Upgrading Legacy Control Systems to Current Technology Using Schneider Electric’s Solutions and Guillevin Automation
November 28, 2023
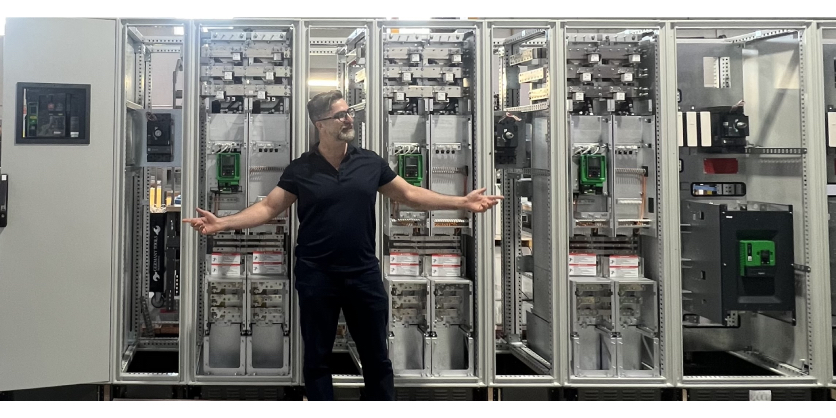
When a legacy control system is no longer supported by the manufacturer, an upgrade is required. To facilitate an easy migration, Guillevin Automation can assist you in this process with the right products and solutions.
Guillevin is one of the latest and oldest distributors of equipment used for electrical, automation, and health and safety applications in Canada. For over a century, Guillevin has partnered with leading manufacturers to bring customers the best products and solutions in their industry. Muzen Zurar, Automation Manager at Guillevin, discusses upgrading legacy control systems to current technology using Schneider Electric’s solutions.
What is a ‘legacy control system.”? How “old” does it have to be to be considered legacy?
“A legacy control system is typically a control system that is no longer supported by the manufacturer. “This is often due to new technologies that have come out, and software associated with it that meets the expectations of the current market. Typically, most hardware is supported for 25-30 years, and there is a large overlap between the new products that would take its place,” says Zurar. Like any device, such as a smart phone, at some point, the manufacturer is going to stop producing and supporting it. This is the same idea for a control system.
We are in the technology era right now. Rapid advances in hardware and software are accelerating what is possible in virtually every industry. People want more out of less. They expect devices to be smarter and more connected than in the past. They want to see things moved to the cloud, and they want them to be future proof. Many devices from a decade or two ago are not on par with today’s standards and will eventually have to be upgraded. To help navigate the process of upgrading, some manufacturers will label their products based on their age to help customers understand their lifecycle.
Terminology such as ‘active product,’ or ‘active, mature product,’ or ‘end of life product,’ and finally ‘obsolete’ can help customers identify where a product is in this cycle. “Once the product is obsolete, there is no guarantee that you will be able to replace it as the manufacturer is no longer producing them. A global company like Schneider shelves products even at their obsolete stage through their service team; however, you tend to pay much more as the demand continues to grow on these items,” says Zurar.
What are some of the common challenges customers face when using legacy control systems? Is there a common “trigger” that brings operators to want or need to upgrade?
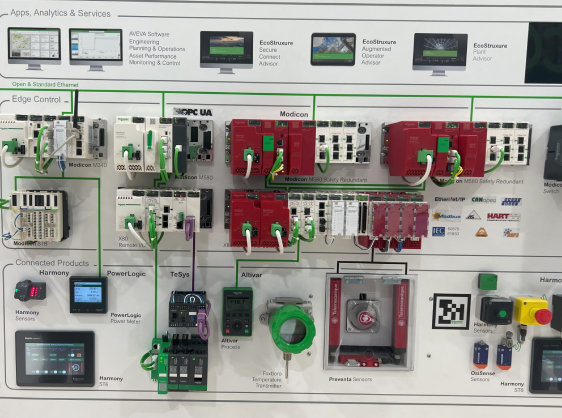
As a product approaches obsolescence, facilities are going to experience challenges. There could be increases in maintenance costs, increases in the cost of spare parts because manufacturers are making less of them, or not making them at all, and demand drives up the price. “The most common triggers are hardware or software obsolescence, or lack of new features required to improve overall performance, like artificial intelligence, analytics, or cybersecurity,” says Zurar.
“Industrial protocols that are no longer available may cause another issue. Our current control platforms are moving towards Ethernet and fiber, which will enable data transfer between devices to become faster and enable machines to run further away from one another without the loss of transmission. This includes easier access to information in the plant from the top level,” says Zurar.
He adds, “Gateway manufacturers continue to be successful as translators for products that are no longer being manufactured.” Sometimes, a facility will have an old system and a new system running side-by-side communicating with each other; they may not communicate in the same industrial language: one speaks serial communication and the other is Ethernet. In this case the solution is to use an industrial gateway as a translator as the solution until that option until they are ready to move towards a full upgrade.
The challenges with legacy control systems are varied, and there is not necessarily a standard solution. It often comes down to the challenges the enterprise faces, and what the owners decide as the remedy.
Does the modernization solution to migrate older system to a future ready plant have to happen in one go, or can it be more gradual? Which one is best? And what are the advantages of each?
“It really depends on the customer or the plant,” says Zurar. “A lot of times, if a plant is running 24/7 for example, it is not possible or practical to stop production. In these cases, the control system that is being used is critical, and even for scheduled shutdowns they are not shutting down every single section of the plant – they are doing it in steps. In a case like this, migration in a step pattern or partial pattern would be more beneficial than doing what is known as rip and replace.”
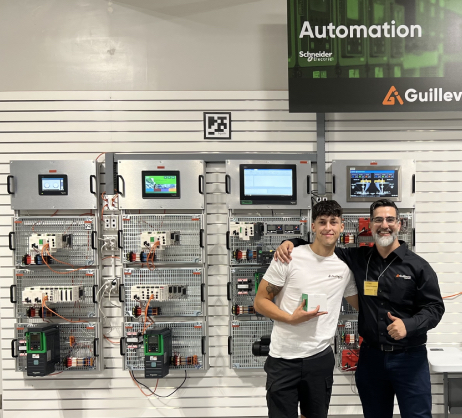
Rip and replace means a facility essentially rips out their entire old system and puts in a new one. This approach has its disadvantages. “It can introduce several errors, because everything in that system must be rewired and the connection points need to be reconfirmed. There are more unknowns and factors to consider in a rip and replace as opposed to a partial or stepwise where the integrator checks that each change is working and can continue to slowly migrate each part of the system,” says Zurar.
Anyone can choose to do a migration and do it in a way that works best for them, but often what Zurar sees in those critical applications where someone just cannot rip a legacy control system out and put in a new one is a partial or stepwise approach. He says, “Typically we are seeing [gradual or stepwise migrations] in those critical applications where someone just cannot rip something out and put it in and just close their eyes and open then and hope that nothing changes.”
As for the benefits or advantages of the different approaches to upgrading legacy control systems, Zurar says, “The biggest advantage of doing a migration in partial steps is less mistakes and errors occurring. There are fewer wiring errors all the way down, from the control to the device. However, the disadvantage of a partial migration is that part of the old system will still be in place while doing the migration. What does that mean to the plant? It means it could end up using more real estate. Perhaps the plant doesn’t have a lot of extra room to add a new system side-by-side with the old system. In this scenario, real estate could become an issue.”
The overall cost of the upgrade could become a disadvantage as well, Zurar says. “Because now you are using more product to do this migration. However, this cost is outweighed by the potential costs that could be involved in terms of rewiring the entire system when everything must be ripped and replaced.” He offers a balanced piece of advice: “Overall, [in terms of cost], I would say migration is a lot better – but it all depends on how people are thinking. Are they thinking of operating expenses or capital expenses? It really depends on the customer and the plant.”
It also depends on how critical it is for a customer or a plant to run a particular section that needs to be upgraded. What kind of time frame is available to make the changes and run the test? Zurar has seen scenarios when his integrators go into a plant where there is a small window of time to upgrade, and doing the migration in steps is easier than ripping everything out and replacing it because it takes a lot of time to test all the wire points.
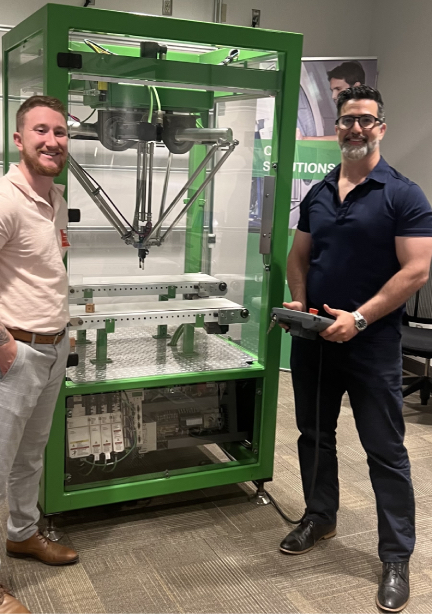
What are the major steps or aspects of a migration process? And how do your manufacturing partners make it safe, seamless, and simple?
“The first step is always going to be an audit to understand the products in place, and the network of all control systems that may be dependent on its communication,” says Zurar. This involves going to the plant and doing an audit of exactly what needs to be done: What devices are connected? What are they connected to? This is done to get a good understanding of the environment that is about to change. “Because once you are committed to that change, it is important to make sure that everything is properly connected into this new system that is going to be put in place,” he adds.
“The next step would be to consider everything that is really going to upgrade, including the software that is inside the controller. A lot of old legacy controls are using different software to do the programming; when the conversion is done off site, it is important to make sure that the integrator tests this off site to make sure that things work properly, comparing the new program to the old program. And from there, it is [up to the customer to decide] whether they utilize the migration steps and the tools that our suppliers have to create the migration, or if they do the rip and replace,” Zurar says.
Migrations are safe, quick, and reversible. Schneider Electric has software that pre-converts programs and pre-tests hardware before a migration is performed. Rarely, and under very specific circumstances, if this process needs to be reversed, legacy parts can be replaced quickly due to wiring adapters that maintain the original wiring. “It’s not just putting the new control system into the old one and hoping for the best,” Zurar says. “They have tools in place that can use to switch back over to the old system if something is not right or the changes are not made properly.”
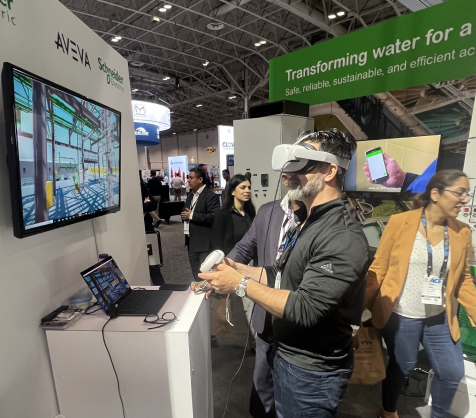
Schneider Electric also has software that they can use, and that they also sell to integrators who specialize in upgrading legacy controls that can convert old, legacy programs into a newer platform. “And this is not just Schneider to Schneider software. They have software that can convert a different vendor’s software to Schneider software,” says Zurar. “And, before doing that conversion, Schneider has other tools that can be used to run checks and determine how much of the conversion has been done. It will give you a percentage of how much of a conversion it has done: 100% conversion or 90% conversion, for example.”
Zurar says, “This is a useful tool because, sometimes in legacy control systems, there is unconventional logic that may not be 100% converted. Therefore, it is helpful for the integrators to see what has been converted rather than writing a new program from scratch, along with the new controls and any other products that have to be installed to upgrade the system.”
How have Guillevin Automation’s manufacturing partners simplified wiring solutions to make upgrading legacy control systems faster and easier?
As a distributor, Guillevin Automation has partnered with many leading manufacturers that offer solutions in this industry. Weidmüeller, another of their suppliers, has developed a solution to simplify wiring when upgrading a legacy control system. Zurar says, “They developed a migration kit that eliminates the need to pull any wires from the control system to put them in the new control system. They have developed what they call marshalling cables from the old system up to the new system, and a rack-type system that accommodates the old I/O terminal blocks.”
“You can still get rid of the whole old system, but where it is wired to the terminal blocks stays in place where they develop a connector to marshal the wires that go to the new system. They have really simplified wring when you are doing a partial, or step-by-step migration phased approach,” says Zurar.
This solution from Weidmüeller was developed in their engineering facility in Markham, and they can develop a new control system using any vendor’s old legacy system, and they will build and test all the wires in-house to make sure it works properly and make life easier. “They even use the right gauge of wires based on the I/O that the new control system is going to, and tag all the wires based their audit to make sure that every I’O point is clearly understood. This is done as you will find in an old control system, there are no tags, and no indication about what wire is going where,” says Zurar.
Weidmüeller offers two solutions: their bridge solution and their in-rack solution. The in-rack solution is where the new control system sits on top of the old wiring arms. A disadvantage here is that it creates a slight depth due to a small metal structure underneath where the old wiring arms sit, so, if there is not space in the panel, this might not work. Because Weidmüeller anticipated this space concern, they also developed their bridging system, which brings the marshalling cables (whatever length needed and even to another panel or anywhere inside of the panel) to wherever the new control system is.
What are Schneider Electric’s control system solutions? What are the top three, and what are their features and benefits?
Schneider Electric has a vast family of controllers and distributed control systems. Focusing on Schneider Electric’s larger control system solutions, the top three in Zurar’s opinion are:
- Modicon PAC (part of the Modicon family)
- Foxboro DCS
- Triconex
The Modicon PAC is highly scalable and flexible. It uses a variety of different programming languages that are native to the control system itself, meaning there is no need for a gateway or gateways as it can connect across all different platforms, such as SCADAS, EcoStruxure, Aveva, Wonderware, and others. Foxboro DCS is an innovative family of control components, and consolidates critical information to ensure flawless, continuous plant operation. Triconex is the gold standard in safety instrumented systems.
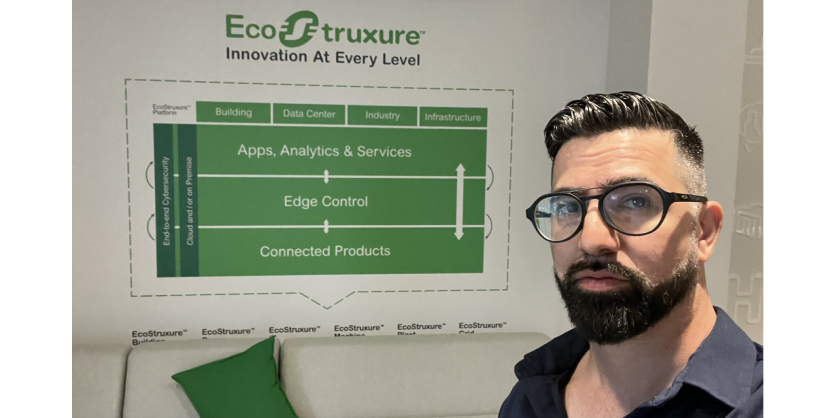
What can you tell us about Schneider Electric’s EcoStruxure? What is it and what does it do? How does it help upgrade legacy control systems and how is it futureproof?
One of Schneider Electric’s newest control systems is their EcoStruxutre Automation Expert. It was released in the Canadian market in June of 2023 and has been designed to connect everything in the automation environment. Zurar says, “It is a new control system that is essentially pulling control away from the hardware – It is hardware-agnostic. You can put it on a physical piece of hardware such as a PLC, or on a software-based PLC, such as a computer or server.”
“If a PLC or something goes down, you can start running your control strategy over any computer or any server, anywhere. It is not really stuck to the hardware,” says Zurar. “The international standard that it adopts is IEC-61499, many different forward thinking manufacturers are moving towards that area now, so this is something that we are going to start seeing a lot of,” he adds.
By using this communication standard, it opens the architecture and is indifferent to what kind of industrial protocol a control system is using. In this way, EcoStruxure provides the core capabilities for connectivity with intelligence by connecting the field devices on the factory floor to the control systems all the way up to analytics. “Even if you have a ‘dumb’ device down on the floor, EcoStruxure enables you to bring data up, utilize it, and bring it all the way up to the analytical side, whether it be hosted on premise or in the cloud,” says Zurar.
Additionally, EcoStruxutre Automation Expert like all of Schneider’s software/hardware solutions has built-in cybersecurity that keeps evolving to protect the customer. Zurar says, “Schneider focuses on end-to-end cybersecurity to ensure that, by utilizing this layered approach and their products, the customer is always protected and that no threats from the outside world can penetrate this system.”
What Schneider Electric control systems and related products does Guillevin have in stock today?
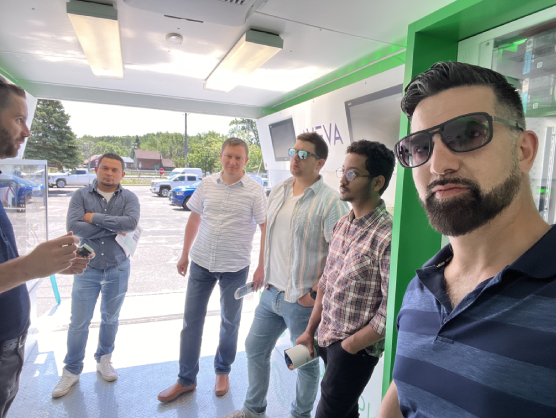
Guillevin stocks the entire portfolio of Schneider Electric industrial automation products, amongst others. “We have over 100 locations across Canada. Most, if not all our locations, are stocking locations,” says Zurar. “This includes all the PAC controllers such as the M580s, M340s; their PLCs, all the machine-level PLCs and the machine safety controllers, as well as the vast variety of different HMI’s.”
“Also, the VFD’s and servo drives that we stock is another big one to mention. I cannot mention all the smaller components, but pretty much everything in the Schneider industrial automation umbrella, Guillevin stocks. And, we have over 100 locations across Canada to help customers out with not only supply them parts but supplying them support.”
Guillevin operates on a decentralized business model, which allows them to best serve their customers. For example, there are 27 locations in Ontario. All their branches are forward-thinking with respect to customer service. Zurar says, “We have a system that can see all our locations, what their inventory is for each product, and what people bought a particular product for, which helps optimize their inventories. I like to buy things in bulk and get a better price.”
“People say, ‘Oh, you bought this at a better than normal cost!’ And we transfer it at the same cost, we do not try and make money off anyone, and they get to take advantage of that with their customers that they are looking to develop. And not only are they rescuing their customers, but they may also even be getting them at a discounted price.”
Where can the customer turn if they need assistance upgrading their legacy control system?
Customers can turn to any Guillevin location, and they can bring in their internal experts. Depending on the size or time frame of the project, they can then bring in a representative from Schneider Electric’s service team, or one of Guillevin’s local partners. They have specialized integrators that are specialized in various industries and know Guillevin’s systems and the process of that plant.
“For example, integrators specialized in food and beverage, we like to introduce them to clients in the same industry. We can then say with confidence, ‘These businesses understand not only our system but the processes that are in place.’ We’ll bring those people in as well. But the first call is us. We are the guys on deck.”
What else should customers know about upgrading their legacy control systems to current technology using Schneider Electric’s solutions? And what else should they know about Guillevin Automation?
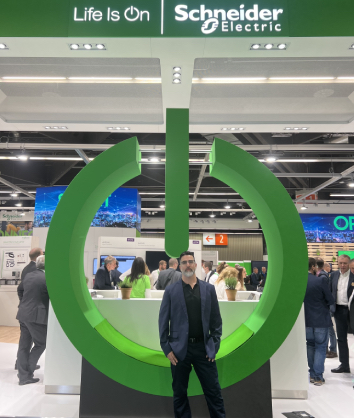
When it comes to upgrading a legacy control system, Zurar says that it is very important that people start the conversation as early as they can. “You never know what one piece of that control system could go down, and if [the manufacturer] cannot get that part, the [customer] needs to have a plan in place. The sooner that they get a team like Guillevin involved, and understand what we can do for them, and what our partners can do for them, the better.”
Schneider Electric and Guillevin can give their customers free audits of their plant. Zurar says, “We can go through their plant at no cost to give owners and operators an understanding of every electrical control panel. We can create a bill of materials, and a life expectancy of every product in their plant. Getting us involved, and getting an understanding of everything that is in [their plant] is important.”
“A lot of big clients do not know what is and where. Not until a process goes down, and then it becomes a 911 call. Do not wait for that 911 call. Try and be a bit proactive. See how we can make your life easier, even if it is not for today or tomorrow, at least you understand what you could potentially do, and how you can mitigate all those risks.”
“Companies and industries are becoming more proactive; not only are they looking for the newest features in general, but also because manufacturers are slowly pushing away old products and bringing in new products. It is important to move with the waves,” says Zurar. Guillevin has an automation team in all their major sectors. Zurar is the Automation Manager in Ontario, and he has counterparts in British Columbia, Alberta, and Quebec. They have major manufacturing partners from coast to coast, Schneider Electric being one of them. No matter where a customer is in Canada, parts will be available.
“Understanding that is a big value to a lot of our customers, they need to know a little bit more about Guillevin’s Automation team and how we partner with common manufacturers. We have training facilities across the country for automation. In this location, where I am, we have a very large lab that customers can come to and get comfortable with our products. We will do training on site and in-house, and we will even do remote training for customers to get them familiar with our products,” says Zurar.
More Information
Related Story
Guillevin Automation: What You Need to Know
Every industry wants to be more productive, and automation is necessary to help customers achieve this, making Guillevin Automation a great partner for industry. Guillevin Automation has many years of experience helping their customers with any automation challenge, and offer the latest technology to make them more productive. In this article, we shed more light on Guillevin Automation and what they have to offer.