7 Good Reasons For Ethernet-APL by Pepperl+Fuchs
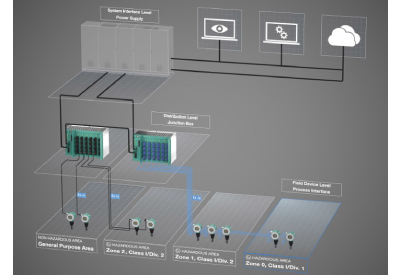
May 26, 2022
As development progresses and the benefits for the process industry become clearer, interest in and demand for the Ethernet Advanced Physical Layer, or Ethernet-APL for short, are growing. The debate about this innovative technology is becoming increasingly intense, so that more and more users from all over the world are approaching our experts with questions. You will find the most important answers here–and thus seven good reasons why this technology should not be missing in your plant.
1. Which DCS Manufacturers already Offer Control Systems with Ethernet-APL Today?
In fact, all of them, without exception, already offer Ethernet-APL. With the FieldConnex® rail field switch from Pepperl+Fuchs, the connection right into the field of the plant and thus the continuous communication can be easily realized–up to the selection of different protocols.
2. Which Field Device Manufacturers already Provide Ethernet-APL-capable Field Devices?
The first manufacturer to immediately announce complete instrumentation with Ethernet-APL for spring 2022 is Endress+Hauser, and others will follow. However, by the time of ACHEMA at the end of August 2022 at the latest, it can be assumed that this topic will cause a lot of movement among manufacturers.
3. What Benefits Will Customers Receive if They Deploy Ethernet-APL, Especially Comparing to 4-20 mA and HART?
This is the key question: universal, barrier-free network access to instrumentation at high speed! All the advantages we know from everyday life with Ethernet can be transferred to the requirements of the process industry:
- •better SOPs
- •less maintenance
- •reduced risk of failure and malfunction
- •higher output
- •more efficiency
4. From Which Features Do These Benefits Derive?
A field network, in conjunction with PROFINET or Ethernet/IP and appropriate hardware and software, enables applications with fully automated processes interacting with field instruments. Specifically, this means, for example, that systems can provide the following functions and applications:
- •automatic device detection
- •automatic upload and download of the instrument configuration
- •upload of the right DTM / EDD device drivers
5. Are there Demo Devices? How Can I Experience the Technology Live?
The experts from Pepperl+Fuchs will not be able to demonstrate the technology to you in a demo case as usual. The easiest way to implement a test configuration with Ethernet-APL is in your own environment with your control system or controller that you keep on hand for testing. From Pepperl+Fuchs you get a switch and the expert support. You request the field devices from your usual suppliers. You can then start testing immediately with a PROFINET controller and PROFIBUS PA field devices. Before you do this, however, you should set yourself goals for how the functions of a network infrastructure can make your daily work easier and develop test scenarios from them. The NAMUR epics, which describe various use cases, also provide inspiration for this.
7. What Is the NAMUR Open Architecture and How Does Ethernet-APL Fit in?
NOA or the NAMUR Open Architecture defines a lateral access to secondary information of the field instrumentation, such as configuration, alarms and diagnostics. Lateral means access independent of the control system and in parallel, so that the control system can remain unaffected and highly available in its configuration and thus process control
NOA defines appropriate application scenarios for handling the instrumentation, such as
- •the simple commissioning of the field devices
- •automatic alignment of the plant documentation
- •the simple exchange of instruments or
- •the ability to read out several variables from one device.
For this purpose, NAMUR defines OPC-UA as the preferred protocol, which is transmitted in parallel to the industrial protocol for plant control. Ethernet-APL is the data transmission link and physics that enables this parallel communication directly to the field device.
Do you have further questions? Please contact the experts at Pepperl+Fuchs and let them know how they can support you.