ABB Breaks New Ground with its ABB Ability™ Digital Powertrain
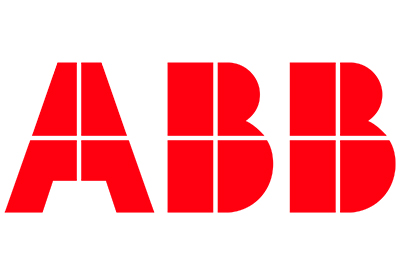
July 3, 2018
ABB Ability™ is about digital transformation. There are already over 200 ABB Ability solutions, including services, software and IoT (Internet of Things) devices, which offer significant advantages for customers, such as increasing process uptime and output with less risks and costs.
“Conventionally, when a drive stops in a steel plant in India, the manager has to phone us and we will send someone out. That takes a couple of days,” said Sönke Kock, Digital Leader in ABB Drives. “Yet, when this happened recently to a drive equipped with ABB Ability™ Remote Assistance services, we received the alarm directly from the drive, and we found within 20 minutes that the drive had overheated because a dust filter was dirty. The dust filter could easily be replaced by plant personnel, avoiding further lost worktime and costs.”
That was possible as the ABB drive was feeding all its information to the cloud and ABB’s experts were able to analyze it immediately. Now, ABB introduces its ABB Ability™ Digital Powertrain – a digital solution that integrates sensor and drive data with cloud-based analytics along a whole chain of industrial equipment used in factory environments – from drives and motors, to pumps and bearings.
An essential element of the ABB Ability™ Digital Powertrain is its monitoring services. Each powertrain, including all its components such as drives, motors, bearings and applications like pumps and compressors, sends measurement data to the cloud, which is then visible to the operator on a simple dashboard. Powertrain assets that are functioning correctly are shown as green; yellow indicates there’s something which needs to be checked, while red means that there is something wrong.
“All your powertrains appear on one screen in a pie-chart showing perhaps that of your, let’s say, 27 powertrains, 20 are green, six are yellow and one is red,” explained Kock. “You can then drill down into the data to get details of the individual powertrains and their components as needed. This is the first kind of IoT-based solution to cover the whole powertrain with such extensive monitoring capabilities.”
“If one of a few hundred bearings breaks on a mine conveyor belt, it may not be noticed until it causes a serious problem,” Kock illustrated. “But the dashboard will show the powertrain as yellow, so that the operator can focus on it and zoom in to its different components until the problem with the single bearing can be identified.” The operator can then contact ABB or arrange for in-house technicians to solve the problem.
The next stage of condition monitoring comes soon as ABB introduces predictive maintenance services in the coming months where components will be analyzed directly under their real operating conditions. This enables them to be serviced or replaced according to precise recommendations based on actual, ongoing levels of stress and wear. After all, the lifetime of a component as given on the box can only be based on average conditions – predictive maintenance will know whether real conditions require earlier or perhaps later action, and may also indicate where conditions may be changed to improve component life.
“Digital Powertrain is another step towards digitalizing the interaction between ABB and its customers,” said Kock. He believes that digitalizing the whole process, from purchase to decommissioning, will reduce cost, waste and delay and so helps achieve ABB’s main aim, which is to provide more benefit and profit for the customer.
For more information HERE