4 Reasons to Upgrade to Modern Motor Systems
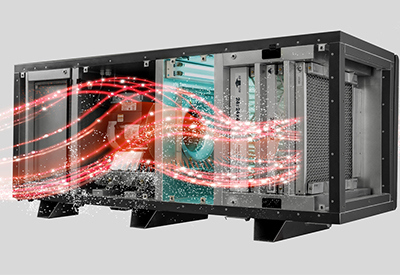
September 13, 2021
Although modern motor technologies offer significant potential energy savings to business owners, the majority of motors currently in use are outdated and inefficient. In fact, a recent survey of the US market found that over 60% of industrial motors are over a decade old. Here are four reasons why it’s worth updating to more modern motor systems such as magnet-assisted synchronous reluctance motors and variable speed drives.
Cut energy costs now
By implementing new technologies and industry best-practices, energy efficiency can be improved by up to 30%.
Globally, electric motors account for almost 70% of electricity used in industrial applications. And 45% of the world’s electricity is used to power electric motors in buildings and industrial processes, including data centers, steel factories, food processing plants, and packaging centers. Unfortunately, most of the electric motors installed in these facilities are outdated and inefficient. This means that most businesses which rely on motors could cut their energy costs now, simply by modernizing their motors systems.
By implementing new technologies and industry best-practices, energy efficiency can be improved by up to 30%.
Only pay for the energy you need
When added to an existing motor of a pump, fan or compressor, a variable speed drive can typically reduce power consumption by 25%.
About 70% of industrial motors are used to power fans, pumps and compressors. Most of these operate at partial load, with the motor running at full speed while the speed or flow of the application is controlled mechanically using brakes, throttles or valves. In contrast, using a variable speed drive to control motor speed and torque directly, prevents energy being wasted by mechanical speed or flow control. This means that the motor system will only use the amount of electricity that is actually needed, when it’s needed, and no more.
Ensure future compliance
Upgrading to the most efficient motor technology available will help ensure future compliance.
Regulations are in place to help drive industry to update the installed base, however, these regulations typically specify the minimum acceptable energy efficiency standards. In fact, the latest available motor technology is already significantly more efficient than regulations require. For example, in the US, NEMA actively supports adoption of Premium efficiency motors (equivalent to IE3) to improve efficiency throughout the market. However, ABB’s EC Titanium technology delivers ultra-premium efficiency (equivalent to IE5), which is considerably more efficient than the minimum requirements, and it delivers 40% lower losses than Premium efficiency motors.
Since energy efficiency regulations are likely to get tighter over the upcoming years, it makes sense to upgrade motors to more than the minimum standards in advance. This will enable easier compliance, as well as bringing clear energy and cost savings.
The conversation about energy efficiency is changing. New technologies enable us to save more energy than ever before, explains Jesse Henson, President of ABB’s NEMA Motor Division.
Benefit from overall life time savings
Upgrading technology now will pay back in savings for the rest of the application life cycle.
Although many older motors are still in good working order, they are built to meet older, outdated efficiency standards. This means that the whole system is running at a lower than optimum efficiency level, which will continue to add unnecessary costs throughout the lifetime of the application. As a result, it is well worthwhile updating a working motor to improve system efficiency before the end of its working life. The long-term savings far outweigh the initial costs and, in fact, the initial investment can often be paid back in as little as one to three years.