A Guide to Controller Area Network (CAN) for Industrial Applications
July 10, 2024
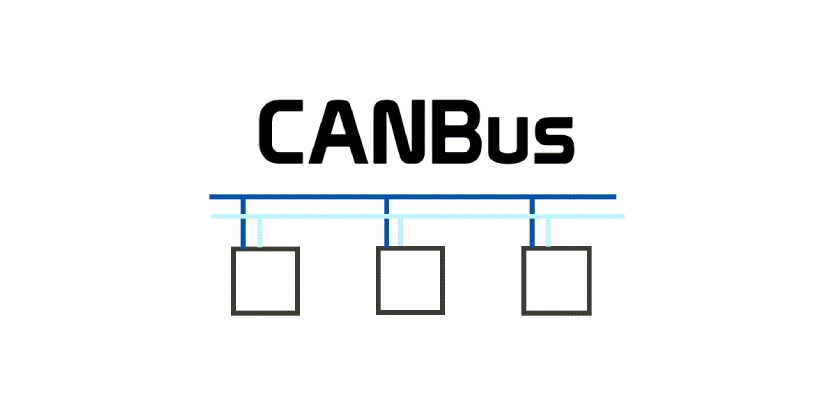
In industrial and automotive communication protocols, the Controller Area Network (CAN) bus stands out for its robustness, efficiency, and adaptability.
Originally developed for the automotive industry to reduce the complexity and weight of car wiring, CAN bus has expanded beyond its initial application to become a widely adopted standard in mechatronics and industrial automation.
This guide explores all things CAN: its operational principles, key benefits, and the spectrum of its applications, providing a foundational understanding for professionals looking to integrate this technology into their systems.
Understanding Controller Area Network (CAN) bus
At its core, CAN bus is a serial communication protocol that enables multiple microcontrollers and devices to communicate with each other within a vehicle or industrial system without the need for a central computer. This decentralized approach is key to CAN bus’s efficiency and reliability, allowing for real-time control and data exchange even in environments subject to significant electrical interference and physical conditions.
Key Features of CAN bus
- Multi-Master System: CAN bus operates on a multi-master principle, where any device on the network can initiate communication. This flexibility ensures that critical messages can be transmitted without delay.
- Priority-Based Message Transmission: Messages on a CAN bus network is prioritized based on their identifier fields, ensuring that higher-priority messages gain access to the bus more quickly, which is crucial for time-sensitive operations.
- Error Detection and Handling: CAN bus incorporates robust error detection mechanisms, including frame check, bit monitoring, and acknowledgment checks. This error handling capability enhances the reliability of data transmission.
- Resistance to Interference: The physical layer of CAN, often implemented with differential signaling, provides high resistance to electrical noise, making it ideal for use in harsh industrial environments.
Main Types of CAN bus Used in Industrial Applications
- CANopen: Developed for automation systems, CANopen standardizes the communication objects and provides a wide range of device interoperability options, making it suitable for complex machinery and system networks. It’s widely used in applications that require precise synchronization, such as in motion control systems.
- DeviceNet: Focused on industrial automation, DeviceNet uses CAN for networking sensors, actuators, and other industrial devices. It simplifies the connection and communication among devices and provides power over the bus, which reduces wiring complexity.
- SAE J1939: Used primarily in heavy-duty vehicles and mobile equipment, J1939 is based on CAN and supports messaging and network management capabilities tailored for vehicle applications. It allows integration of vehicle and engine components into a single network with high-bandwidth and robust control capabilities.
Benefits of CAN bus in Industrial and Automotive Applications
The widespread adoption of CAN bus across different industries can be attributed to several compelling advantages it offers:
High Reliability and Robustness
- Error Detection Capabilities: CAN bus’s sophisticated error detection mechanisms, including cyclic redundancy checks (CRC), ensure high data integrity, making it exceptionally reliable for critical communications.
- Fault Confinement: CAN bus isolates problematic nodes to prevent them from compromising the entire network, ensuring system-wide robustness.
Efficiency and Scalability
- Efficient Use of Network Bandwidth: The priority-based message transmission system allows for efficient use of the network, ensuring that messages are delivered in a timely manner based on their urgency and importance.
- Scalability: CAN bus networks can easily accommodate additional nodes, making it simple to expand the system without significant redesign or cost.
Flexibility and Simplicity
- Multi-Master System: The ability for any device to initiate communication without a central controller simplifies network architecture and increases system flexibility.
- Widespread Adoption and Support: With its origins in the automotive industry and expansion into industrial automation, CAN bus benefits from broad industry support, including a wide range of tools, software, and hardware options.
Operational Principles of CAN
Understanding how CAN bus operates requires a closer look at its communication model, message structure, and transmission process.
Communication Model
- Bus Topology: CAN bus uses a bus topology, where all nodes are connected to a single communication line. This design simplifies wiring and ensures that messages are accessible to all nodes.
- Differential Signaling: CAN bus’s physical layer typically uses differential signaling to reduce susceptibility to electrical noise, enhancing signal integrity over long distances and in noisy environments.
Message Structure
- Identifier (ID): Each message on the CAN bus network has a unique identifier that determines its priority, with lower ID values having higher priority. This ID not only controls message priority but also serves as the message label, eliminating the need for source or destination addresses.
- Data Field: Following the identifier, the data field can carry up to 8 bytes of data per frame, making it suitable for a wide range of control and monitoring tasks.
Transmission Process
- Arbitration: When multiple nodes attempt to transmit simultaneously, CAN bus uses non-destructive arbitration based on ID priority to resolve conflicts, ensuring that the highest-priority message is transmitted first.
- Message Transmission: Once the bus is free, the node with the highest-priority message transmits its data. Other nodes become receivers and check the message for errors.
- Acknowledgment: After successful transmission, receiving nodes send an acknowledgment bit, confirming receipt of a valid message.
This operational model allows CAN bus to facilitate reliable, real-time communication critical for automotive systems, industrial automation, and other applications where data integrity and timely delivery are paramount.
Understanding CAN 2.0A and CAN 2.0B
The evolution of the CAN protocol has led to the development of two significant versions: CAN 2.0A and CAN 2.0B, which are distinguished primarily by their differences in message identifier lengths and thus, network capacity.
- CAN 2.0A: Also known as Standard CAN, CAN 2.0A utilizes an 11-bit identifier, which allows for up to 2,048 different message identifiers. This version is sufficient for most applications where the network complexity and the number of devices are moderate.
- CAN 2.0B: Known as Extended CAN, CAN 2.0B expands the identifier to 29 bits, offering over 536 million possible message identifiers. This extension is beneficial in complex systems with many sensors and actuators, as it greatly increases the network’s address space and allows for more granular control with more devices.
Both versions maintain compatibility with each other at a basic operational level in mixed networks. CAN 2.0B is fully backward compatible with CAN 2.0A; however, when both types of messages are present on the same network, care must be taken in message priority management and identifier assignment to avoid conflicts and ensure efficient data flow.
This differentiation allows engineers to select the most appropriate CAN version based on their specific requirements, balancing network complexity with control granularity.
Applications of CAN bus in Precision-Required Environments
CAN bus’s robustness, efficiency, and flexibility make it a preferred choice for a myriad of applications beyond its automotive origins. Here are some key areas where CAN bus technology shines:
Automotive Systems
- In-Vehicle Networks: CAN bus is used extensively for communication between various control units such as the engine control unit (ECU), transmission, airbags, antilock braking system (ABS), and more, facilitating real-time control and diagnostics.
- Advanced Driver Assistance Systems (ADAS): For systems requiring quick and reliable data exchange, such as collision detection, lane assist, and adaptive cruise control, CAN bus provides the necessary performance and reliability.
Industrial Automation
- Manufacturing Equipment: CAN bus networks connect sensors, actuators, and controllers in manufacturing lines to coordinate complex sequences of operations, enhancing efficiency and flexibility.
- Process Control Systems: In industries ranging from chemical manufacturing to food processing, CAN bus facilitates the real-time monitoring and control of process parameters, ensuring optimal production conditions.
Medical Devices
- Patient Monitoring Systems: CAN bus is used in medical monitoring equipment, providing reliable data transmission critical for patient care.
- Surgical Robots: For devices requiring precise control and feedback, such as surgical robots, CAN bus’s real-time capabilities ensure accurate and reliable operation.
Building Automation
- HVAC Systems: CAN bus helps in the efficient operation of heating, ventilation, and air conditioning systems by enabling real-time control and monitoring.
- Access Control Systems: In security and access control, CAN bus enables the integration of various components like sensors, alarms, and locks for enhanced building security.
Exploring CANopen and DeviceNet
While CAN bus serves as the foundational communication protocol, specific applications might require additional features or standardized communication objects. This is where CANopen and DeviceNet come into play:
CANopen
- Standardized Communication: CANopen is a higher-layer protocol that builds on CAN bus to provide standardized communication objects for control, device configuration, and monitoring, making it highly suitable for automation tasks.
- Flexible Configuration: With a focus on flexibility and interoperability, CANopen supports a wide range of devices and applications, from simple sensors to complex motion controllers.
DeviceNet
- Industrial Focus: DeviceNet utilizes CAN bus for industrial applications, offering a robust network protocol for automation equipment. It emphasizes ease of integration, device interoperability, and real-time performance.
- Extensive Device Support: Designed to connect industrial devices like switches, photoelectric sensors, and motor controllers, DeviceNet simplifies the creation of efficient, flexible automation systems.
The Controller Area Network (CAN) bus has established itself as a vital communication backbone in automotive, industrial, and various other sectors, credited to its unmatched reliability, efficiency, and adaptability. By enabling precise, real-time control and data exchange across a wide range of environments, CAN bus significantly enhances system performance and capabilities. Further enriched by protocols like CANopen and DeviceNet, CAN bus’s ecosystem offers extensive solutions tailored to meet specific application needs, reinforcing its position as a cornerstone technology in modern automated systems.
Related Story
Ask An Expert at Electromate
If you have questions about any of Electromate’s product offerings, please book a consultation with one of their Sales Engineers in your area. If you just have a question about one of their motion control or robotic lines, simply fill out the Ask an Expert form below. They strive to get you an answer ASAP.