5 Business Cases for Using AC Drives with Integrated Safety
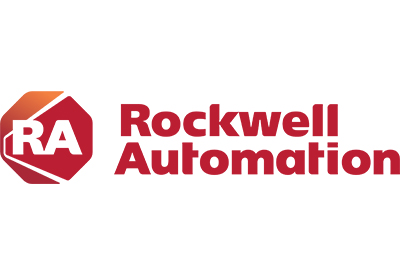
May 27, 2019
If you still only view safety as a matter of compliance, you’re missing the bigger picture in the era of smart manufacturing.
Smart, networked safety can deliver measurable business benefits. And it can push the boundaries of what’s possible in your operations.
Low-voltage AC drives with integrated safety are a perfect example of what networked safety can do for you. When connected to a safety PLC over Ethernet, they can give you more insights into your operations, reduce system wiring and components, and add precious minutes back to production. And yes, they can also help you be compliant – and maybe even reduce safety risks.
To put these benefits in the context of the bottom line, here are five business cases for using AC drives with integrated safety:
1. Increased Productivity: Lockout/tagout (LOTO) has long been a core element of industrial safety. But it can also constrain productivity.
AC drives with integrated safety allow you to use safety functions in place of LOTO procedures in certain instances. Safety functions – like safe limited speed, safe torque off and safe brake control – can help workers service equipment in a fraction of the time and still be compliant.
Consider a task like cleaning augers and rotating drums. Using LOTO procedures, workers must continually start and stop the assets to clean them. Safety functions like safe limited speed and safe direction allow workers to clean the equipment while it rotates at a slow speed.
2. Enhanced Safety: Workers sometimes bypass LOTO procedures to stay productive. And that creates serious safety risks. AC drives with safety functions that allow workers to more quickly service machines can reduce incentives for bypassing safety procedures.
Also, safety functions can support passive safety systems to reduce risks for new workers. Passive safety systems perform functions with little or no worker effort required. This can help mitigate the risks of inexperience, such as workers placing their hands in hazardous areas.
3. Reduced Complexity: Traditional safety products are hardwired separately from a standard controller and can require extra hardware like safety relays. A networked safety product like an AC drive with integrated safety can share the same Ethernet network as a standard controller and reduce the need for added hardware. This can simplify your system and reduce its costs.
Networked safety and control products can also be programmed, configured and maintained in one software environment, further reducing complexity.
4. Better Insights: An AC drive with integrated safety can give you access to rich analytics to help you improve your performance.
For example, you can track the time, location, frequency and duration of when the drive’s safety functions are being used. This can help you better track safety-related downtime and identify changes to improve uptime. Drive diagnostics can also help you see where safety-related failures occur to speed up troubleshooting and recovery.
5. Greater Flexibility: An AC drive with integrated safety can grow and change with your business.
For example, you can use the advanced safety functions later if they’re not needed today. The drive delivers integrated safety through a card that you can add at any time.
You can also easily change the drive’s safety applications as your requirements evolve over time. A hardwired safety solution can require complex planning and rewiring to meet new safety requirements. But a networked solution only requires updating code in your safety PLC.
Safety as a Business Enabler
Networked safety products offer more than compliance – they can help you maximize the performance of your business. Especially today, if you want to digitize your operations to be more competitive, networked safety products can help make you more intelligent, more connected and more productive.
Learn more about low-voltage AC drives with integrated safety here.
For more information, vists HERE.