Mazak: Defusing Explosive Titanium Additive Situations
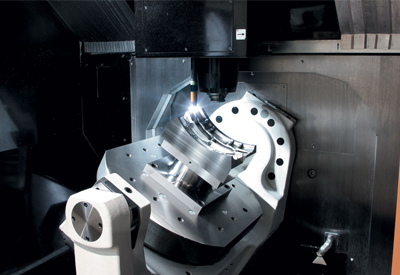
July 2, 2019
For manufacturers across every industry, additive manufacturing (AM) holds enormous promise, particularly when it comes to the production of parts made from high-value materials such as titanium. Rather than starting with a block of titanium large enough to contain an entire part and cutting it down to size – creating a massive heap of chips in the process – AM allows manufacturers to build parts to near-net shape. Nevertheless, one key feature shared by many AM processes presents a serious challenge to the technique’s widespread use: the volatility of titanium feedstock.
Pure titanium is a relatively reactive metal, especially at the temperatures seen in machining operations, but as with many reactive metals, the risk of an explosive reaction is mitigated by passivation, or the natural formation of a protective layer over the metal’s surface. For AM processes, however, the increased surface area of AM-grade titanium powder raises the level of reactivity, especially when the heat is sufficient to disrupt the protective oxide layer. If mishandled, the result is a “thermal event,” the engineer’s polite method of referring to chemical and physical reactions that result in fires and explosions.
Generally speaking, the advantages of powder AM systems far outweigh the disadvantages for many shops. After all, with AM-grade titanium powder, parts with well-finished, complex interiors that cannot be created through any subtractive method become possible. Systems like Mazak’s own laser and multi-laser deposition technologies are ideally suited to tasks such as repair and cladding with titanium. With these technologies, which use argon as a shielding gas to prevent oxidation and the risk of a thermal event, as well as proper storage and handling practices, AM-grade titanium powder can play a safe and productive role for manufacturers interested in leveraging state-of-the-art technology for their part-production success.
When necessary, Mazak’s Hybrid Multi-Tasking machine lineup offers an alternative to powder based AM: Hot Wire Deposition (HWD). Rather than prioritizing additive precision, this technology delivers an extremely high deposition rate and utilizes a much less reactive and cheaper form of titanium: wire. HWD takes advantage of a wire AM process originally based on CNC welding technology. A century of welding has resulted in textbooks filled with wire’s behavior at different temperatures and appropriate feeder rates, and because titanium wire has an intact passivation layer to prevent further oxidation, it requires no additional storage considerations. Bales of wire can simply be put away just like any other inert material.
To reduce the high temperatures of arc torches to a level usable for AM processes, HWD incorporates heating elements within its wire AM head to bring the wire to a set temperature prior to it being extruded and melted by a laser. By modifying the mixture of pre-heating temperature and laser wattage, operators have precise control over material qualities and a deposition rate measured in pounds per hour instead of ounces or grams.
As part of Mazak’s HYBRID Multi-Tasking family of technologies, HWD is designed for single-setup production on 5-axis machining centers like the Mazak VC-500A/5X AM HWD. Interested in learning more? Visit the HYBRID Multi-Tasking process page and discover how this advanced process can save you time and money while providing a way to bring additive technology into your shop.