Tri Tech Automation Increases Uptime and Lowers Maintenance Costs for Customers
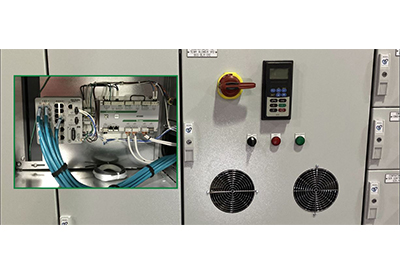
January 20, 2021
SITUATION
With its commitment to lowering their customers’ cost of ownership, Tri Tech Automation (Tri Tech), a developer of automated control systems, sought to reduce customer maintenance costs on their motor control centers (MCCs) installed at customers’ oil and gas pump stations. In addition, Tri Tech management wanted to promote their MCCs as having advanced safety features and advanced diagnostics to protect personnel and equipment.
Tri Tech wanted to offer customers a method to diagnose maintenance problems remotely. That would enable a service technician to bring the necessary replacement parts on a service call and save delays related to parts procurement. Service technicians need between four to six hours just to get to remote pipeline locations. Without any advance information on the nature of the problem, the technicians need as much as a day to identify the problem and order replacement parts if needed. In addition, service technicians could be subject to electrical hazards such as an arc flash when working around the energized electrical equipment.
Tri Tech also wanted to ensure that their service technicians would be protected from an arc-flash event when working on an MCC. The potential arc-flash incident energy at an MCC associated with a large pump could exceed 40 cal/cm2, which can be life threatening in the event of an arc-flash incident and also could cause destruction of the MCC. Service technicians needed an extensive set of personnel protective equipment (PPE) to safely work on an MCC in which the potential for a high-energy arc flash could exist. Having to use all that PPE adds to maintenance costs.
A SAFETY CULTURE
Tri Tech determined that they needed updated arc-flash protection equipment and considered possible solutions from the major suppliers of electrical power equipment. Their equipment either lacked features or provided unnecessary extra features which resulted in an unacceptably high purchase price. Some arc-flash protection devices did not have remote communication capabilities. Some required use of a large number of sensors, driving up cost.
Because Tri Tech had used the Littelfuse AF0100 ArcFlash Relay in other applications, their engineers contacted Littelfuse for advice. Littelfuse engineers analyzed the requirements and recommended the AF0500 Arc-Flash Relay. Littelfuse provided product demonstrations, the required technical information, and technical support during product evaluation. The AF0500 had the exact capabilities that Tri Tech needed:
- – Remote communication via Ethernet using the Modbus TCP communication protocol enabling interfacing with a programmable logic controller (PLC)
- – 360-degree arc-flash monitoring along the MCC power bus, using the PGA-LS20 Fiber Optic Sensor
- – Arc-flash sensing using two PGA LS10 Point Sensors in areas where maintenance activities with energized equipment are most likely to occur
- – Detection of an arc flash and activation of a trip signal in under 1ms
The AF0500 Arc-Flash Relay has the fastest response time in the industry. Arc-flash incident energy levels are, in part, related to the amount of time that the fault is present until the main breaker in the MCC opens. The AF0500 decreases the total time between detection and opening of the MCC main breaker, thereby lowering the arc-flash incident energy. Lower arc-flash incident energy levels lead to a reduction in the amount of PPE that service technicians need to safely work around energized electrical equipment. Wearing less PPE saves time and lowers maintenance costs.
OUTCOME
Tri Tech selected the AF0500 Arc-Flash Relay to improve MCC safety and to reduce maintenance costs. The AF0500 provided sufficient sensing and the fastest detection time to monitor the sources of potential arc flash in an MCC panel for protection of both personnel and the MCC panel.
Tri Tech can get logged event history remotely from the AF0500 through its Ethernet link to the local PLC. Knowing that a relay has tripped is valuable information that supervisors can tell field service technicians prior to traveling to a remote site. Service technicians can now reduce the total time to restore an MCC to operation in as little as one day. This is, much faster than what previously could take weeks. Now, Tri Tech can save its oil and gas customers significant maintenance costs and increase MCC uptime.
Tri Tech will use their new MCC panel to grow their business by targeting power generation companies and chemical manufacturing facilities as well as oil and gas production and distribution companies. TriTech has learned that, with the AF0500, the company can build an MCC in half the time and at a lower price than competitors.
“The Littelfuse AF0500 Arc-Flash Relay upgrades the safety of our motor control centers and enables us to maximize uptime and reduce maintenance costs for customers. The AF0500 has just the capabilities that we needed. We feel that the AF0500 makes our motor control centers extremely valuable for the power generation and process control industries,” says Craig Leonard, Vice President of Operations.
With Littelfuse leadership in arc-flash detection, Tri Tech can safely and efficiently serve its customers while maximizing MCC uptime and lowering the cost of ownership.