Allied Expert Advice: A Checklist for Sensible Motor Maintenance
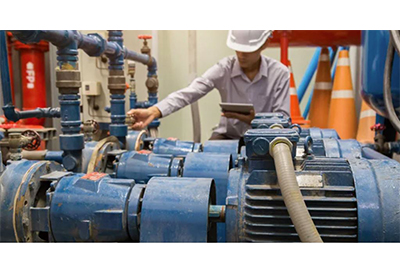
April 6, 2021
Small motors – both AC and DC – serve as critical points in industrial operations. They may be integral to automation and equipment control and serve multiple purposes to mechanically drive and actuate systems and equipment, but are often replaced rather than repaired or reconditioned.
Larger motors may be repaired, rewound, and sent into a motor rewind pool. However, many motors will simply be replaced when imminent signs of failure are detected using smart equipment, instrumentation, and tools discussed below.
“Special features such as custom shaft or mounting with or without a rear shaft can make an impact on repair or replacement decisions,” explains Allen Bennett, a field application engineer with Allied Electronics & Automation.
Bennett adds that a motor’s age is telling of how easy (or difficult) it may be to replace. “Depending on how old the motor is, finding a new exact drop-in replacement could be difficult,” says Bennett. “Older motors have larger housing sizes even within the same frame. This is due to out-of-date insulation materials and lamination stacking methods. Features such as mounting holes, mounting base thickness, and shaft height from base are usually different on old verses new electric motors.
Examining these characteristics prior to buying a new motor will ensure the new motor will work in the application. Advances in insulation materials, lamination materials and bonding methods enable new motors to be smaller. Newer motors are more efficient thereby lowering electricity cost, and this could be a factor in a decision to buy new.”
It’s important to monitor the health of motors and ensure they are reliable and ready to work when needed. There are numerous ways to determine if a motor is in good material condition and running well or is degrading and losing functionality.
A smart way to monitor motor performance throughout a network of equipment is to utilize a motor maintenance checklist. While this list does not incorporate every action to detect premature motor performance, it does represent a sensible list to monitor and detect motor problems and replace them prior to failure and further detrimental effect on your operation.
Here are five areas of focus:
- – Insulation breakdown and resistance. Preventive maintenance includes monitoring the insulation condition of insulated motor windings. Taking scheduled insulation resistance readings, using quality equipment, is a best practice. Such readings should be recorded archived, and all maintenance technicians should be well aware of the limits set forth by industry standards and manufacturer recommendations.
- – Loose connections, cleanliness, and ground detection. Electrical breakdown is often preceded by heat. Heat is a symptom of loose connections and grounds. In addition, dust may be flammable. Therefore, it’s important to have a robust program to check for such conditions. A reliable infrared camera or device can visually indicate conditions of “hot spots” within switchboards as well as wiring, connections, controllers, and power and distribution panels. Infrared “shots” should be taken according to a disciplined schedule. Should any deficiencies be found, they should be repaired and corrected immediately.
- – Misalignment and impending bearing failure. If a roller bearing is failing, has water intrusion, or another journal bearing is beginning to fail, heat and noise may be early warning signs. An infrared camera may also be used to detect heat on motor bearings. Where appropriate, bearing and shaft alignment may be checked with test instrumentation that accurately signal misalignment,
- – Environmental considerations – air gap, water intrusion, physical proximity to motors and their operations. This check is more visual and may easily be incorporated during normal maintenance walkabouts and visual inspections. Notation of any conditions such as water intrusion, close quartered motors without adequate space ventilation, or any climate condition that could adversely impact motor performance are all key.
- – Vibration– within the motor itself, or from the equipment or structure it is mounted to. Is there excess vibration. Excess vibration may be due to numerous factors. How much vibration is too much can be determined by understanding industry standards, manufacturer recommendations, and by taking vibration readings with a reliable tool at a disciplined interval and schedule. Limits should be set and corrective action taken for motor rebuild, repair, or replacement.
While this list is not all inclusive, it is a sensible list to check against your current maintenance program. It also is a sensible approach to ensuring that the health of your motors is acceptable and sound to fortify your uptime and reduce your downtime, due to motor issues.