Make Short Production Runs More Efficient with Motion Systems from Rockwell Automation
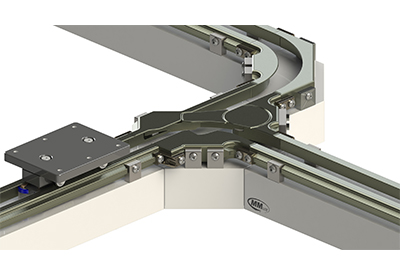
August 12, 2019
Manufacturers are customizing products to meet more targeted consumer demands. As a result, they must contend with shorter production runs and more frequent changeovers, which takes time away from producing products. The MagneMover LITE system is helping make these higher-SKU operations efficient by moving payloads faster in a more flexible way than traditional conveyors do today.
Now, Rockwell Automation has updated the MagneMover LITE system that rapidly moves products in carts along a motorized track. The flexible system can now move heavier products and support larger-scale applications. It also reduces downtime because it allows for changeovers with the push of a button and no mechanical intervention.
Heavier Products:
New wheeled cart options give users five-times greater carrying capacity than sliding carts. The single- and tandem-wheeled carts can carry payloads of up to 2.5 kg (5.5 pounds) and 10 kg (22 pounds), respectively. This allows producers to scale up from one product size to another without the need for multiple machines to produce and package their product varieties.
Larger Scale Applications:
Using Ethernet-enabled motors and Ethernet-based node controllers to replace serial communications allows users in high-volume industries to improve layout flexibility and run hundreds of carts per path while requiring fewer node controllers. The MagneMover LITE system is ideal for larger applications using long paths with high switch and cart densities.
“Machine builders and manufacturers that have seen how this technology can reimagine manufacturing, assembly and packaging operations have been eager to do more with it,” said Neil Bentley, director of product line management, Rockwell Automation. “That’s why we enhanced the MagneMover LITE system. It supports bigger payloads. It delivers even better performance. And it can scale applications up to previously unseen sizes.”