Yokogawa Releases SensPlus Note, an OpreX Operation and Maintenance Improvement Solution for the Digitization of Field Data Using Mobile Devices
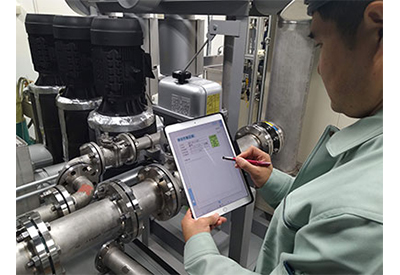
November 29, 2019
Yokogawa Electric Corporation and MetaMoJi Corporation announce that they have jointly developed SensPlus Note, a low cost and easy to implement solution for the digitization of plant data on mobile devices. SensPlus Note, a solution in Yokogawa’s OpreX Operation and Maintenance Improvement family, improves the efficiency and quality of maintenance work and the precision of post-maintenance analyses by enabling data from plant field work to be used more efficiently. This solution will be released in all markets worldwide on January 31.
Development Background
A wide variety of equipment and devices from different manufacturers are used in plants. Each has a specific set of maintenance procedures and check items, and this work is performed as set out in manuals, check lists, and other documentation. While it would improve efficiency and help to ensure that this work is done correctly if field maintenance data could be shared and analyzed in real time, this is not possible in plants where such data is written down on paper documents. To address this need, Yokogawa and MetaMoJi have jointly developed the SensPlus Note solution for the digitization of field maintenance data on mobile devices. This solution draws on Yokogawa’s plant operations know-how and MetaMoJi’s proven expertise in developing business applications for mobile devices.
Features
The SensPlus Note solution consists of a data input application and a cloud platform. Data input using this application is digitized and uploaded to a cloud server, where it can be analyzed using other software. The mobile application is based on MetaMoJi’s GEMBA Note, which is an advanced digital notebook that was developed to support maintenance at construction and manufacturing sites.
1. Digitization and real-time sharing of information, with intuitive operation
With the SensPlus Note solution, text input using a pen or keyboard, videos, still images, and audio recordings can all be easily entered on the same form and linked to a device management ledger. This saves time and provides all the information in one place that is needed to know precisely what is happening in the field. Once such information is input into GEMBA Note, it can be shared with other personnel, drastically speeding up loop checks* and other tasks that require multiple operators to coordinate their efforts.
2. Ability to install additional server applications for statistical analysis and other operations
With SensPlus Note, data is uploaded to a cloud server, where it can be viewed and managed using a web portal. With its ability to store data collected over long periods of time, this platform is ideal for both preventive and predictive maintenance. Applications for the statistical analysis of field and plant operational data and other operations can be added to the platform as needed to assist in identifying failure causes and improving work procedures.
Yokogawa will continue in its efforts to expand the lineup of applications that can be used with the SensPlus Note solution.
Major Target Markets
Manufacturers
Applications
Communication between central control rooms and plant personnel, and between personnel at different plants
Communication between field personnel and third parties, such as the help desk of a plant equipment manufacturer
The analysis of stored data to improve maintenance and manufacturing operations