Next-Generation Process Safety Systems Maximize Uptime of Increasingly Demanding Applications
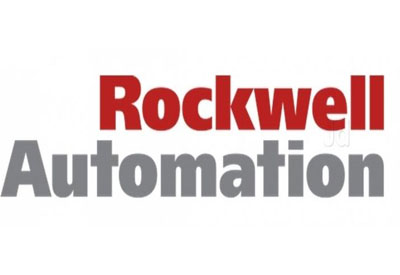
October 30, 2018
Rockwell Automation has updated its process safety logic-solver platforms to maximize uptime for industrial producers who want to help ensure compliance with the latest safety requirements. As companies face increasingly demanding process safety applications — whether a new installation or part of managing the installed base of legacy systems — the AADvance fault-tolerant system and Trusted fault-tolerant system utilizing the common SIS Workstation software help producers meet the requirements of their process safety functions. They also maximize uptime through increased scalability, communication and resiliency features. All systems are compliant with the IEC 61508 functional safety standard.
“With next-generation performance capabilities, the updated process safety logic-solver offerings will help achieve process safety system performance requirements in connected operations,” said Steve Del Rio, global business manager for safety, Rockwell Automation. “These enhancements underscore our commitment to investing in high-performance safety solutions and supporting next-generation, logic-solver applications with maximum safety and system availability.”
SIS Workstation software: The latest SIS Workstation software converges the AADvance and Trusted design tools into one, resulting in easier system support. Through the merging of technologies, users can now learn a single platform, which improves training and streamlines communications for topologies using both platforms. The SIS Workstation software also uses a singular, modern configuration environment for both the AADvance and Trusted systems which enables faster and more reliable field commissioning and is supported by all Microsoft Windows platforms.
Trusted fault-tolerant SIS: The updated Trusted system can now execute code up to three times faster for higher-speed applications, such as turbomachinery control. The system includes triple modular redundant (TMR) controllers, a wide range of analog and discrete I/O modules and specialty modules for turbomachinery control.
It is designed to help minimize system trips and provide high availability and fault tolerance. The latest release also incorporates improved packaging to help enhance its performance in harsh environments — especially beneficial for applications in hot and humid conditions, such as offshore oil and gas operations. It also meets or exceeds the latest hardware design standards, providing more robustness in environmental and emissions performance at the board level.
AADvance fault-tolerant SIS: The updated AADvance system features enhanced communication compatibility with other plant-wide systems, such as ControlLogix controllers. By safely sharing information such as diagnostics and alarms with other plant assets, the overall ability for operations to respond to abnormal situations is improved.