get Even Cooler?
With EPICs as a foundation for their control platform, Peter and Todd continue to dream up even more service offerings. They are working on the ability to remotely update both the local servers and each individual EXPERT unit from their central webserver. The server will soon have its own REST API as well. With the correct key, a customer could grab the information from ALTA’s nationwide system without needing to interface with their local hardware at all. Additionally, ALTA is considering using the larger storage capacity of the groov EPIC PR2 processor (GRV-EPIC-PR2) to store the EXPERT’s process history buffer directly on the EPIC, rather than its local Windows servers.
Other new features are on their way as well, potentially including real-time operational adjustments based on local power rates. And with a large network of performance data to draw on, the team has also been evaluating integration with a cloud IoT platform for long-term data storage and predictive control.
Peter sums it up by saying, “It’s nice to have the EPIC as the IPC with I/O. It’s just simpler… We can do a lot with a little.” As of writing this case study, ALTA has deployed 200 EPICs in the field. EXPERT sales are booked solid through the coming year.
Contact Information
For more information, visit www.altarefrigeration.com or contact Opto 22 for free design guidance or technical support any time.