MOVI-C® Modular Automation System from SEW-Eurodrive
February 6, 2024
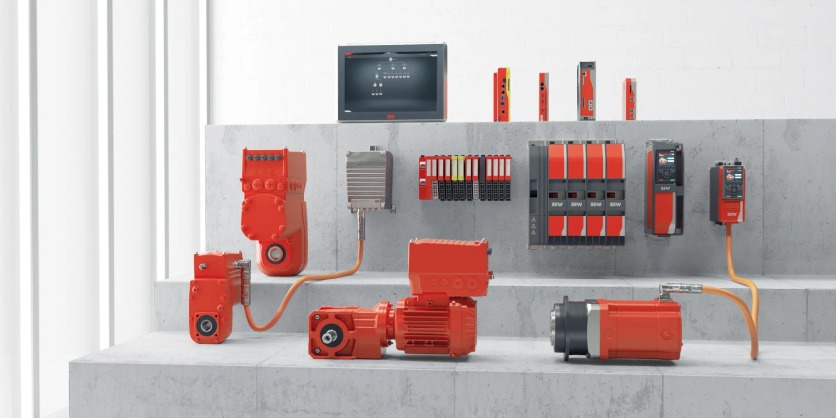
MOVI-C®, the modular automation system for all-in-one solutions from a single source
MOVI-C® is the all-in-one solution for automation tasks. Whether you want to implement standards-based single-axis or multi-axis applications, particularly complex motion control applications or customized automation solutions, MOVI-C® can help you do all that and give you the scope to achieve optimum automation for new projects.
Your benefits: MOVI-C® is the all-in-one modular automation system from SEW-Eurodrive. This end-to-end solution from a single manufacturer covers all your needs – planning, commissioning, operation and diagnostics software, electronic control and monitoring devices, mechanical drives and gearmotors. There is only one place you must go to for all the automation components you need. Naturally, all components can be fully integrated into all automation concepts, fieldbus topologies and network standards. You have complete freedom when it comes to the communication topology, as MOVI-C® harnesses all communication advantages – from PROFIBUS and Industrial Ethernet to Modbus and, in the future, OPC UA.
MOVI-C® offers automation and a whole range of benefits from a single source – specifically, a company that is both an automation specialist and a manufacturer.
MOVI-C® in use
Since its debut at the SPS IPC Drives trade fair in November 2016, SEW-Eurodrive have also captured the highlights of the new MOVI-C® modular automation system in moving pictures. Interested in finding out more? Then join them on a short journey into the future of automation by watching this video.
Four modules – one solution: Complete automation from a single source
MOVI-C® – the all-rounder for any topology
1) Topology for single-axis automation
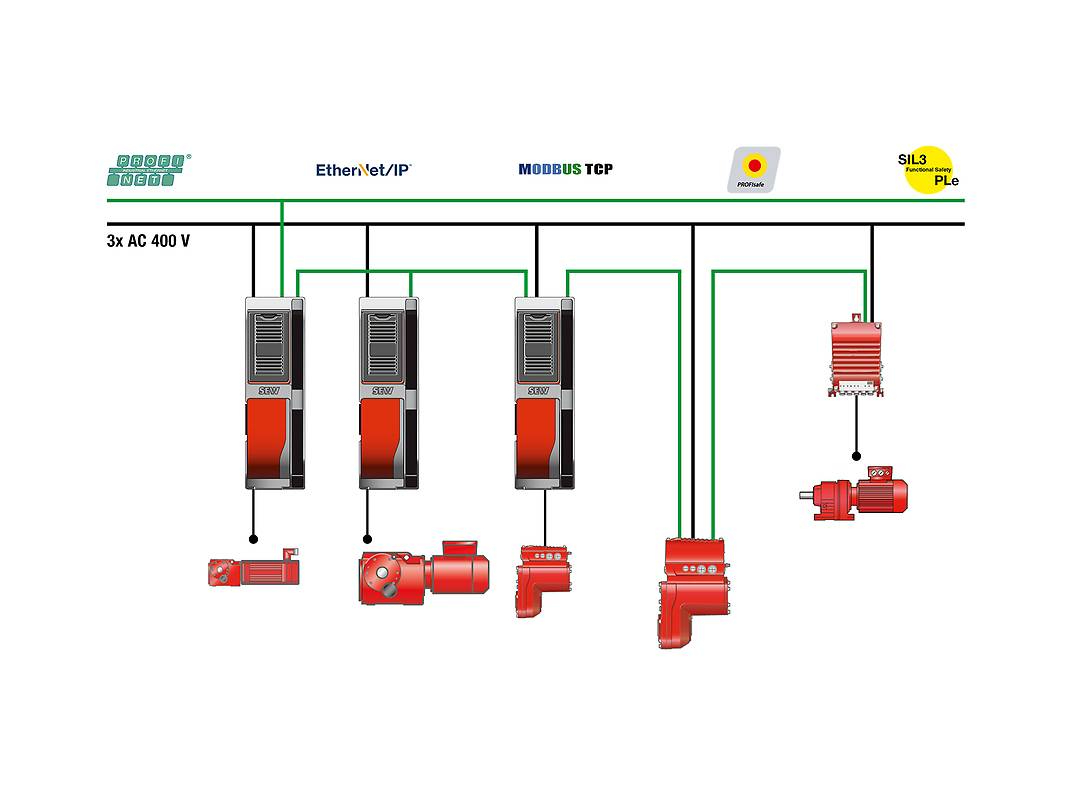
The MOVIDRIVE® technology application inverter and the MOVIGEAR® performance and MOVIMOT® flexible mechatronic drive system are connected directly to the higher-level master via fieldbus interfaces. Predefined MOVIKIT® software modules ensure the drive function can be quickly and reliably implemented using graphical editors. Each axis is controlled individually via the network. Data is stored via a data exchange function on a memory card in the application inverters and in the decentralized units.
2) Topology for motion control
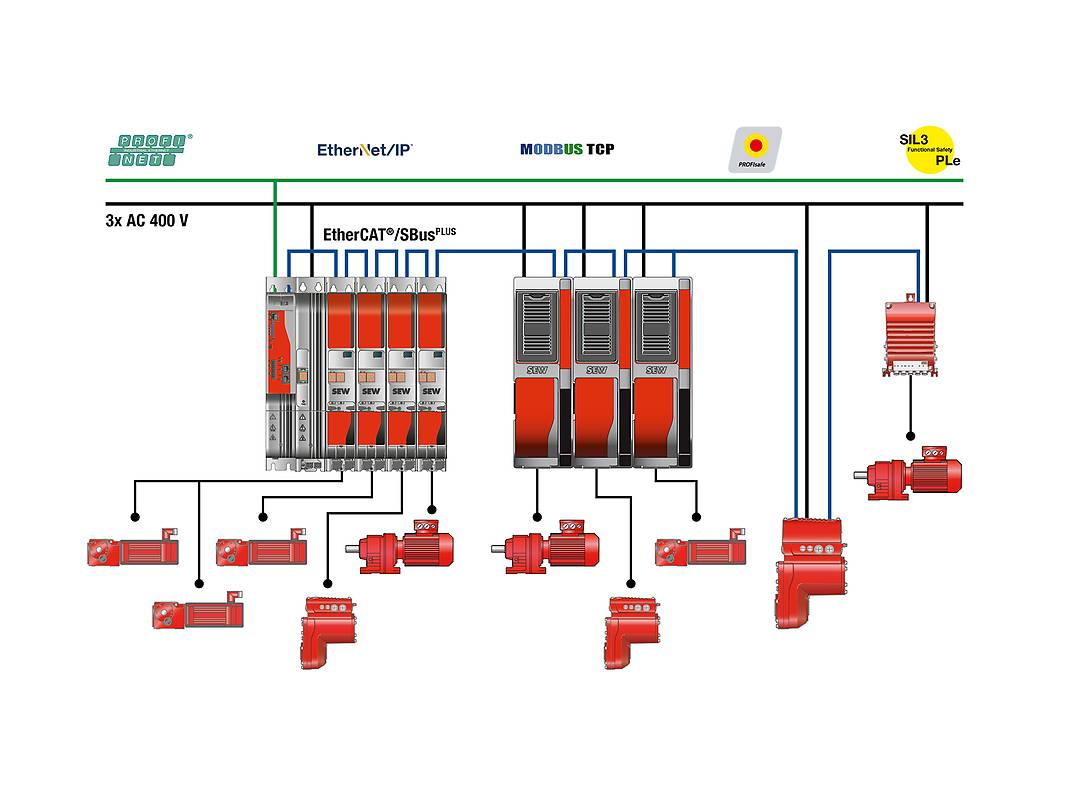
The MOVIDRIVE® modular and MOVIDRIVE® system application inverters and decentralized peripherals such as the MOVIGEAR® performance mechatronic drive system and MOVIMOT® flexible have a real-time-capable connection to the MOVI-C® CONTROLLER via EtherCAT®/SBus PLUS.
The MOVI-C® CONTROLLER receives setpoints for single-axis motions or coordinated motions from the higher-level master via the fieldbus. The MOVI-C® CONTROLLER determines the setpoints for the connected application inverters, thereby taking care of tasks such as phase-synchronous operation, electronic cam function or kinematics. Predefined MOVIKIT® software modules are used to implement the motion control drive function quickly and reliably with the aid of graphical editors. Thanks to more than 50 kinematic models, many mechanical configurations are already covered. New functions for kinematic models can be custom-made by SEW-Eurodive. Data is stored via a data exchange function on a memory card in the MOVI-C® CONTROLLER.
3) Topology for module automation
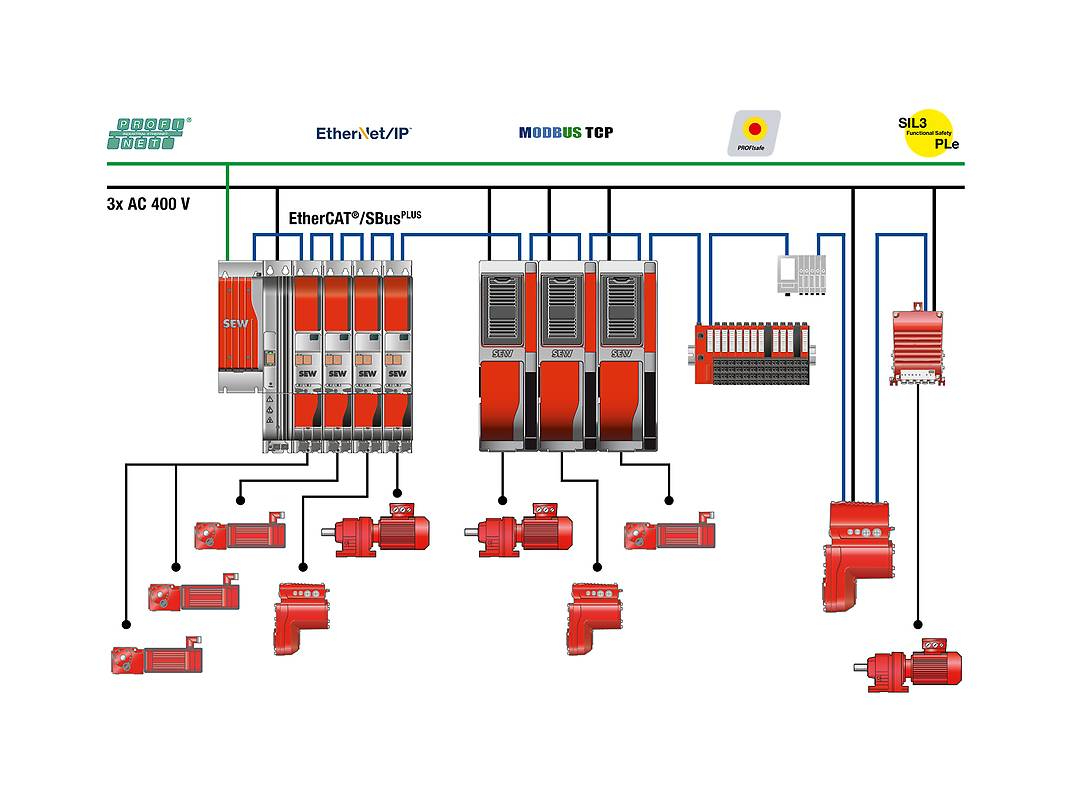
All drive functions of the motion control topology are available in the module automation topology. In addition to the graphical editors for the drive functions, automation tasks associated with the higher-level master controller can also be implemented in part or in full in a straightforward and flexible approach using the programming system (IEC 61131) in the MOVI-C® CONTROLLER. To support automation, any EtherCAT® devices can be integrated centrally or decentralized in addition to the MOVI-C® application inverters and drives.
4) Topology for EtherCAT® motion slave
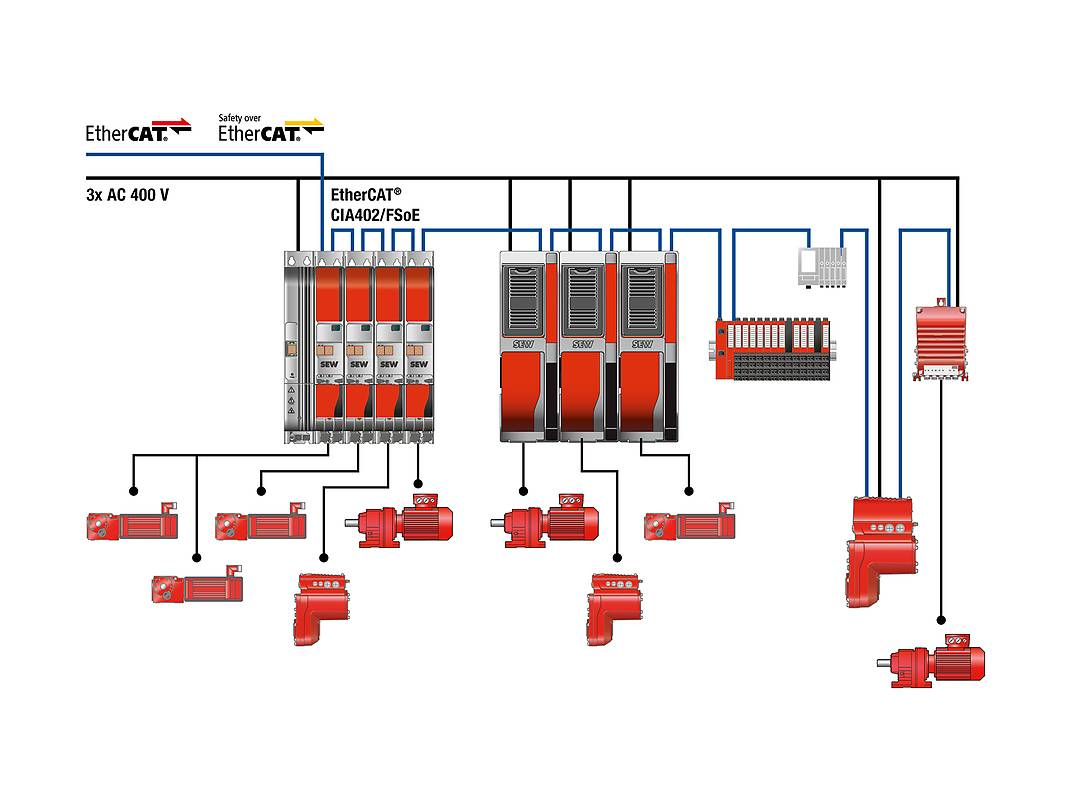
The CiA402 profile for controlling inverters has established itself in plants with highly specific motion control applications that are calculated in the higher-level master controller. To support control via CiA402, the application inverter MOVIDRIVE® modular, MOVIDRIVE® system and the mechatronic drive system MOVIGEAR® performance and MOVIMOT® flexible can be connected directly to the controller via the integrated EtherCAT® interface. This means integration into the higher-level controller can be achieved particularly quickly and easily and does not require extensive conversion work. More sophisticated safety functions can be triggered via FSoE directly from the safety control system.
In all topologies, the higher-level master controller uses safe communication to activate safety functions that are executed in the MOVISAFE® CS..A safety card in the application inverter, in the mechatronic drive system MOVIGEAR® performance and in the MOVIMOT® flexible.
Related Product
A Clear View Ahead for Industrial Gear Units. DriveRadar® from SEW-Eurodrive
Considerable investments are made with respect to industrial gear units, and given this expense, it is reasonable that the owner or operator expects excellent system availability and improved productivity. It is not always possible to predict downtime and be able to prevent unscheduled maintenance. What if there was a way to get a clear view ahead, a way to achieve proactive maintenance and avoid costly breakdowns and even preventative maintenance? What if this solution was possible for not only new industrial gear units, but existing ones as well?