Rockwell’s Medium-Voltage Drive Technology Helps West Fraser Reduce Annual Energy Bill
January 9, 2025
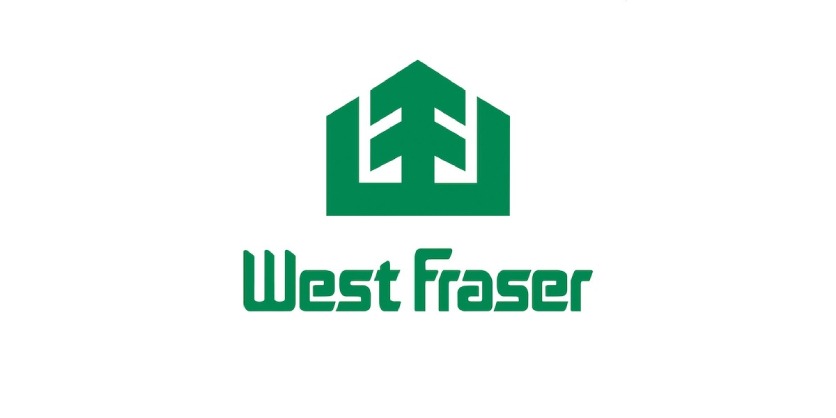
Industrial applications that run things like pumps, fans, conveyors, and compressors are responsible for more than 50% of the world’s total electricity consumption. One option to dramatically reduce that drag on resources is variable frequency drives (VFDs). These devices can adjust the frequency and voltage of the power supply, which can help improve the motor’s efficiency and even extend the life of the motor.
Rockwell Automation helped West Fraser, a diversified wood products company, make significant gains towards energy saving targets through an Intelligent Packaged Power (IPP) solution featuring VFDs. An IPP solution simplifies the integration between process and electrical systems—giving workers immediate access to real-time data on the equipment and how it is operating so they can make better decisions faster.
West Fraser’s plant in Cowie, Scotland, began using a Rockwell CENTERLINE® 1500 medium-voltage motor control center (MCC) and three PowerFlex® 6000T medium-voltage VFDs across three of the site’s energy-intensive fan applications. As a result of reducing motor speed by 25%, West Fraser lowered the motor’s energy consumption by approximately 60%, translating into an annual savings of more than $266,000.
This is just one example of how VFDs can have a profound, positive impact in reducing energy consumption and cutting carbon levels.
More Information
Related Story
How to Prevent MCC Corrosion with Insulated Bus Technology
Many industries around the world face challenges with corrosive environments, whether it is inside their facilities with air pollutants such as sulfur dioxide, or outdoors with corrosive factors such as water and salt fog. Corrosion is the single largest cause of the breakdown of machinery, structures, supports, and motor control equipment in a plant.