Efficient, Intelligent, Compact and Quiet: new CrytoBox from Bosch Rexroth
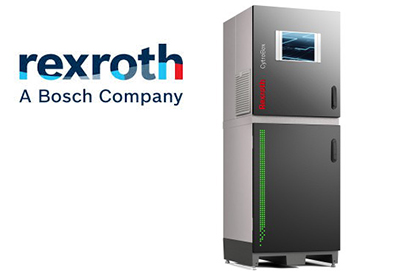
March 18, 2019
New hydraulic power unit for the medium performance range from 7.5 to 30 kW for efficient production:
- Compact control cabinet format
- Energy savings of up to 80 percent
- Condition monitoring and data analysis
Connecting machines and facilities with IT systems opens up enormous potential for making tire curing more economical and more intuitive. This is exactly where the new CytroBox hydraulic power unit from Bosch Rexroth comes in.
With its intelligent, energy-efficient modular design, it provides a new solution approach for the medium performance range up to 30 kW. By integrating IoT technologies, it also paves the way for consistently implementing Industry 4.0 concepts.
The CytroBox is a hydraulic power unit for the medium performance range up to 30 kW. The current consumption is parametrized and optimized with regard to the existing electrical cabinet. Preset controllers in variable-speed pump drives adjust energy requirements on an individual basis. Consequently, the speed is switched off during no load or the vulcanization of the tire to save energy and is controlled under full load in a closed loop to the exact pressure command value with a highly dynamic response. It saves up to 60 percent of energy compared to conventional power units, which are implemented in tire curing presses.
The high degree of efficiency of the manifold block, manufactured using the 3D sand core printing method, also contributes to efficient operation. With this additive manufacturing method, the manifold block is up to 40 percent more compact and has improved flow channels. This improves the oil flow, reduces pressure losses and minimizes the areas where leaks could occur, as fewer plug screws are required. Moreover, the hydraulic power unit is also equipped with an active dewatering unit against external contamination.
Cleverly connected to condition monitoring
Equipped with a sensor package and open interfaces, the CytroBox is predestined for use in connected environments. Integrated and wired sensors provide information regarding the current filter, oil or drive condition. The collected data are then processed by the drive controller. With the help of Open Core Interface, they can then be conveniently further processed and integrated into modern machine concepts.
The CytroBox also offers a connectivity option for operators. This makes it easy to realize the potential of IoT technologies as a pay-per-use service easily and without risk. All information regarding the CytroBox – from the component and operating status or forthcoming maintenance work to predictive maintenance analyses is available via Rexroth’s Online Diagnostics Network (ODiN). As a result, the information is always close to hand.
Full performance with the smallest of footprints
Flexibility and a space-saving design are important criteria when selecting components. The CytroBox combines a small footprint with a compact design. This also includes a tank with optimized degassing and flow. Thanks to a CFD simulation, the oil volume is reduced by 75 percent – from 600 to a mere 150 liters. The use of synchronous technology also saves space. The high-performance water-cooled synchronous motors are up to 80 percent smaller than comparable asynchronous ones. All functions are brought together in a compact control cabinet. As a result, the CytroBox can be integrated into existing production lines in a flexible, space-saving manner.
Lower noise emissions for greater comfort when working
The airborne sound is absorbed completely by the compact arrangement of all the components in one unitary housing and the built-in sound insulating mats. This way, no sound leaks out. In order to reduce noise emissions stemming from structure-borne noise, the motor pump group is rigidly affixed to a polymer-concrete foundation. The damping bearings which typically transmit the noise to the tank are completely eliminated. Consequently, the noise emission of the CytroBox is less than 75 dB (A) – even at full load. Comparable power units have an average noise level of 85 dB (A). This reduces the need for measures and costs for noise reduction, and also makes working very pleasant, even in direct proximity to the hydraulic power unit.