Schneider Electric Partners with Delta Systems & Automation to Improve Efficiency and Productivity with EcoStruxure Augmented Operator Advisor
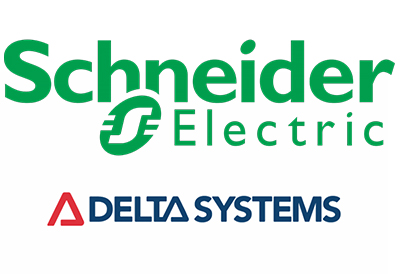
April 30, 2019
Schneider Electric has announced it is partnering with Delta Systems and Automation, a packaging and machinery company, to integrate EcoStruxure™ Augmented Operator Advisor to better manage their Flow Wrapper machines. As part of the partnership, Delta Systems will also leverage Schneider Electric’s P4 3-Axis Delta Robot to improve performance and simplify operations.
Delta Systems, part of the IMA Group, specializes in feed systems and horizontal flow wrapping. Prior to transitioning to Schneider Electric’s PacDrive-3 control architecture, Delta Systems used their own proprietary control system on their machines, which generated both diagnostics and status reporting. However, they were also seeking sensory inputs and material flow to increase operational efficiency, reduce costs and improve proactive maintenance. EcoStruxure Augmented Operators solved these needs with added benefits to increase performance of the system and speed maintenance time.
“EcoStruxure Augmented Operator Advisor helps us quickly diagnose problems within our flow wrapper machines, allowing us to predict and execute preventive maintenance schedules, improve machine availability, and reduce costs,” said Brian Kyles, Technical Director Delta Systems and Automation. “As part of the largest supplier of turn-key packaging systems globally, we selected Schneider Electric due to its expertise, innovative technology and customer-centric approach.”
The Augmented Operator Advisor software combines contextual and local dynamic information through an intuitive tablet interface that feeds real-time data and virtual objects, giving operators immediate access to relevant machine and process information. Additional benefits of Augmented Operator Advisor include:
• Reduced downtime. Operators can virtually open electrical cabinet doors to troubleshoot potential issues with machine components without shutting down operations.
• Faster operation and maintenance. Operators can quickly find information, with immediate access in the field to real-time data, user manuals, instructions, diagrams and more.
• Less human error. The software locates the right equipment and guides operators step-bystep through complete maintenance procedures.
“We’re excited to partner with one of the most technologically advanced leaders in packaging and machinery,” Gonzalo Buelta, Vice President, Industry OEM Business, U.S. at Schneider Electric. “Delta Systems continues to raise the bar through its integrated approach to system supply, quick turn around on parts and R&D improvements. We look forward to working together to drive the industry forward, while harnessing EcoStruxure as the driving technology for maximum reliability and efficiency.”
In addition to providing the external control system, Schneider Electric is also adding its P4 3-Axis Delta Robot, an add-on to its PacDrive product line, to Delta System’s Flow Wrapper machines. The P4 Delta Robot consists of stainless-steel housing, arms, and rotational axis with 15-kilogram load capacity, which is different compared to competitors and well suited for the food, pharma, cosmetics, and beverage industries. The P4 Delta Robot will also enhance operations by allowing the regular Flow Wrapper machine and the robot to be managed with one controller and monitored using Augmented Operator Advisor