Rockwell Automation and Comau Partner to Simplify Robot Integration for Manufacturers
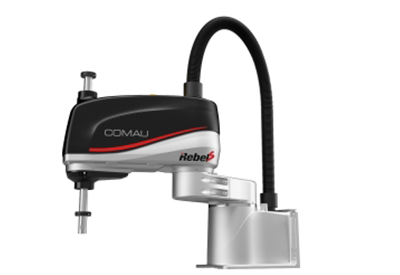
April 20, 2021
Rockwell Automation, Inc., a global company dedicated to industrial automation and digital transformation, and Comau, a global provider in industrial automation and robot manufacturer, recently announced that they are joining forces to give businesses worldwide vital tools to maximize manufacturing efficiencies through unified robot control solutions.
“Industrial companies are looking for efficient ways to integrate robotics into their operations for process optimization and agility,” said Rockwell Automation Chairman and CEO Blake Moret. “Rockwell Automation’s collaboration with Comau will simplify programming and lifecycle management, accelerating time to value for our customers.”
Moret said this expansion of robotic applications is rooted in Rockwell’s broader strategy to help industrial companies save time and improve performance with unified robot control, ultimately providing long-term value for their business. The partnership is a collaborative development and selling model that offers the unified robot control product to both companies’ customers.
“Comau’s robotics and industrial automation expertise, as well as its reputation for high performance, reliability, and quality, combined with Rockwell Automation’s global capabilities and experience in automated material handling, food and beverage, household and personal care, and life sciences, gives customers the incremental value of an integrated robot solution,” said Comau CEO Paolo Carmassi. “Comau is eager to work with such an important partner that has a market-leading global footprint in all industries.”
Engineers will now be able to program their entire machine in one environment, including Comau robot arms directly controlled through Rockwell Automation’s Logix-based controllers. Rockwell Automation’s Studio 5000 automation system design software provides relief from the time-consuming and often difficult task of trying to coordinate traditionally separate machine control and robot systems to work together using two different software tools.
Machine builders, system integrators, and others will gain development and deployment efficiencies through the use of digital engineering tools like Rockwell’s Emulate3D digital twin software, which creates digital models of production lines, auto-generates machine control code, and has built-in capabilities for Comau robots.
The combined Rockwell and Comau solutions will also offer benefits beyond enhanced integration. For example, end users can use analytics and digital twin tools to gain deeper insights into machine performance and potential production optimization. They can also use safety and security solutions to reduce business risks.
Operators on the manufacturing floor who use Rockwell’s FactoryTalk software suite will benefit from being able to see both line and robot control systems on a single interface. In-plant and remote technicians will only need to learn and maintain one architecture to monitor both systems. They can also leverage Rockwell’s augmented reality (AR) tools to improve lifecycle and service cycle maintenance.
Automazioni Industriali Capitanio, a recognized system integrator, designs, manufactures, and commissions automation systems for the metals industry and is an early adopter of the joint solution. Marco Capitanio, managing director of AIC, said the Rockwell-Comau collaboration allows the company to offer a seamless robot solution for customers, which he sees as a key advantage for a machine builder.
“We value the simple and flexible programming environment, complete access to robot supervision and diagnostic parameters, and the ability to leverage existing automation panels and standard control devices,” Capitanio said.
Rockwell products and technology that will be key to robotics integration include the following:
- – Allen-Bradley ControlLogix control systems
- – Kinetix 5700 servo drive platform
- – Studio 5000 automation system design software
- – FactoryTalk View human machine interface (HMI) software
- – FactoryTalk InnovationSuite, powered by PTC digital transformation software suite
- – Emulate3D digital twin software
- – PTC Vuforia AR tools for remote collaboration and information capture
Comau’s comprehensive robot range meets the needs of a wide variety of industries, from automotive to logistics, food and beverage, and packaging, just to name a few. It includes more than 40 different industrial robotic arms, with load capacities from 3 to 650 KG.