The XPlanar Greatly Increases Testing Capacity and Throughput
Flexible final inspection for I/O terminal production from Beckhoff
May 25, 2023
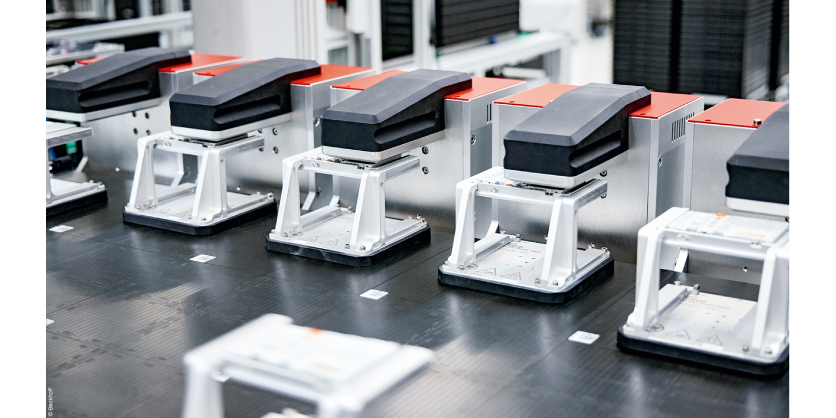
In the fall of 2021, Beckhoff began to completely rethink the way it carried out final inspections of I/O components with Xplanar. Its aim was to significantly increase testing capacity and throughput, even though many different types of terminals are produced. The system, which was created entirely by the company’s own equipment manufacturing department, can program, adjust, and test around 10,000 terminals per shift fully automatically. The high speed and flexibility are the result of not only the sophisticated system concept, but also the intelligent XPlanar transport system, PC-based control, and the wide range of EtherCAT Terminals.
“Keeping pace with the growth that Beckhoff achieves year after year.” This was and remains a challenge for Michael Golz, head of the demo systems department, and his approximately 40 employees, who are responsible for building the operating equipment, among other things. They have taken a completely new approach to the system for final inspection of I/O terminals – with the XPlanar as a transport system, specially developed firmware programmers, and test stations with universal test cabinets.
“On average, a fully tested I/O terminal that is programmed with the appropriate firmware leaves the system every 3 s,” stresses Michael Golz, “regardless of the type of terminal and the order in which they are delivered.” Currently, over 200 different types of terminal can be programmed and tested on the system. The number of different types present in the system also has no impact on the output rate of 10,000 terminals per shift.
It seems like Beckhoff is trying to square the circle, particularly as, depending on the type of terminal – with/without FPGA, a controller, or with analog channels – programming and the subsequent function test take different amounts of time. “It can take up to 30 s for the firmware to be installed and all analog channels to be adjusted,” explains Stefan Engelke, who developed and programmed the test cabinets together with his team.
The solution to this time issue lies in the parallelization and separation of the firmware installation on the one hand and the function tests on the other. This is not a groundbreaking idea in itself; the pioneering element is the systematic use of the XPlanar’s degrees of freedom for the entire internal logistics and in feed of the terminals to the workstations. Due to the free 2D movement of the products, it is irrelevant whether a single bus terminal needs to spend 10 s or 1 min in a tester. The remaining movers simply go past the occupied stations to the next free station. The overall output of the system is therefore unaffected by individual delays.
Easy, flexible, and transparent handling
“The process is nevertheless very simple,” says Michael Golz. “The operator doesn’t have to set up anything; all they have to do is place a stack of trays with terminals at the in feed station and press a button.” The stack then enters the picking station, where a delta robot picks up the modules from the trays and places them individually on the waiting XPlanar movers. The system has two main paths, almost like high-ways, leading left and right to the programmingand testing stations.
The stations are located at exits or parking bays on the side of both lanes. Between the lanes, there is a third path where all movers return to the picker. This symmetrical set-up has the advantage that even if an entire half of the system fails, the other side can continue to operate.
The movers pass the terminals under a reading station through to the lateral programming stations. The reading station captures the individual Code (BIC) of each terminal by means of multiple cameras and Beckhoff Vision. “After that, the system knows the terminal type and does everything completely autonomously – programming, adjusting the analog channels if necessary, and function testing,” adds Ulrich Brockhaus, who is responsible for system programming. At the same time, the BIC is “married” to the mover via its ID. This means that the mover ID can be used to track the location of each individual mover or terminal, even after a power failure.
When the mover has reached a free programming station, it positions the terminal precisely under its contact pins. Then, depending on the BIC, the corresponding firmware is loaded onto the terminal.
It then moves on to one of the universal testing stations, which in turn calls up the device-specific test sequence based on the BIC. If the software has been loaded correctly and the function test reports no issues, the mover transports the terminal to the picking station’s second delta robot, which places the terminal on another tray, via the middle track. The mover passes through the reading station a second time, only this time in the opposite direction.
“The terminal is booked out via the renewed capture of the BIC on the return track, and the installation of the firmware and the function test of each individual terminal are documented in the central database, including all adjustment values in the case of analog terminals,” Stefan Engelke states.
All XPlanar degrees of freedom used
The basis for this flexible yet fast process is an XPlanar system consisting of 100 tiles. “We built the two main paths with two outbound lanes and the return track in the middle from six XPlanar base sets, each containing 3 x 4 tiles,” says Michael Golz. For the add-ons (programmer and tester), the remaining 28 tiles are screwed onto the side of the basic system. Each mounting position has a standardized interface with power supply (400 V AC), safety, Ethernet (LAN), as well as EtherCAT. “The interface and the system layout enable future expansions without major conversion work,” emphasizes Daniel Golz, who is responsible for the mechanical design of the system and the specific details for terminal contacting.
XPlanar makes machinery modular while also simplifying mechanics in many sectors. For example, the programming stations use XPlanar’s XY precision positioning. Therefore, immediately after reaching the exact position, programmers can lower their pins onto the terminal contacts and start loading the firmware.
At the test stations, another XPlanar feature reduces the design work: the variable flight height. When it arrives at the test station, the mover lifts first so that the slide-in unit of the test station can move under the terminal. Then the mover lowers its hovering level again, and the terminal then rests on the slide-in unit and is drawn into the tester. The benefit of this is that all contacts are freely accessible and can be contacted. After the test, the terminal is then placed back on the mover in reverse order.
The option to rotate the movers comes into play again during insertion and removal. It is used to rotate the movers by 180°, depending on the side of the system used. “This feature has also significantly reduced the mechanical complexity and has made space-saving configuration of the tester and programmer on both sides possible in the first place,” points out Daniel Golz.
Overall, the system layout benefits from four XPlanar properties:
- The 2D product movements individualize transport of the terminals and facilitate parallel processing in the programming and testing stations.
- XY precision positioning means there is no need for a handling system at the programming stations.
- The transfer of the bus terminal with the aid of the Z movement (lifting/lowering) replaces complex mechanics in the test stations.
- 360° rotation enables the mirror-symmetrical set-up of the system.
Taking a closer look at the electrical and optical functions
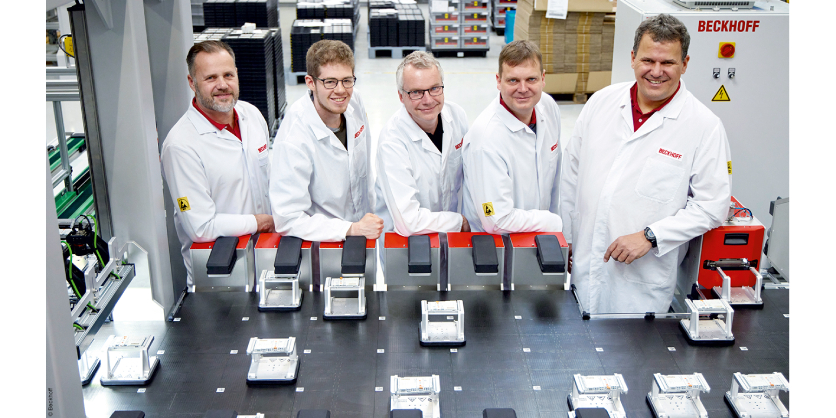
The testing stations don’t just check the electrical properties and functions of a terminal. “For terminals with analog signals, the corresponding test sequences and calibrations are included too,” says Stefan Engelke. An integrated vision system also checks that the prism is present and in the correct position and measures the colors and intensity of the LED.
A very wide range of EtherCAT Terminals, with their diverse functions and measuring ranges, can be tested fully automatically on the system, and this is all thanks to the universal test cabinet. Its complete measurement and testing technology is based on Beckhoff technology, with a focus on the precise measurement terminals from the ELM series. Mounted in mobile cabinets and coupled to the system by means of a plug connector, the test cabinets can be replaced quickly, without shutting down the entire system. This needs to be performed regularly, since the ELM terminals are measurement devices which must be re-calibrated and certified in specific cycles.
The strengths of PC-based control are also evident in the overall coordination and evaluation. If a tester detects a discrepancy on a terminal, this is registered via the BIC while the tester sends the terminal back to the programming stations for reconfiguration. However, if error messages accumulate on a programmer or tester, this indicates a malfunction. “In this case, the tester is reported to the system as unavailable and this position is no longer approached by the movers until the tester has been examined and, if necessary, replaced,” says Ulrich Brockhaus.
Although the system will then run with one station less for a short time, it is still up and running and not significantly slower. “An I/O terminal that could cause any problems for a customer would not leave our system,” adds Michael Golz.
The system is a prime example of how PC-based control can be used to perform a wide variety of tasks and functions. In addition to a C6670 control cabinet industrial server, which coordinates the 33 movers on the 100 tiles, a total of ten C6032 ultra-compact Industrial PCs control the other system components. The delta robots are automated with the AX8000 multi-axis servo system and AM8000 servomotors.
“We use the AMI8100 integrated servo drives to infeed and eject the trays because they are extremely compact and only require EtherCAT and 48 V voltage to operate,” says Ulrich Brockhaus.
AA1000 linear actuators are used by the programmers to contact the terminals; AA3000 electric cylinders are also used by the testers to feed in the terminal carriers. The entire safety technology is implemented with TwinSAFE. TwinCAT Vision captures the DataMatrix codes. Around 40 EtherCAT measurement terminals from the ELM series are installed in each of the four test cabinets. In addition, a wide range of EtherCAT Terminals from the EL series are also used. Michael Golz says, “PC-based control has made a lot of things easier for us in this project and leaves us the option for further expansions.”
Michael Klasmeier, head of I/O production at Beckhoff, adds, “Our I/O terminal portfolio comprises a wealth of products, from 2-channel digital input terminals to compact drive technology, with differing levels of complexity, which are produced in annual quantities ranging from a few thousand to hundreds of thousands of units. All of our products are produced locally in Verl, East Westphalia. Our objective is increase production output with our current employee numbers and in the space available, which is impossible without automated testing.”
Michael Klasmeier, head of I/O production at Beckhoff
More Information
Related Product
Beckhoff Expands Power Supply Portfolio with Supplementary PS9xxx Modules
The new PS9xxx buffer and redundancy modules extend the universal 24/48 V DC power supply series from Beckhoff. These new modules provide more efficient options to avoid machine and plant downtime and, as a result, increase system availability. With the supplementary PS9xxx modules, the PS power supply series and the CU81xx UPS series, Beckhoff offers a complete and coordinated range of solutions for reliable power supply in the 24 and 48 V DC range.