IO-Link Valve Connector for Smart Valve Control from Pepperl+Fuchs
January 9, 2024
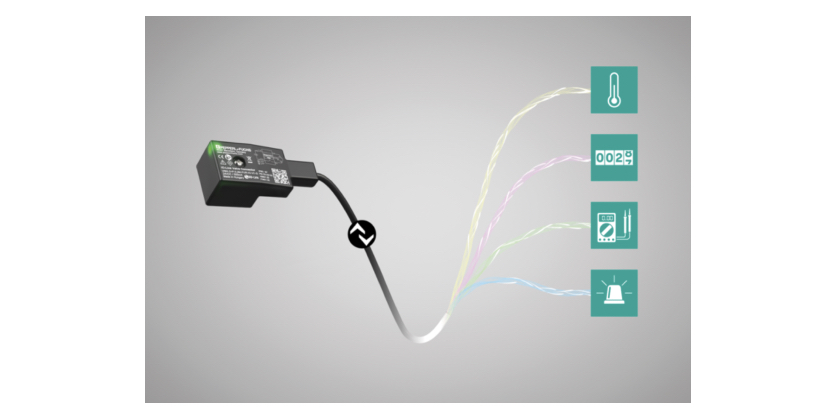
More intelligence in the plant: This is what the manufacturer-independent communication standard IO-Link stands for. From machine and plant engineering to material handling, IO-Link is widely used in modern factory automation. In addition to IO-Link masters, Pepperl+Fuchs offers a wide range of IO-Link-capable sensors. However, the standard is also suitable for monitoring and controlling actuators such as valves. As the latest addition to its connectivity portfolio, Pepperl+Fuchs now offers a valve connector with an IO-Link interface. This device allows plant operators to keep an eye on the status of their solenoid valves at all times.
IO-Link Interface for Condition Monitoring and Predictive Maintenance
The valve connector of design A is suitable for connecting pneumatically or hydraulically actuated solenoid valves—for example, individual, critical valves in IO-Link environments with high monitoring requirements. To monitor the status of these actuators, the connector records extensive diagnostic data: Supply voltage, output current, valve movement, temperature, and power consumption of the solenoid coil. Individual limits can be set for each parameter via a configurable alarm function. Lead breakages and short circuits are also reliably detected. Furthermore, a resettable switching cycle counter can be used to monitor specific intervals in the product life cycle. A second, non-resettable counter makes it possible to keep track of the entire service life of the valve.
All process data is passed on to the controller or a cloud-based system via an IO-Link master—for example, via a device from the ICE* series. In this way, the valve connector provides all the data needed for condition monitoring and predictive maintenance. This solution, which is also ideal for retrofitting existing plants, turns any standard valve into a smart device that can be fully integrated into Industry 4.0 environments.
Longer Service Life Due to Power Save Mode
To further increase the service life of the valve, the valve connector can be operated in power save mode. By pulse width modulation (PWM), the output current can be controlled depending on the valve type. As a result, energy reductions of up to 70% can be achieved. This also lowers the temperature at the valve, eliminating the need to install cooling devices and significantly extending the service life of the valve.
Increased Convenience during Installation and Maintenance
The valve connector is supplied with a pre-assembled M12 connector. This allows it to be connected directly to the IO-Link master without having to assemble a cable on site. Since each valve connector can be individually named in the software, it is easy to assign the data to the respective connector or valve. Moreover, a programmable LED status indicator simplifies maintenance: the “Find me” function allows valves to be identified quickly and easily. The event-related programming of the LED means that the current status of the valve can be identified at first glance. In addition, all device settings are stored in the IO-Link master, eliminating the need for time-consuming parameterization when replacing a device.
Highlights of the IO-Link Valve Connector
- Increased plant availability: reliable condition monitoring due to various digital diagnostic data via IO-Link
- Individual control of the output current in PWM mode enables energy reduction of up to 70%
- Short response times in the event of maintenance due to configurable alarm function when defined limit values are exceeded
- Event-related LED for fast status display and identification of faulty valves directly in the plant
- Complete solution from a single source—extensive IO-Link portfolio for any requirement
More Information
Related Product
Exceptional Performance in PLC-Based Applications from Pepperl+Fuchs
The new ICE11 IO-Link master for PLC-based applications is multiprotocol-capable and now supports not only PROFINET, EtherNet/IP, and MODBUS TCP but also EtherCAT and CC-Link IE Field Basic. It can be used worldwide in various application areas such as robotics, intralogistics, and motion control applications.