Identifying Air and Gas Leaks
October 9, 2024
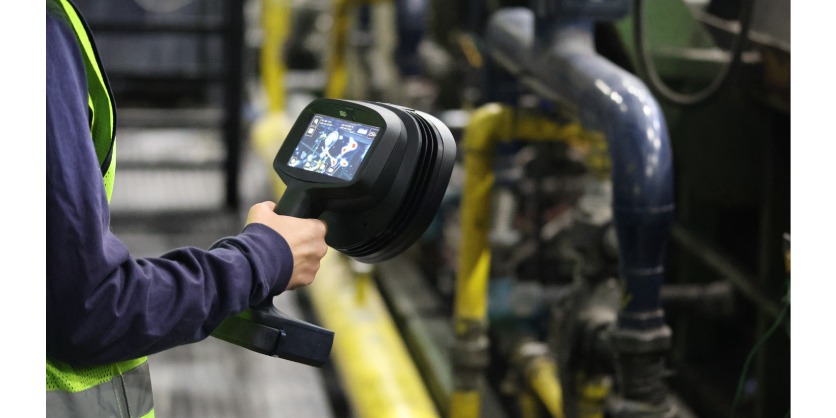
Author: Darrell Taylor
The other day I performed a Google search for ‘How to detect an air leak’. Not surprisingly it came up with millions of results to detect leaks, over 18 million in fact.
Whether solving the problem in a commercial establishment or a domestic home environment, the majority of search results pointed to one solution. Namely, soapy water!
Before we all ridicule the idea as belonging to a bygone era, take a vehicle with a slow puncture to a tire fitting depot and the chances are they remove the wheel and spin it in water to determine the leak. It’s a simple time proven method for determining leaks from pressurized systems.
But of course, not all equipment can be placed in soapy water. What if a system is known to be losing pressure and yet the lines carrying the compressed air from the source are located 10 metres above the ground, and dismantling the system is out of the question? Thankfully there is a fast and effective solution at hand.
Each time air or indeed any gas, leaks from a pressured system there is an associated sound. If the leak is significant, it can be audible to the human ear and therefore easily identified and rectified accordingly. However, most leaks in high pressure systems are extremely small and are out of the range of a human ear.
Think about a pressured air system on a large factory delivering compressed air from a bank of compressors to various stages of production throughout the manufacturing process. The chances are there are hundreds if not thousands of connections in the form of joints, reducers, valves, elbows, condensers etc. Each of these has the potential to leak small amounts of air, reducing the pressure of the system.
One leak might make very little difference but multiply this by the number of potential leaking joints and efficiency can be significantly compromised. The compressor will seek to compensate for any pressure loss by simply working harder. However, as any engineer will know, compressors can be expensive to operate in terms of energy and therefore will certainly increase an operators energy consumption.
With electricity costs being so much higher in Europe due to geopolitical factors in recent years, and other regions as well, and most companies are seeking to reduce the amount of energy used. Having a compressor work overtime to compensate for leaking joints is certainly not something senior management would smile about!
These scenarios are certainly not uncommon, in fact one European compressor manufacturer has stated that in some industrial settings, up to 80% of air generated is lot in leaks for example. So clearly identifying these small leaks can make a real difference to a company’s energy bills.
Although the sound produced by a small leak is inaudible to the human ear a high performance acoustic imaging camera such as the FLIR Teledyne Si2 – LD will have absolutely no problem identifying the source. Launched earlier this year the camera is capable of detecting leaks of 0.05 litres per minute at a distance of 10 metres, meaning those elevated air lines pose no problem for this latest instrument in the FLIR acoustic imaging camera line up.
For closer work the camera is even more sensitive and can detects minute leaks of 0.0032 litres per minute at a distance of 2.5 metres. Coupled with this improvement, the third-generation camera has improved microphones now capable of detecting sounds over an extremely wide frequency range, namely 2 – 130 kHz.
Areas of plant are often dark or dimly lit. for this reason FLIR have fitted the FLIR Si2-series of cameras with two powerful LED lights to make component identification easy even in poorly lit conditions.
Of course, it’s not just compressed air that the camera is capable of detecting; noise emitted by any escaping gas is identified by the powerful microphones. However that’s only part of the story.
The FLIR Si2-LD has built in software termed Industrial Gas Quantification. If the leaking gas is ammonia, hydrogen, helium, or carbon dioxide, very commonly used gases in a number of industries, the software is capable of quantifying the financial loss caused by the leak. By simply entering factors such as the cost per litre, the software identifies the amount each leak is causing over a given period of time. Such data is invaluable to financial analysts and senior management within an organisation.
It goes without saying that the financial considerations are only one aspect of leaking gas. The gases mentioned above all carry significant health hazards and can present a variety of dangers to personnel if allowed to leak for any period of time. Ammonia and carbon dioxide can cause serious breathing problems and asphyxiation even in smaller concentrations, whereas hydrogen can explode in the presence of oxygen. Clearly the cost of such problems goes way beyond any financial considerations.
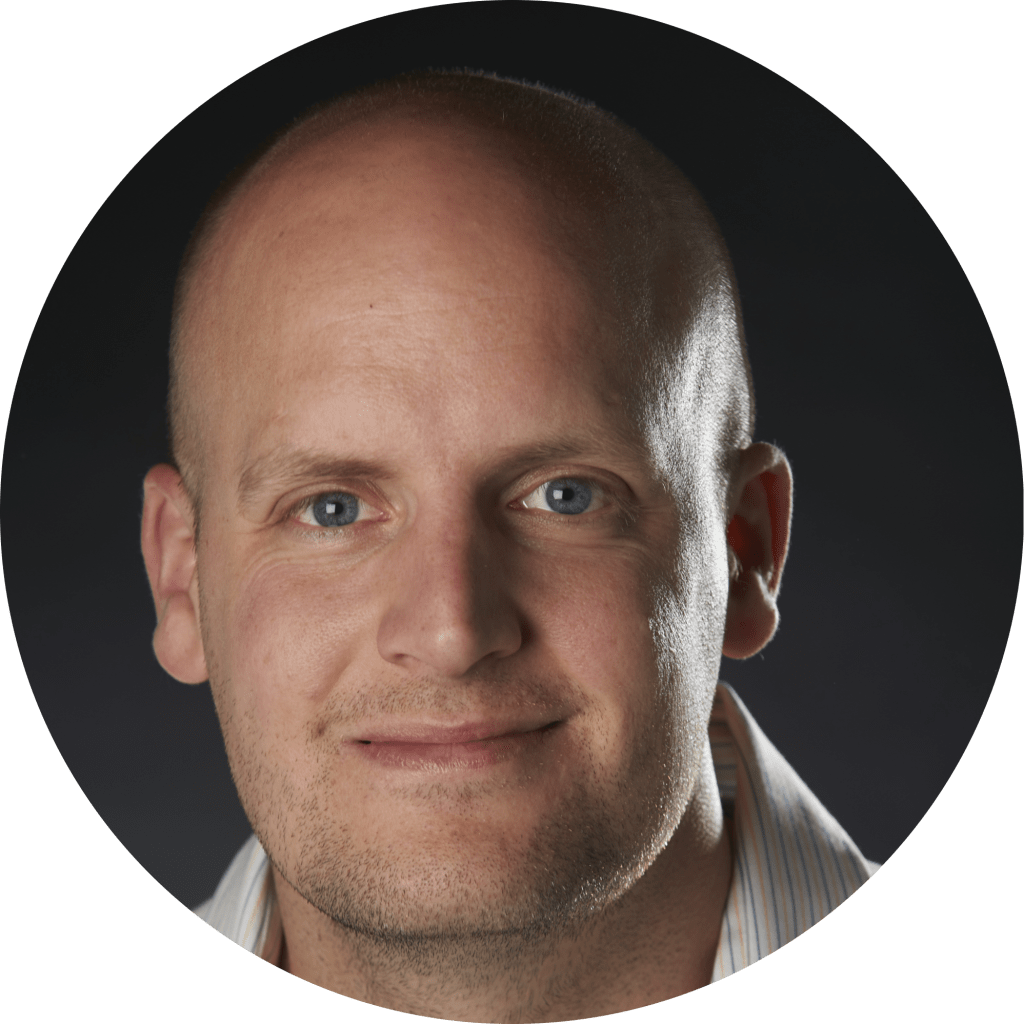
More Information
We’ve come a long way since the ‘soap and water’ approach. See how the latest technology from FLIR Teledyne can help in reducing downtime, lower energy bills and improve safety in your organisation.
Visit www.flir.com or contact you local FLIR Teledyne agent or distributor.
Related Story
FLIR Announces Si2-Series of Acoustic Imagers to Detect Compressed Air Leaks, Partial Discharges, Mechanical Faults, and Quantify Gas Leaks
FLIR, a Teledyne Technologies company, has announced the expansion of its versatile Si-Series of acoustic imaging cameras with three models in the new Si2 family, designed for detecting compressed air leaks, specialty gas leaks, mechanical faults, and partial discharges: the Si2-Pro, Si2-LD, and Si2-PD. The Si2-Series offers industrial-grade solutions for the detection of air and gas leaks as well as mechanical faults such as bearing issues, addressing the top inspection requirements for industries such as manufacturing, electrical, and utilities.