Motor Protection Filters for a Global Courier’s Distribution System
March 25, 2024
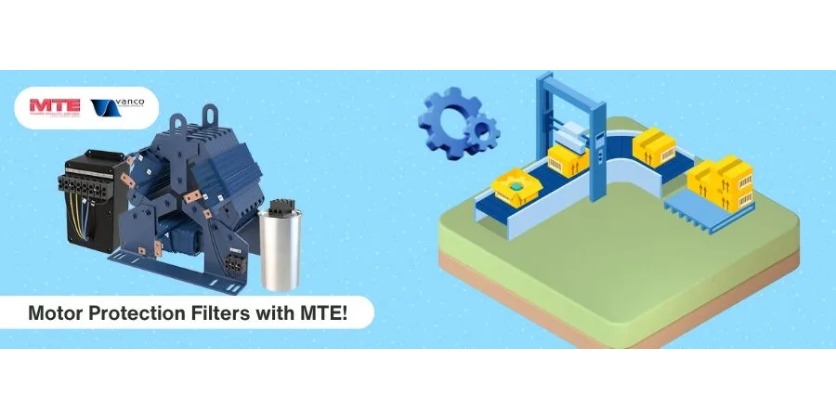
Motor protection filters for a global courier’s distribution system
In the fast-paced world of global courier services, the efficient movement of packages relies heavily on conveyor systems driven by induction motors. A leading courier company faced recurring challenges with motor and gearbox failures leading to disruptions in the package sorting process and increased maintenance costs. This case study explores the implementation of MTE Corp’s SineWave Nexus motor protection filters to address these issues and enhance the reliability of their distribution system.
Distribution Overview and Challenges
For context, the global courier company operates extensive package sorting facilities with conveyor systems powered by Variable Frequency Drives (VFDs). The conveyor gearboxes and motors are critical in ensuring the timely and accurate movement of thousands of packages through the facility.
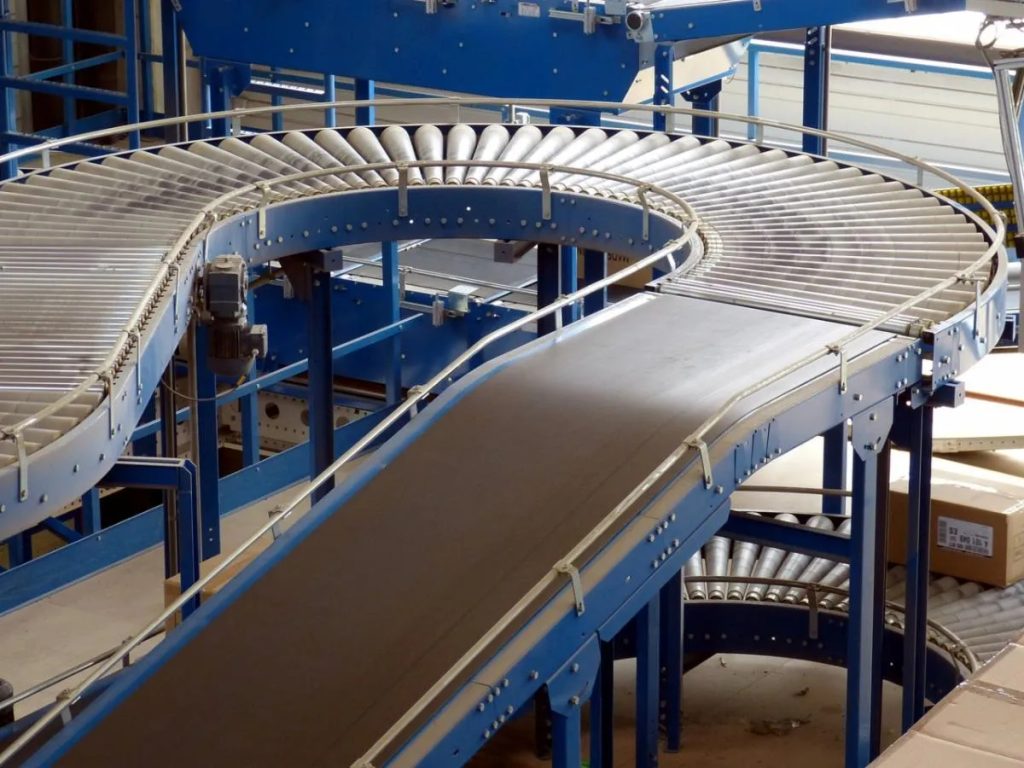
Facing this volume of packages daily, the courier company has encountered challenges in its operations. These challenges are listed below:
- Frequent motor winding failures due to high reflected wave differential voltage.
- Motor bearing failures caused by circulating bearing currents.
- Common mode voltage leads to numerous gearbox failures.
- Frequent drive faulting and tripping, disrupt the sorting process.
- With each failure, increasing downtime and rising maintenance costs resulted in significant financial losses.
Solution and Results
Following a thorough evaluation of the installation and identified issues, the team proposed the installation of a 480V, 2A SineWave Nexus motor protection filter on the most problematic drive conveyor system. This filter was designed to address both differential and common mode issues, providing a holistic solution to the client’s challenges.
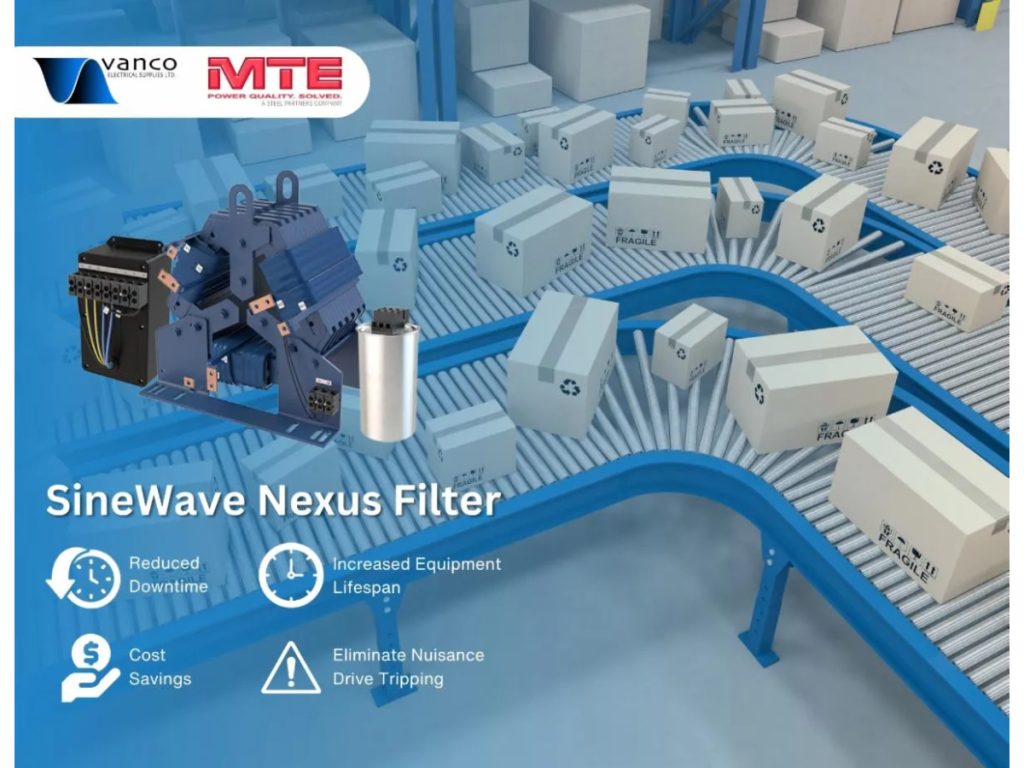
The implementation of the SineWave Nexus motor protection filter yielded substantial improvements, transforming the distribution system’s reliability and efficiency:
Significantly Reduced Downtime:
- Drastically minimized disruptions caused by motor and gearbox failures.
- Reduced downtime to 1-2 hours per incident, a significant improvement from previous instances.
Increased Equipment Lifespan:
- Extended life of conveyor gearboxes, motors, and motor cables.
- Mitigated damage to motor windings and bearings, leading to enhanced overall system durability.
Cost Savings:
- Lowered costs associated with production downtime.
- Reduced expenses related to maintenance labor and motor repair/replacement, resulting in substantial overall cost savings.
Elimination of Nuisance Drive Tripping:
- Virtually eliminated drive faulting and tripping, ensuring uninterrupted sorting operations.
MTE Corp’s SineWave Nexus motor protection filter proved to be the definitive solution for the global courier company’s distribution challenges. The successful implementation led to a significant reduction in downtime, increased equipment lifespan, and substantial cost savings. The elimination of nuisance drive tripping further underscored the effectiveness of the SineWave Nexus in enhancing the reliability and efficiency of the client’s distribution system.
More Infromation
For more information on how MTE can benefit your distribution or supply chain operations, please click the button to learn more.
Available at Vanco Electrical Supplies – Certified Distributor of MTE
Source: MTE – Warehouse and Logistics Success Story
Related Story
Maximizing Motor Efficiency: Navigating the Impact of VFDs on Motors
Running a motor directly from the power source produces uniform, sinusoidal waveforms but wastes energy due to continuous speed operation regardless of the load requirements. To enhance efficiency, variable frequency drives (VFDs) control motor speed, reduce energy consumption, and minimize equipment wear. However, VFDs use pulse-width modulation (PWM) to supply electrical pulses instead of a true voltage waveform, generating harmful harmonics that can damage motors, cables, and bearings.
Choosing the right level of motor protection is crucial for reliable and efficient operation. MTE offers a family of application-engineered products designed for the performance you need. This article will explore the options available to help find the right level of motor protection you need for you application. For application support, contact Vanco Electrical Supplies Ltd. and they are happy to help.