A Guide to Industrial Ethernet (IE)
April 2, 2024
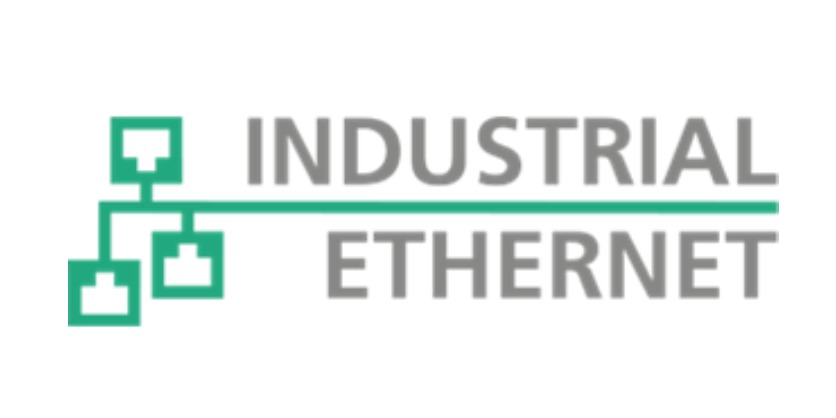
Ethernet has become the backbone of industrial communication, enabling devices and systems to exchange data rapidly and reliably.
This guide delves into Ethernet’s implementation in industrial settings, highlighting its advantages, protocols, frame structure, and data types to provide a solid foundation for professionals looking to leverage this technology.
Understanding Industrial Ethernet
At its core, Ethernet in industrial applications is adapted from the office Ethernet to meet the stringent requirements of automation and control systems. It offers a universal networking standard that ensures interoperability, reliability, and scalability.
Key Benefits
- High Speed and Bandwidth: Ethernet networks can significantly outpace traditional fieldbuses, offering speeds ranging from 10 Mbps to 10 Gbps. This high bandwidth supports the transmission of large amounts of data quickly, which is crucial for applications requiring real-time feedback and control.
- Scalability and Flexibility: The scalable nature of Ethernet allows for easy network expansion and reconfiguration without extensive downtime or overhaul. It supports a wide range of topologies such as star, tree, ring, and daisy chain, making it adaptable to various industrial layouts.
- Standardization and Interoperability: Ethernet uses standard protocols and interfaces, ensuring that devices from different manufacturers can communicate seamlessly. This interoperability reduces integration challenges and simplifies maintenance.
- Integration of Control and Information Layers: Unlike traditional systems where control and information networks operate separately, Ethernet facilitates the integration of both layers. This integration enhances data visibility across the enterprise, aiding in decision-making and process optimization.
Common Industrial Ethernet Protocols
Several protocols have been developed to tailor Ethernet for industrial applications, including:
- EtherNet/IP: Designed for industrial automation, it enables real-time control and information exchange, supporting various topologies.
- PROFINET: Aimed at collecting data from, and controlling, equipment in industrial environments, enhancing automation efficiency.
- Modbus TCP/IP: An extension of the Modbus protocol over Ethernet, facilitating communication between automation devices.
Ethernet Frame Structure
Key Components of an Ethernet Frame
- Preamble: The preamble consists of 7 bytes of alternating 1s and 0s, ending with two 1s. It serves to alert receiving devices to an incoming frame and enable synchronization.
- Start of Frame Delimiter (SFD): Following the preamble, the SFD is a one-byte field that marks the actual beginning of the frame. It signals the end of the preamble and the start of the Ethernet frame data.
- Destination MAC Address: This 6-byte field specifies the media access control (MAC) address of the receiving device. It ensures that the frame reaches the correct destination within a local network.
- Source MAC Address: Similarly, this 6-byte field contains the MAC address of the sending device. It identifies the frame’s origin, allowing for response or acknowledgment.
- EtherType/Length: This field can serve two purposes. It can indicate the type of payload contained in the frame (EtherType) or the size of the payload (Length), depending on the network configuration and standards.
- Payload (Data): The payload carries the actual data being transmitted. Its size can vary but must be within the minimum and maximum size limits defined by Ethernet standards to ensure proper network operation.
- Frame Check Sequence (FCS): The FCS is a 4-byte field used for error checking. It contains a cyclic redundancy check (CRC) value based on the frame’s contents. Receiving devices use this value to detect errors in the frame.
Importance of Ethernet Frame Structure in Industrial Applications
The structured format of Ethernet frames plays a vital role in the reliable and efficient transmission of data in industrial environments. It allows for:
- Error Detection: The FCS enables the identification and rejection of corrupted frames, crucial for maintaining data integrity in critical industrial processes.
- Network Management: The distinction between source and destination addresses facilitates network management and troubleshooting.
- Interoperability: Standardized frame structures ensure compatibility and interoperability among various devices and systems within an industrial setting.
Data Types in Industrial Ethernet
Understanding data types is crucial for data exchange and interpretation:
- Boolean: Represents a true or false condition, typically used for status indicators, alarms, and simple control logic.
- Integer Types:
- INT: A 16-bit (2-byte) integer, capable of representing values from -32,768 to 32,767.
- UINT: An unsigned 16-bit integer, representing values from 0 to 65,535.
- DINT: A 32-bit (4-byte) integer, for values between -2,147,483,648 and 2,147,483,647.
- UDINT: An unsigned 32-bit integer, for values from 0 to 4,294,967,295.
- Real Numbers:
- REAL: A 32-bit floating-point number following the IEEE 754 standard, used for analog values with decimal points.
- LREAL: A 64-bit floating-point number for higher precision analog values.
- String: A sequence of characters used to represent text. The length and character set can vary depending on the protocol and device requirements.
- Byte and Word:
- BYTE: An 8-bit (1-byte) data type, often used for compact binary data representation.
- WORD: A 16-bit (2-byte) data type, useful for combining multiple binary states or small integer values.
- DWORD: A 32-bit (4-byte) data type for longer binary data sequences or larger integer values.
- Time Types:
- TIME: Represents durations or intervals, often in milliseconds.
- DATE: Represents calendar dates.
- TIME_OF_DAY or TOD: Represents specific times of the day.
- DATE_AND_TIME or DT: Combines date and time for timestamping events.
- Structured Data Types: These are user-defined types (UDTs) that combine multiple primitive data types into a structured format, useful for representing complex data structures like objects, records, or configurations.
Importance of Understanding Data Types
- Precision in Data Handling: Choosing the appropriate data type ensures that the data’s precision and scale are maintained, especially critical for control and measurement applications.
- Efficiency: Using the most suitable data types can optimize network bandwidth and storage, particularly important in high-speed or large-scale industrial networks.
- Interoperability: Correct data typing is essential for interoperability between different devices and systems within an industrial setting, ensuring that data is accurately understood and acted upon across the network.
In industrial Ethernet communication protocols like EtherNet/IP, PROFINET, and Modbus TCP, these data types facilitate the structured and efficient exchange of information, allowing for precise control, monitoring, and integration of industrial processes. Understanding and utilizing these data types effectively can greatly enhance system performance and reliability in industrial automation and control systems.
Applications
Ethernet’s robustness and versatility facilitate its application across a wide spectrum of industries, including but not limited to:
- Manufacturing: For automation and control systems, Ethernet enables real-time monitoring and control of manufacturing processes, improving efficiency and productivity.
- Energy Sector: In power generation and distribution, it facilitates the management of smart grids, ensuring reliable energy flow and enabling predictive maintenance.
- Transportation: Ethernet supports signaling systems, real-time passenger information systems, and surveillance systems in airports, railways, and urban transit systems.
- Water Treatment: For control and monitoring of water distribution and treatment facilities, ensuring safe and efficient water supply.
- Oil and Gas: Used in remote monitoring and control of drilling operations, pipeline monitoring, and safety systems in hazardous environments.
- Building Automation: In managing HVAC, lighting, and security systems to improve energy efficiency and occupant comfort.
These applications showcase Ethernet’s capacity to support complex, real-time communication and control tasks across diverse industrial landscapes.
Conclusion
Industrial Ethernet stands as a pivotal technology in modern industrial automation and control systems, offering unparalleled speed, reliability, and flexibility. Its ability to integrate devices and systems across various industries while ensuring efficient, real-time data exchange underpins its critical role in the digital transformation of industrial operations. For engineers and professionals in the field, mastering the nuances of Ethernet communication is essential for designing and maintaining systems that meet today’s demanding industrial requirements. This guide serves as a foundation for understanding and applying Ethernet in industrial contexts, empowering professionals to leverage its full potential in driving operational excellence.
Related Story
A Guide to Modbus Communication Interfaces
Modbus is a widely used industrial communication protocol with several variants, including Modbus RTU, Modbus ASCII, and Modbus TCP/IP. It was initially developed by Modicon (now part of Schneider Electric) in the late 1970s and has since become a de facto standard for connecting various devices in industrial automation.