Lubricants: Unlocking Peak Performance in Your Gearmotor
April 16, 2024
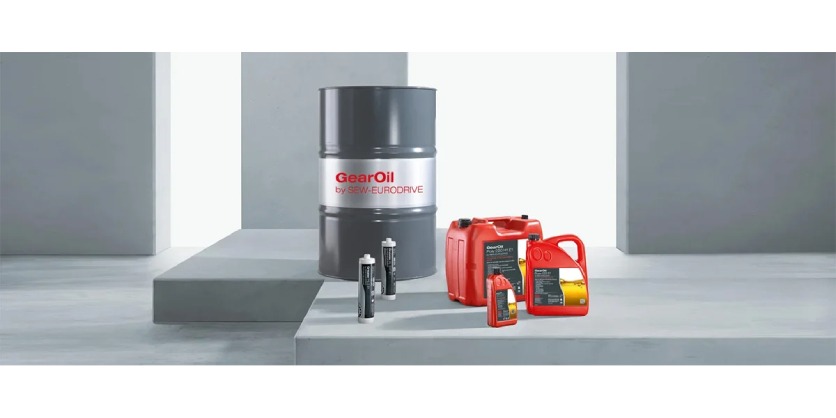
In the world of mechanical systems, gearmotors are the workhorses, driving operations across various industries. Yet, their efficiency and longevity hinge on a crucial component often overlooked: lubricants. Understanding the role of lubricants, how to select them, and the importance of maintenance can significantly impact your gearmotor’s performance and lifespan.
Understanding Gearmotor Lubricants
Lubricants in gearmotors serve several vital functions. They reduce friction between moving parts, minimize wear, protect against corrosion, and help dissipate heat. The right lubricant can ensure that your gearmotor operates smoothly, efficiently, and remains durable over time.
Types of Lubricants
Gearmotor lubricants come in various forms, including oils, greases, and synthetic options, each suited to different applications and environments:
- Oils: Ideal for high-speed and high-temperature conditions, oils are excellent at heat dissipation.
- Greases: Suitable for gearmotors operating under moderate speeds and temperatures. Grease stays in place better than oil, making it a good option for vertical or irregularly shaped gear units.
- Synthetic Lubricants: Designed for extreme conditions, synthetics offer superior performance in very high or low temperatures and provide longer lubrication intervals.
Selecting the Right Lubricant
The choice of lubricant depends on several factors:
- Operating Environment: Consider temperature, moisture, and exposure to contaminants.
- Load and Speed: High loads and speeds may require lubricants with specific properties to reduce wear and manage heat.
- Gearmotor Design: The manufacturer’s specifications can guide the viscosity and type of lubricant needed for optimal performance.
Maintenance and Changing Intervals
Regular maintenance and timely replacement of lubricants are key to preventing gearmotor failures. While the exact intervals can vary, here are some general guidelines:
- Initial Change: Some manufacturers recommend changing the lubricant after the first 500 hours of operation to remove any debris or contaminants from the initial break-in period.
- Regular Interval: Typically, lubricants should be changed every 7,500 to 10,000 hours of operation or at least annually, though harsh operating conditions may necessitate more frequent changes.
Signs You Need to Change Your Gearmotor’s Lubricant
- Increased Noise or Vibration: Could indicate lubrication breakdown or contamination.
- Overheating: Insufficient lubrication can lead to increased friction and heat.
- Visual Inspection: Discoloration or metal particles in the lubricant are signs of wear and contamination.
Conclusion
Lubricants play a critical role in the performance and maintenance of gearmotors. By selecting the appropriate type and diligently adhering to maintenance schedules, you can enhance the efficiency, reliability, and lifespan of your gearmotor systems. Remember, when in doubt, consult the manufacturer’s guidelines or reach out to a professional for advice on keeping your gearmotors running smoothly.
More Information
Download lubricant tables
Refer to SEW-Eurodrive’s lubricant tables to find the gear unit oil that is perfectly suitable for your drive and complies with the specific requirements of your application:
Standard gear units | Feb 27, 2024 | 01 751 28 04 | Go to table (PDF, 1,2 MB) (PDF, 1.3 MB) |
Industrial gear units | Jul 18, 2023 | 47 049 14 05 | Go to table (PDF, 1,1 MB) (PDF, 1.1 MB) |
Related Story
Compact Extra-Low Voltage Drives from SEW-Eurodrive
The new compact extra-low voltage drives are absolutely at home in the materials handling technology used in warehousing systems. They offer your applications high running smoothness, overload capacity and flexibility. They have a diverse range of potential uses, and they fit like a glove into even small installation spaces.