Rockwell Automation Helps Simplify Integrating Safety into Machines
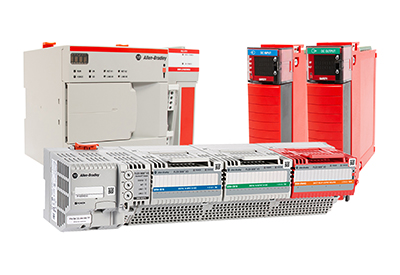
July 11, 2019
Machine designers are required to design safety into more industrial systems than ever. To help them design more easily and meet their other application requirements, Rockwell Automation has seven new safety modules across three I/O platforms. This offers designers both local and distributed safety I/O options and a wide range of performance and connectivity attributes to help improve compliance and machine performance.
“Our expanded safety I/O portfolio gives designers more options to meet their safety needs,” said Steven Goh, vice president and general manager, Asia Pacific Business Center, Rockwell Automation. “Safety options are selectable for any Allen-Bradley I/O module. The new modules also incorporate faster safety reaction times, greater diagnostics and enhanced communications to create more competitive machines.”
The new safety modules also help simplify the design process. For example, they have a largely common data structure and graphic user interface. This programming and operation can help reduce design time, allow for code reuse and shorten the learning curve for designers.
The new safety I/O modules include:
- The Allen-Bradley Compact 5000 safety I/O modules provide local and distributed safety I/O for the Compact GuardLogix 5380 safety controller and distributed safety I/O for the GuardLogix 5580 safety controller. The modules offer faster safety reaction times to help designers lower their costs and create smaller and simpler machines. They also provide additional diagnostics to help users more easily identify faults.
- The Allen-Bradley ControlLogix CIP Safety I/O modules provide local safety I/O for the GuardLogix 5580 controllers in larger applications that require a high-density I/O solution. Using these in-chassis modules simplifies configuration and reduces panel space by eliminating the need for an adapter. These modules can also be used for distributed safety I/O.
- The Allen-Bradley FLEX 5000 safety I/O modules are ideal for applications that require fixed field-wiring terminations and both vertical or horizontal mounting. The distributed I/O modules can operate in extreme environments and be used directly connected to copper and fiber networks. They also support a range of network topologies, including a redundant star network via Parallel Redundancy Protocol, and enhance communications with 1-gigabit EtherNet/IP connectivity. The FLEX 5000 platform provides distributed safety I/O for the Compact GuardLogix 5380 and GuardLogix 5580 controllers.
Each of the seven new safety I/O modules is TÜV certified for use in safety applications up to SIL 3 and PLe, Cat. 4. For added protection against environmental stresses, all modules are selectable with conformal coating options.
Find out more HERE.