Analysing Backfeeding Events with the Help of Power Supply Data
August 9, 2023
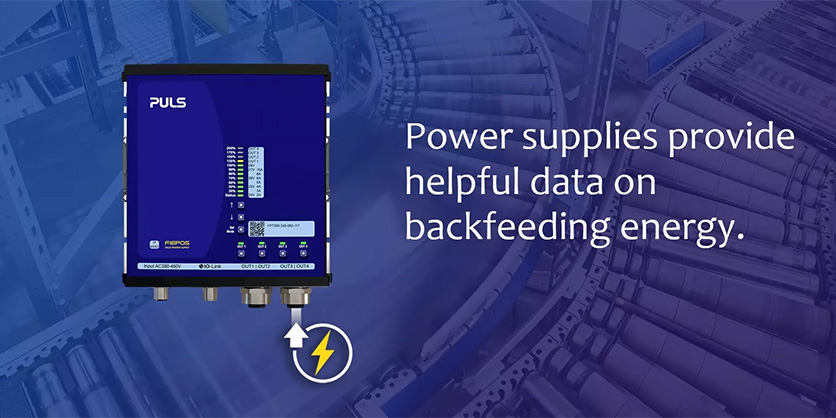
Backfeeding is a physical process that is highly desirable in many applications, such as electric vehicles, for the purpose of energy recovery. However, in an industrial setting, backfeeding can be a problem and lead to costly system downtimes if the power supply units fail. In this blog article you will learn how power supply data can help you to identify those backfeeding events and take measures.
Resistance to Backfeeding: Why is it Important for Power Supplies?
Rotating machine components, such as drum motors, store kinetic energy which they feed back during braking in the form of voltage to the output of the power supply. On its output side, the power supply can absorb a certain amount of this energy in its output capacitors. At the same time, the output voltage increases accordingly.
The resistance to backfeeding events describes the maximum voltage allowed at the output of the power supply. If this figure is exceeded, the power supply will switch off and the system or machine will shut down.
However, even plant operators are often not aware of the backfeeding figures in real operating conditions. There is a lack of specific data concerning the frequency and the maximum values.
A detailed real-life load profile is helpful when choosing a suitable power supply during the planning phase and when analysing faults in the operating phase. The question is: how can this data be obtained?
The Power Supply as a Data Source
The power supply manufacturer PULS has developed the FIEPOS family of power supplies for decentralized use and has integrated the option of application analysis. The power supply functions like a sensor. It records a variety of application-related parameters (for example, voltage, current, temperature) and makes them available in real-time.
As the decentralised power supply is on the field level, PULS logically uses an IO-Link interface for communicating these data. Therefore, the FIEPOS power supplies function as reliable data sources and make the perfect complement to the existing condition monitoring systems. The following practical example clearly demonstrates the value that these data can add.
Application Analysis with the Help of the Power Supply
A manufacturer of intralogistics solutions planned to replace its existing 24 V power supply with a different decentralized solution. The power supply that was currently in use was constantly causing system shutdowns and it had not been possible to identify the cause.
PULS advised the company about the available solutions and made available a sample of the three-phase 360 W FPT300 power supply. With the support of application specialists from PULS, the customer evaluated the initial data after putting the power supply into operation.
The aim was to investigate three different backfeeding processes:
- The parallel operation of the running motors without braking.
- The parallel operation of running and braking motors.
- The serious case of all the motors stopping abruptly at the same time, for example in the event of an emergency stop.
In all three situations, the output voltage and the current were measured and analysed over a specific period.
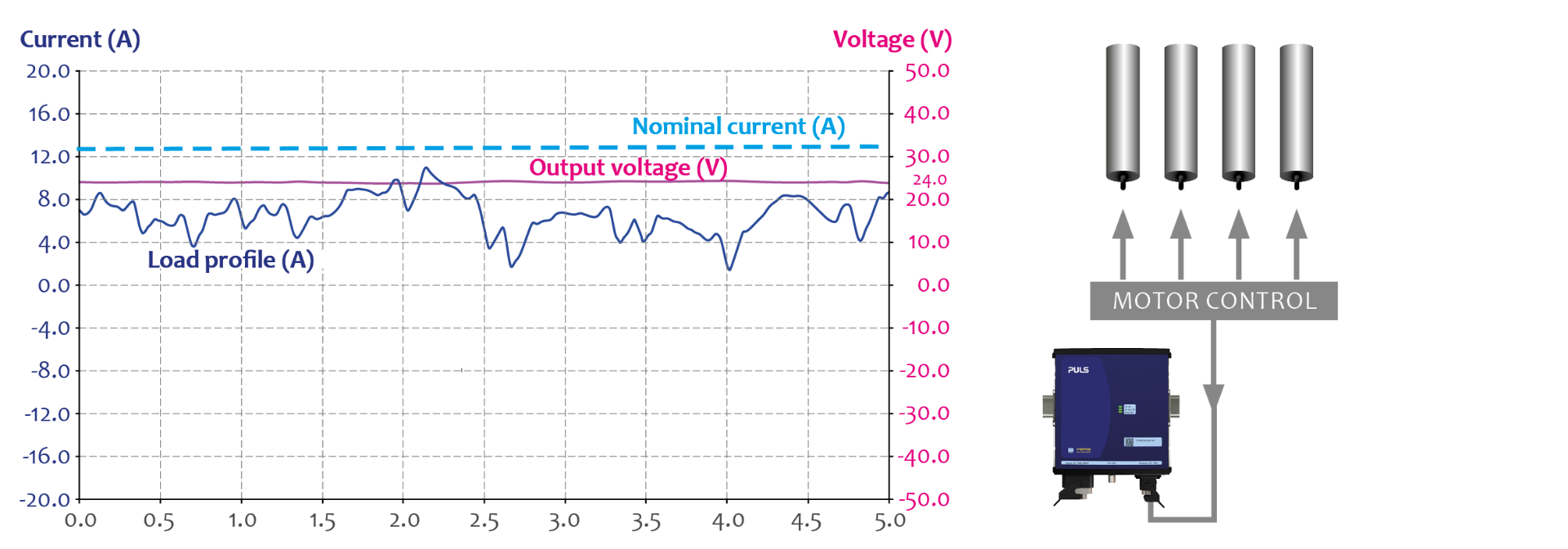
As expected, in situation 1, where the motors were running, there were no noticeable problems (see Figure 1). However, the first load profile for the plant in normal operation was determined, which can help with identifying the correct size of the power supply.
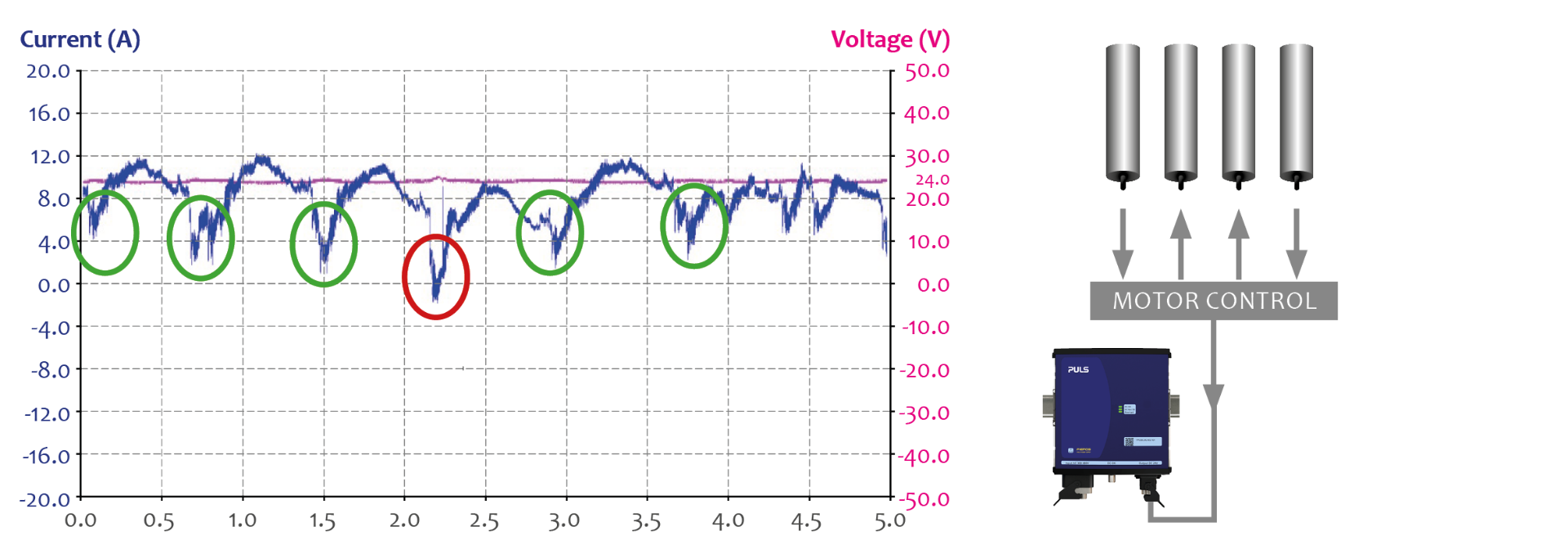
In situation 2, the parallel operation of running and braking motors was analysed. In almost all cases, the energy from the braking motors resulting from backfeeding was directly absorbed by the running motors. Only one brief occurrence of a slightly increased output voltage and a negative current spike was observed, which did not present a problem for the power supplies (see Figure 2, marked in red).
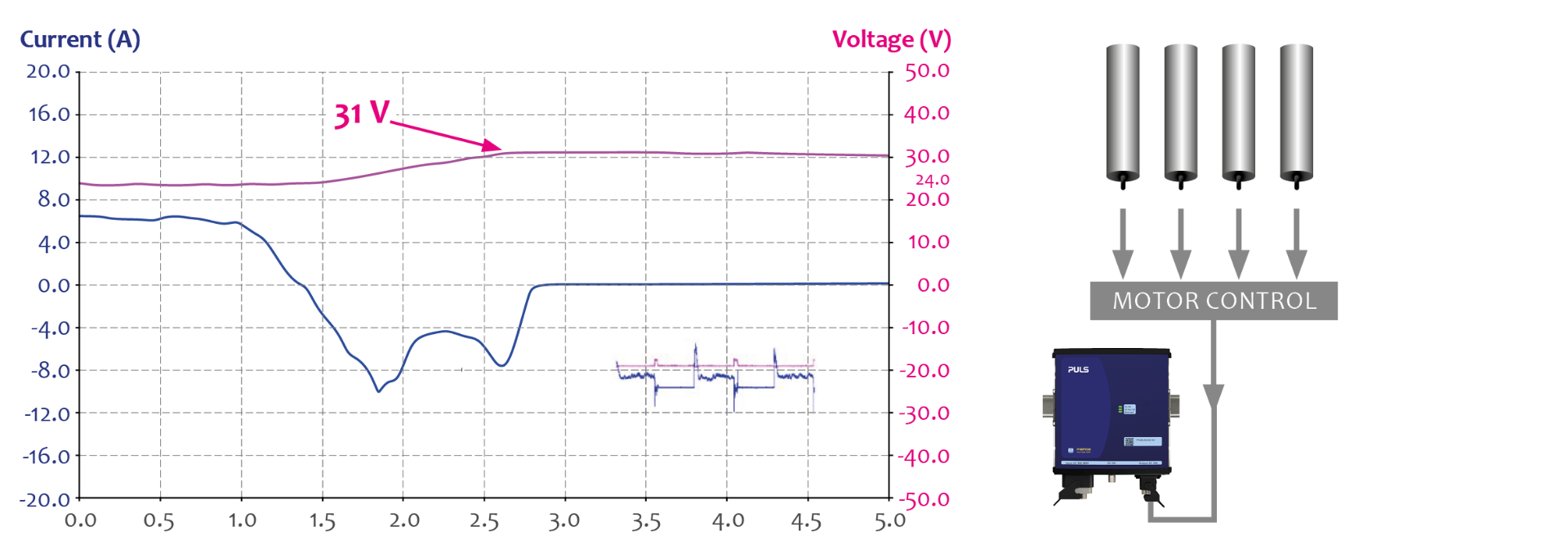
Situation 3 was more critical. All the drum motors stopped simultaneously and caused a rapid drop in current and an increase in voltage to 31 V (see Figure 3).
The data analysis showed that this situation led to the system shutdowns that were mentioned initially. The capacity of the output capacitors in the previous power supplies was not sufficient in this case. As a result, the power supplies shut down.
The FIEPOS power supplies are very electrically robust. The highest permitted output voltage during a backfeeding event is 35 V/4.3 J for the FPT300. The output capacity is 18,000 µF.
As a result, the worst figure of 31 V in this example presented no problem for the power supply. As soon as the voltage fell again, the FIEPOS power supply automatically continued working in normal mode. However, it is worth mentioning here that the motor control centres from different manufacturers shut down for self-protection at a voltage of around 32 V.
The detailed inspection by the technical specialists at PULS before the customer made their purchase decision gave the customer the confidence that they were opting for a reliable, future-proof solution.
Decentralized Solutions for Intralogistics
Alongside its extensive IP20 portfolio, PULS is expanding its range of power supplies in protection classes IP54 and IP65/IP67 for decentralised use outside the cabinet. For system developers that means greater flexibility when planning a plant and more space in the system, together with time and cost savings.
The FIEPOS product family is based on single-phase and three-phase 360 W or 600 W field power supplies. The majority of the systems also function at 200 percent for 5 seconds. This makes them ideal for starting high-current loads and prevents the need for expensive, oversized power supplies. Over the next few months, additional performance classes will be added to the FIEPOS portfolio.
The power supplies are available with a variety of connector configurations, including M12-L/-T/-A, 7/8” and Han Q series. The power supplies from the FIEPOS eFused range have up to four current-limited outputs. These systems allow for selective current distribution, protection and monitoring in the field.
Summary
A reliable and versatile power supply is an essential feature of end-to-end decentralization in intralogistics systems
However, for this goal to become reality, power supply manufacturers must collect as much practical data as possible from the field of intralogistics to be able to offer appropriate solutions. The key is to gather and evaluate real application data.
PULS plays a leading role as an innovator in application analysis on the basis of power supply data. A global team of application engineers advises customers and users on overcoming their technical challenges. The team members can answer questions about complex application situations and identify the best solutions.
The findings from these data are also essential for the development of the decentralized power supply solutions of the future.