Beckhoff Introduces Machine Learning for All Areas of Automation
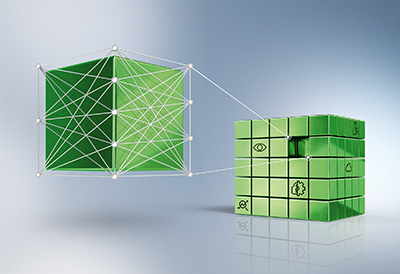
April 17, 2019
Beckhoff Automation has announced a new machine learning (ML) solution that is seamlessly integrated into TwinCAT 3 software. Building on established standards, TwinCAT 3 Machine Learning offers ML applications the same advantages of system openness familiar from PC-based control technology. In addition, this TwinCAT solution supports real-time ML, allowing it to simultaneously handle demanding tasks like motion control. These capabilities provide machine builders and manufacturers with an optimum foundation to enhance machine performance, for example, through predictive maintenance, process self-optimization and autonomous detection of process anomalies.
With machine learning, controls engineers no longer have to follow the traditional engineering route of designing solutions for specific tasks and turning those solutions into algorithms. Instead, the automation controller can learn the desired algorithms from exemplary process data. With this alternative approach, powerful ML models can be trained and then used to deliver superior, higher-performing solutions. In automation technology, this opens up new possibilities in many areas, including predictive maintenance and process control, anomaly detection, collaborative robotics (cobots), automated quality control and machine optimization.
The models to be learned are trained in an ML framework, such as MATLAB® or TensorFlow, and then imported into the TwinCAT runtime via the Open Neural Network Exchange Format (ONNX), a standardized data exchange format used to describe trained models. The TwinCAT runtime incorporates the following new functions for this purpose:
- TwinCAT 3 Machine Learning Inference Engine for classic ML algorithms, such as support vector machine (SVM) and principal component analysis (PCA)
- TwinCAT 3 Neural Network Inference Engine for deep learning and neural networks, such as multilayer perceptrons (MLPs) and convolutional neural networks (CNNs)
Directly execute model results in real-time
Inference, i.e. the execution of a trained ML model, can be performed directly in real-time with a TwinCAT TcCOM object. With smaller networks, system response times of less than 100 µs corresponding to a TwinCAT cycle time of 50 µs are supported. Models can be called via PLC, C/C++ TcCOM interfaces or a cyclical task.
Through seamless integration with the control technology, the multi-core support provided by TwinCAT 3 is also available for ML applications. This means, for instance, that different task contexts can access a particular TwinCAT 3 Inference Engine without restricting each other. All fieldbus interfaces and data available in TwinCAT remain fully accessible as well. This allows ML solutions to use immense amounts of data, for example, for complex sensor data fusion (data merging), and it also means that real-time interfaces to actuators are available to enable, among other things, optimal controller performance.
Go HERE for more information