A Smarter Path to Servo Press Optimization
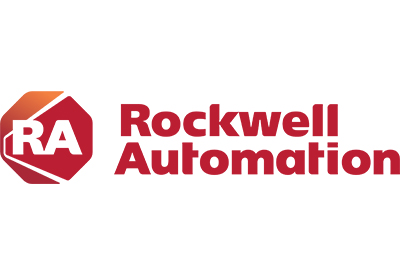
October 19, 2020
I remember when servo presses exploded onto the automotive marketplace more than a decade ago. The advent of the servo-driven press overlapped with the need to improve capital efficiency, manufacturing flexibility and quality to meet the requirements of newer multi-model, multi-platform vehicle production facilities – and the associated demands placed on Tier suppliers.
By replacing traditional flywheel-clutch mechanical systems with servo-driven designs, machine builders redefined press shop flexibility and performance.
Fast forward to today. Flexible manufacturing and multi-model vehicle production is the norm and the need for even more agility is accelerating to address lightweight metals, other new composites, product geometries and regular adjustments to production build schedules that require just-in-time and just-in-sequence deliveries.
If you’re a manufacturer of pressed parts or a servo press OEM, will you be able to keep up? That often depends on control system functionality – and just as important, design philosophy.
The Beauty of Configurable Control
Before servo presses hit the marketplace, the motion of any machine’s ram was a function of the constant speed of the motor during the stroke cycle. Servo technology makes ram motion profiles configurable throughout the stroke to better meet the forming requirements of material and part geometry. In other words, you can independently control the velocity, acceleration and position of the ram at any point in the process.
Your ability to control motion profiles digitally that align with the requirements of complex parts and specialized modern materials can improve the performance, precision and “first time through” quality of your press.
Servo technology also improves agility by replacing many arduous adjustments that are intrinsic to mechanical press changeover. Aside from changing out the die, modifications are completed digitally using a recipe-driven, operator interface – or can be directly received from an MES scheduling system.
How Open Design Expands Possibilities
But just how easily will you be able to support your servo press as new needs arise?
Achieving ongoing flexibility is challenging with some control systems that provide a limited number of motion profiles and are based on proprietary, “black box” technology. Since the application code is “locked,” adjustments typically require support from the control system supplier – adding time and cost.
Recently, we developed a smart servo press solution based on an open, configurable design concept as a cost-effective alternative to an existing system. Derived from off-the-shelf control system components and technology, the solution puts you in charge – and enables you to configure an infinite number of motion profiles, restricted only by processor memory.
More Motor Choices. Better Customization.
As valuable as it is to have an open and configurable design, it is equally important to apply a motor matched to the mechanics of your servo press design to maximize performance. But some servo press control systems are rigid not only in their configurability, but also in available motor options. You may find that your only choice is a motor that is larger than required or not optimized for the application – adding cost, affecting performance and reducing the energy efficiency of your machine.
A smarter servo press approach? Choose a control solution built to accommodate multiple motor types – from multiple motor suppliers.
With a wide range of motor options at your disposal, you can much more easily tailor a press to the exact torque, speed and other characteristics your applications require.
Unifying Control Beyond the Press
A smart servo press solution uses a single control platform for logic, motion and safety control, which speeds machine design. An integrated platform also gives workers better visibility to all machine events – including safety.
When it comes to safety functionality, a smart servo press solution can extend beyond the press itself to include front-of-line and end-of-line tooling, such as stackers, destackers, decoilers, and loading and unloading automation. This equipment can be integrated into the same controller running the press in smaller applications – or interlocked and synchronized with the press controller over EtherNet/IP. So the tooling at the front or end of the line can leverage the same advanced safety motion commands and profiles in the press controller project.
The result? A single, unified solution that helps protect workers – and is easier to operate and maintain.
The Power of Continual Optimization
Your servo press has the ability to operate for decades in an automotive manufacturing environment. A smart servo press platform is built to optimize performance now – and throughout your machine’s extensive lifecycle.
For example, a smart servo press can leverage the capabilities of smart devices, such as variable-frequency drives that include predictive maintenance capabilities. Or integrate condition monitoring to improve asset utilization and performance.
A smart servo press is also built to take advantage of advanced analytics platforms and machine learning – to quickly identify performance deviations and enable continuous improvement. Smart servo press OEMs are also discovering ways to ease maintenance and training with augmented reality (AR) and other advanced digital technologies.
How to differentiate and add digital value to your machine or process is limited only by your imagination.