4 Key Factors to Consider When Sizing Servo Motors
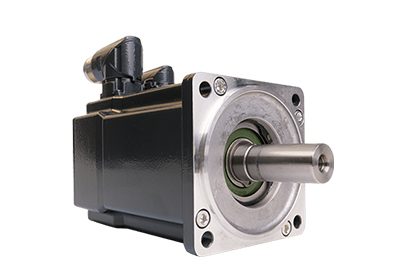
April 30, 2020
By Jeff Kardell
The ability to size servo motors correctly is imperative for motion-controlled applications, and it can be much more involved than sizing AC induction motors. Acceleration, deceleration, and running torque must still be taken into account, but the servo’s ability to dynamically control the load’s speed and position is also important. During acceleration and deceleration, peak and nominal running torque measurements must be calculated to ensure that the servo motor does not overheat during use. In addition, inertia matching between the motor and load is necessary to ensure optimum response and system performance.
In this post, we will be examining these keys factors, as well as how KEB can provide a solution to your motion control needs. Four key servo selection factors I will be detailing are:
While there are other factors to keep in mind for your application, these four are most critical when accurately sizing servomotors.
Inertia Matching
Inertia matching refers to the system inertia. Specifically, the ratio between the inertia of the load and the motor. This formula definition is below:
The moment of inertia is a measurement of how difficult it is to change the rotating velocity of that object or system. The JM (inertia of motor/rotor) should be supplied by the motor manufacturer. KEB’s servo motor data are found on the KEB Drive software, which is a program that aids in choosing motors and gearboxes. JL (load inertia) consists of all components in the system moved by the motor. This ratio between the motor and load is important when selecting servomotors, but the following must be considered:
- – Performance of the motor improves as the inertia ratio decreases
- – Control loop tuning and machine performance improves as the inertia ratio decreases
- – A motor with too low of an inertia ratio will be more expensive and have little to no performance improvement
- – System inertia ratios should be designed for a max of 10:1 but are typically 5:1 for ideal performance
When choosing and calculating an inertia ratio, find the smallest motor that has the ability to provide the speed and torque necessary for your application. If you are finding it difficult to obtain a ratio that works, keep in mind that KEB has the ability to add additional motor inertia. Also consider that many motor manufacturers offer different servo series with different inertias. For example, there might be a product line with a “low inertia” and another with a “medium inertia”.
Speed and Torque Profile
Speed and torque profiles are additional critical elements in choosing a servo motor. While the motors capability is described by the speed-torque curve (see below), the application requirements are best illustrated using the speed and torque profile. Depending on the application, there are different speed and torque requirements that the motor will need to meet.
Below is a graphical representation of a linear application with a servomotor. The speed profile is a graphical representation of acceleration, constant speed, and deceleration as the payload reaches its destination. As you can see by the torque profile, the maximum amounts of torque occur during acceleration. When the machine starts, the motor must overcome the mechanical friction while accelerating the load from rest. Once acceleration is complete, a nominal torque is output by the motor to maintain speed and overcome the friction. The decelerating point in the profile is still associated with high torque, but the friction also aids in stopping the load.
It is important to ensure that the motor can produce the required maximum torque at the application speed. This ideally falls within the intermittent region of the motors speed-torque curve, so it is not oversized.
RMS Torque
RMS torque is the time-weighted average of the torque during a complete machine cycle (steady state). In order to size your motor correctly and prevent overheating, this RMS torque will need to fall within the continuous region of the speed-torque curve. For example, a servomotor with 4 N·m of RMS torque will experience the same heat rise if it produced 4 N·m of constant torque. Therefore, as long as 4 N·m is in the continuous region of your speed-torque profile, the motor will not overheat.
Speed-Torque Curves
Motor speed-torque curves are essential when selecting and sizing servos. In order to prevent the motor from overheating during use, ensure that the motor has the specific capabilities required for your application. These curves ensure that the required torques and speeds, whether continuous or intermittent, can be produced with the servo motor you choose. By examining the speed and torque profiles and computing the RMS torque, you can now look towards speed-torque curves of specific motors and see if they will fit your application.
Let us look at the image below to provide additional insight on speed-torque curves. This is an image from our KEB Drive software, which will be sure to help you when you are deciding if your servomotor is a valid choice for your application. This specific image is for our TA3S servomotor.
In the image, the blue lines represent the maximum speed/torque based on various input voltages. For this example, we will look at only one input voltage curve, 460 VAC (6). The region below the S1 line up until line 6 indicates the continuous running region. In this region, the servomotor is capable of running at the corresponding speed and torque values without overheating. Above the S1 line (1) lies the intermittent operation region. In this region, the servomotor can operate for a small amount of time based on the overall RMS torque of the system.
With the input voltage of 460 VAC, the TA3S can reach full peak torque (8.7 N·m) at speeds up to 2750 rpm. This is assuming no losses in the drive and that the full 460V is available. If the inverter were to have an input reactor on the input, there would be a slight voltage drop at the input to the drive, which would shift the blue curve to the left.
As the speed increases, the available torque starts to drop. If you determine application needs of 4 N·m of torque at 3500 rpm, using 460 VAC would allow you to reach this torque level on an intermittent basis. However, with a 400 VAC input, you would not have sufficient voltage to reach this speed and torque.
For continuous operation (rated torque), the required voltage difference is less, so we can reach higher speeds before we enter the field weakening range. With a 460 VAC input, we can achieve continuous rated torque (S1) out to about 4200 rpm.
An important point to remember when using speed-torque curves is to check the input voltage the motor will be operating at and ensure that the motor will run successfully in either the continuous or the intermittent regions.
Conclusion
In conclusion, while sizing servo motors can be challenging, these four key factors are imperative to making a choice that will fit your application. If interested, you can download KEB-Drive from one of the gearmotor product pages. This software includes servo motor information for the TA servo motors. It also includes information to add inline and right angle gearing.