3 ways that integrated safety minimizes the impact of production line disruptions
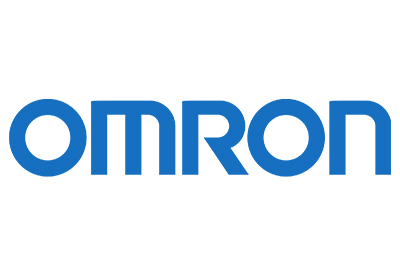
June 18, 2019
Safety used to be treated somewhat as an afterthought, in that it was added as a separate system once all the other production equipment was in place. Nowadays, many manufacturers are seeing the benefits of integrated safety systems, in which safety features are designed into equipment from the very beginning.
A good safety system protects employees, works-in-progress and equipment from the effects of malfunctions while also ensuring that the line can be restarted as quickly as possible to avoid excessive downtime. Integrated safety fulfills all of these requirements with its intelligent use of data.
1. Integrated safety systems take into account the specific functionality of production machinery.
In order to address hazards as efficiently as possible, it’s important for the safety system to thoroughly “understand” the workings of the production machinery. In an integrated system, control software closely monitors each line component in real time.
Since every aspect of the equipment’s operation is accounted for, the system can respond more intelligently to problems. Instead of issuing sweeping measures like an emergency stop, integrated safety can minimize the impact of a disruption by focusing on specific machine functionality.
Omron’s Sysmac platform helps bring safety and production elements together in an intelligent and flexible way to maintain optimum performance even while operations are temporarily disrupted. Depending on the issue, production might be able to remain in a standby condition rather than suffering a complete emergency stop.
2. Integrated safety systems use comprehensive data to get to the root of problems faster.
Machines designed with integrated safety have access to the necessary data to thoroughly evaluate any issue and take measures to keep it from happening again. In a complex production line, it could be extremely difficult to track down the source of the problem without integrated safety.
When the safety system has access to machine data, maintenance personnel will be able to take advantage of all the information they need even before they go out to the line. By knowing ahead of time which tools might be needed and which safety precautions to take, they’ll be able to fix the problems much more quickly and with less risk.
3. Integrated safety systems improve recordkeeping.
For accurate maintenance scheduling in a non-integrated system, operators have to keep a reliable and accurate log of incidents and operations. Many older systems use cumbersome manual systems that exacerbate uncertainty and make it difficult to send information where it’s needed to ensure safe machine operation and to schedule predictive maintenance.
An integrated system is much more sophisticated. All signals and inputs are merged within an intelligent controller that replaces discrete safety relays with advanced logic, removing the uncertainty caused by manual data records. Important information is automatically recorded locally and can also be made available online.
By digitally capturing every event, integrated systems make it easy to check statistics such as the mean time between failures (MTBF) and use them to schedule preventive maintenance. Knowing when to carry out maintenance is a critical factor in reducing the occurrence of equipment breakdown and maintaining high levels of overall equipment effectiveness (OEE).
In addition to providing comprehensive, integrated safety solutions, Omron supports manufacturers with a wide variety of safety services to ensure that production lines meet regulations and that equipment operators have a full understanding of safeguarding measures. Omron’s safety services help maximize uptime while meeting requirements for flexibility.
Contact us( “Hero :: Forms :: Solutions :: Safety”) today to find out how Omron’s integrated safety solutions can improve your application!