POSITAL Announces Ultra-Heavy-Duty Absolute and Incremental Rotary Encoders
February 12, 2025
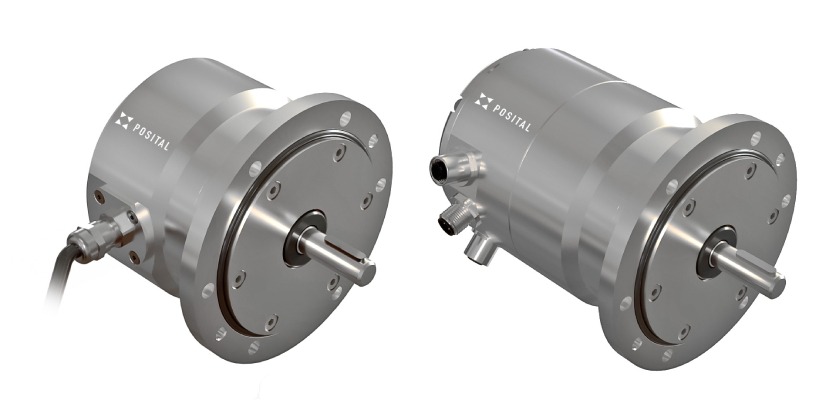
POSITAL has introduced a new series of IXARC rotary encoders designed for applications where high shaft loadings may be encountered. With heavy-duty housings and shaft bearings, these units are designed to withstand radial shaft loads of up to 350 N (80 pounds) and axial loads as high as 250 N (56 pounds), making them ideal for the challenging operating conditions encountered in marine and off-shore facilities, cargo-handling cranes, construction equipment, and machinery or the forestry and logging industries.
These encoders are available with either aluminum or V4A (312L) stainless steel housings. The corrosion-resistant stainless-steel option is an ideal choice for mines, off-shore facilities and chemical plants. IP67-rated seals on the shaft entry and connectors protect internal components from dust and immersion in water or other fluids, while a semi permeable protective membrane reduces moisture build up inside the housing. These measures prolong the life of electronic components and reduce the risk of measurement errors due to condensation on the optical code disk.
These devices can withstand shocks as high as 200 g and continuous vibrations up to 20 g. (100 g shock and 10 g vibration for multi-turn absolute versions) and have an operating temperature range of -40° C to +80° C (-40° to 176° F). They have been certified by an independent testing authorities as meeting ATEX and IECEx requirements for use in environments with potentially dangerous levels of flammable gases or dust (Zones 2 and 22).
Heavy-duty IXARC encoders are offered in absolute and incremental versions, both based on POSITAL’s well-proven optical measurement technology. Absolute versions feature 13-bit resolution, with a range of 4096 revolutions for multi-turn variants. Multiple interface options are available, including PROFINET (RT or IRT), SSI, CANopen, EtherCAT and EtherNet/IP. Three M12 connectors on the housing, enable users to daisy-chain several devices together for more convenient cable layouts. Indicator LEDs on the endplate simplify system setup and troubleshooting.
For incremental encoders, customers have the choice of forty-six resolution values, starting at two pulses per revolution (PPR) and going up to 4096 PPR. (Others are available by special order.) Accuracy is ±0.002°. The output driver for incremental models supports RS 422 (TTL) communications. Like other IXARC encoders, these devices are built using POSITAL’s unique “mass customization” manufacturing process. Customers can specify the exact combination of mechanical features and performance characteristics they need and have the finished product shipped in a matter of days. Minimum order quantity? One!
More Information
Related Product
POSITAL Announces Upgrades to IXARC Incremental Rotary Encoders
POSITAL has enhanced its IXARC family of incremental magnetic encoders, increasing the maximum resolution to 32,768 pulses per revolution (PPR). This upgrade includes new phasing options, offering a choice of wider index (Z) pulses, making it easier to replicate the features of older encoders – an important feature for the Maintenance, Repair, and Operations (MRO) market.
This higher resolution is made possible by the introduction of TMR magnetic sensor technologies. Power consumption has also been reduced, another important consideration for MRO buyers.